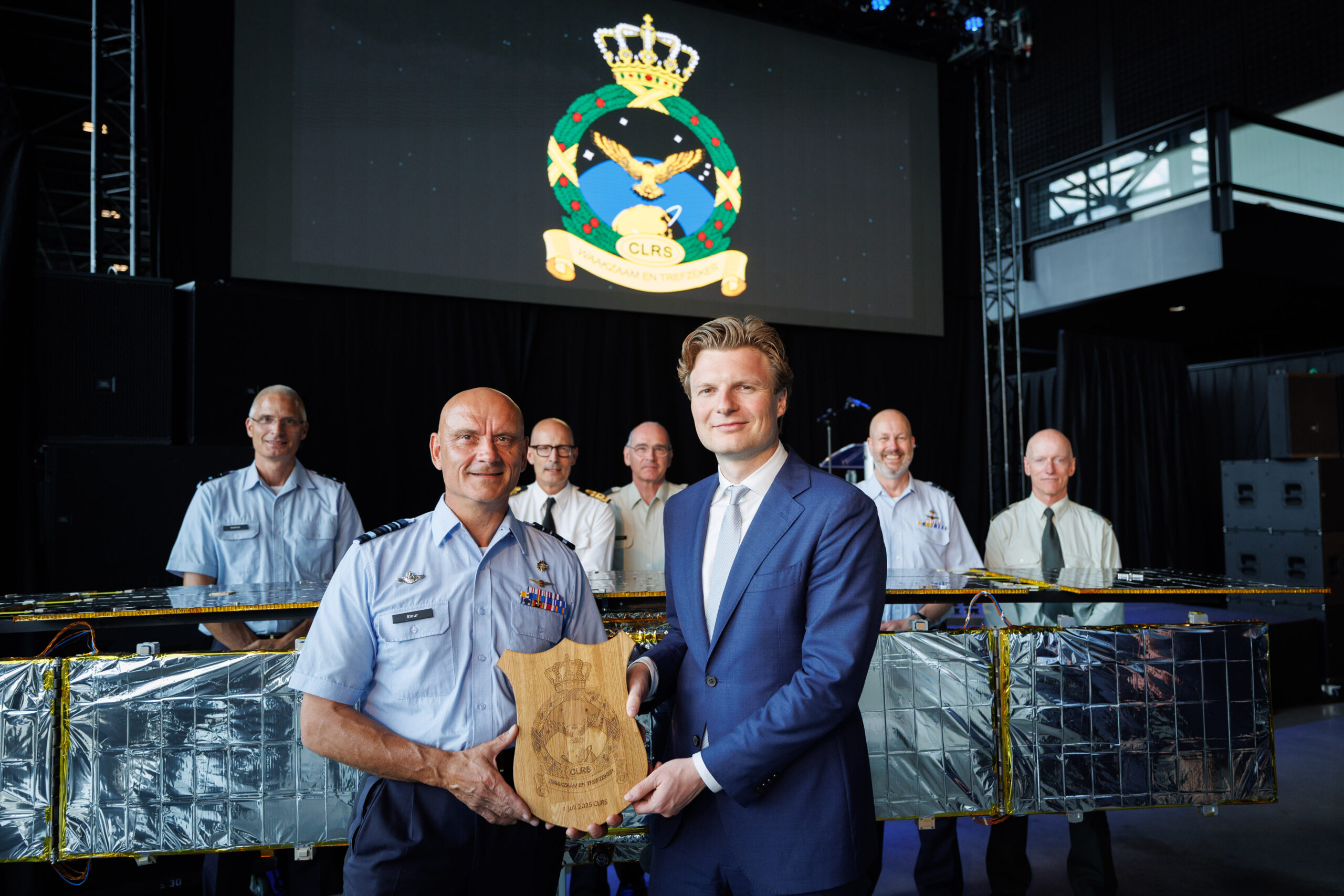
Defence and Security
02 July 2025
A new chapter for the Royal Netherlands Air Force: 112 years of history and a leap into the future
Yesterday, the Royal Netherlands Air Force (RNLAF) celebrated its 112th anniversary. In addition, the name of the Air Command (CLSK) is changing to Air and Space Command (CLRS). The name change means that space exploration is becoming more prominent within the Dutch defence. For NLR, this strong commitment by the Air Force to space power […]
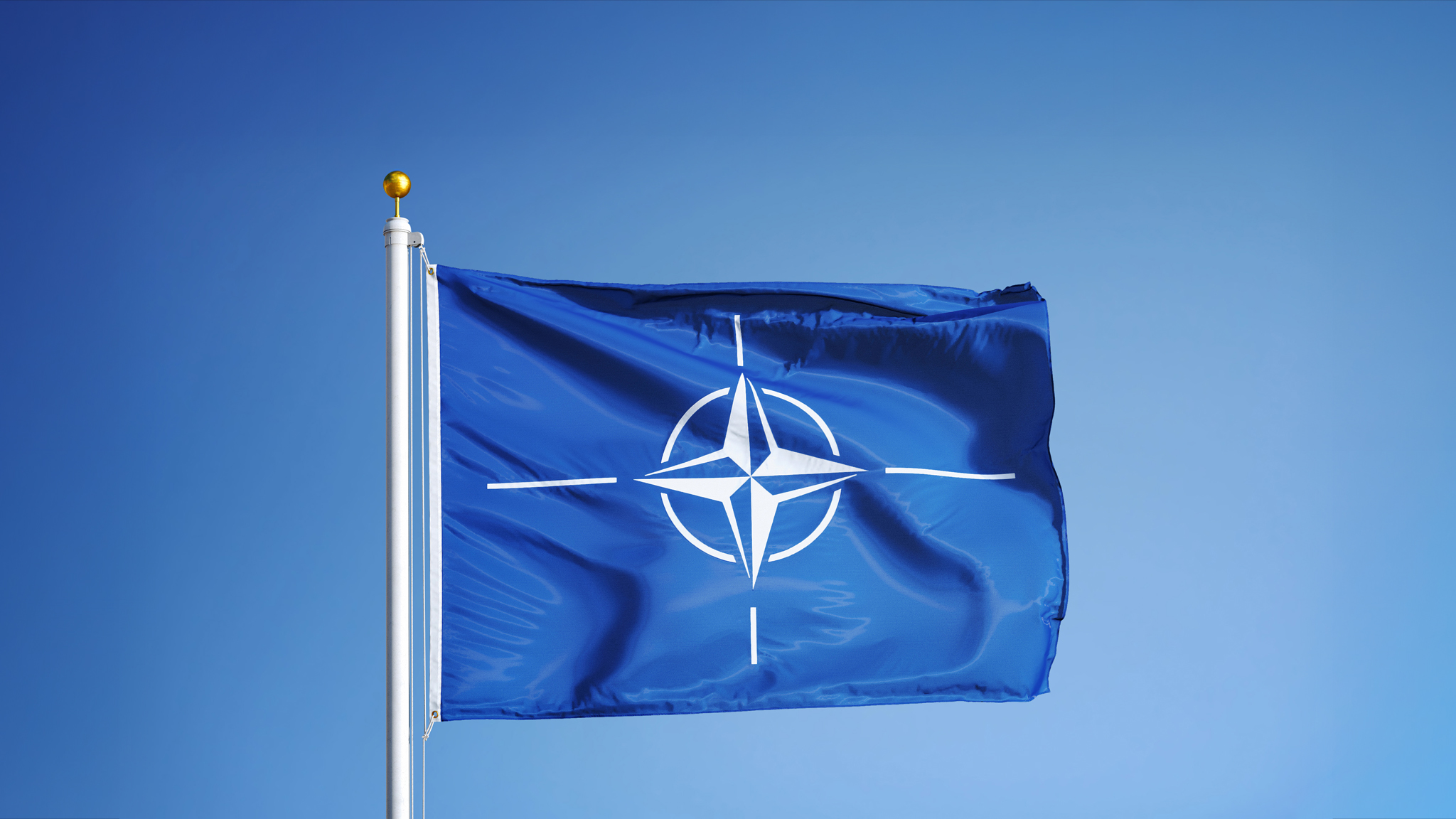
Defence and Security
24 June 2025
NLR plays crucial role as partner between government and industry during NATO Summit
23 June 2025 – During the NATO summit in The Hague, Tineke van der Veen (CEO) and Martin Nagelsmit (CTO) of NLR attended the NATO Summit Defence Industry Forum (#NSDIF), where defence ministers from NATO countries were present alongside experts and industry representatives. The forum focuses on improving cooperation between NATO and the defence industry. […]
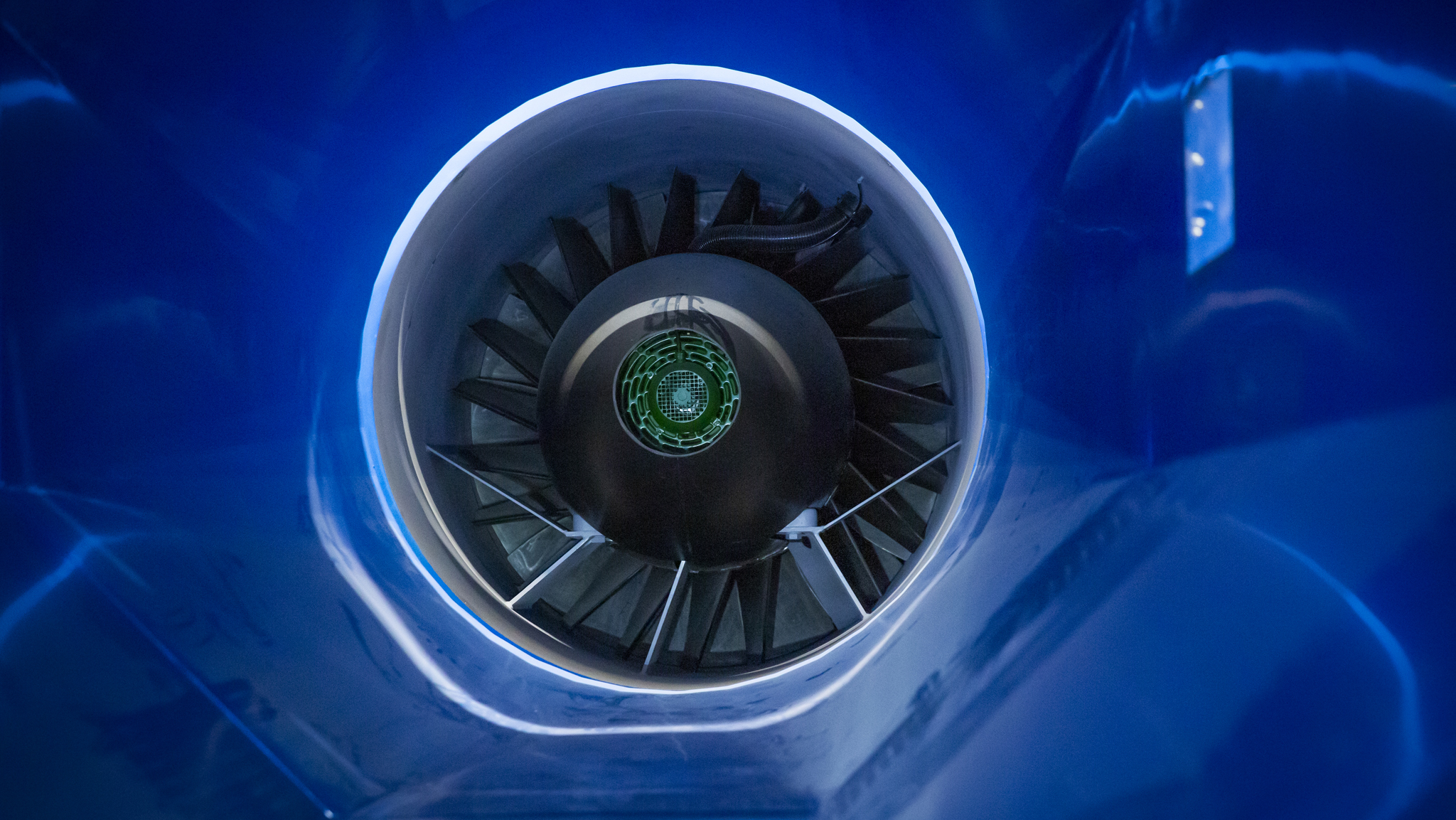
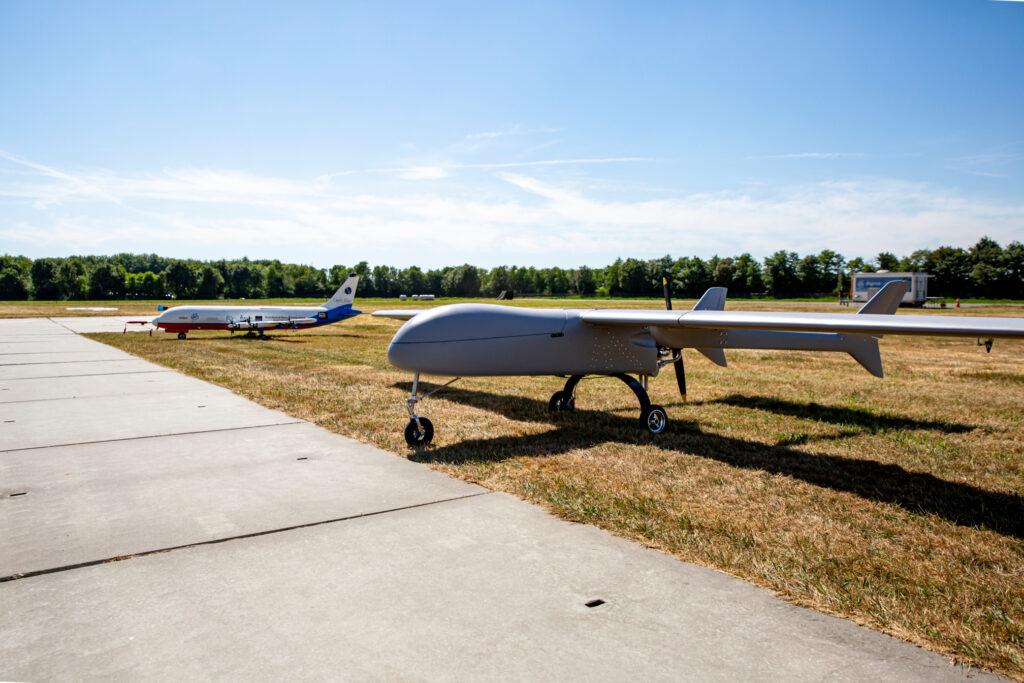
Defence & security
Accelerating drone research for Dutch Defence: the strength of an ecosystem
AGENDA
Let’s meet!
5 Oct
ESA/ESTEC Open day
6-7 Oct
SAMPE Europe
8-9 Oct
Electric & Hybrid Symposium
14-16 Oct
MRO Europe
18-20 Nov
Space Tech Europe
10-12 Mar
JEC World
Areas of expertise
Programmes
Markets
NLR Repository
Newsroom
Stay up to date with the latest developments. In the Newsroom you can find the latest news, articles, and blogs from NLR. We also showcase a range of videos and publications here. For more video content, please visit our YouTube channel, NLRmedia.
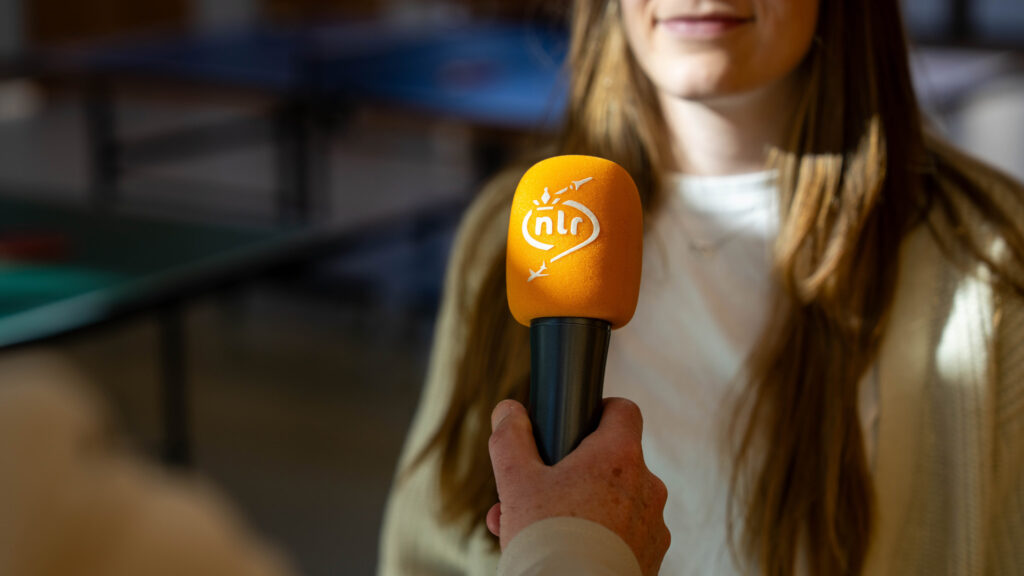