The global aviation industry is committed to reducing global net aviation carbon emissions by 50% by the year 2050, with the European Commission pursuing a more ambitious goal of a 75% reduction in CO2 emissions per passenger kilometre. Alternative fuels such as liquid hydrogen (LH2) are seen as playing a central role in a zero-emission future for aviation. To store cryogenic (20 K) liquid hydrogen in an aircraft, the COCOLIH2T project carries out research and testing for the design, manufacturing and testing of storage containers for new and existing aircraft designs.
The challenge
- Design, manufacture and demonstrate a full-scale composite conformal storage tank for liquid hydrogen at TRL4.
- LH2 tank capacity: 57 kg LH2.
- Gravity index: > 25%.
- No liner.
- Venting rate: < 2% per day.
- Subsystems for gauging, refuelling and monitoring structural health for safe functioning.
The solution
- Perform material testing at 20 K, permeability tests and microcrack investigations to select a suitable composite material.
- Design an inner and outer tank including hoses and valves for safe fuelling and de-fuelling. Designs must be able to absorb internal pressures due to boil off, flight and sloshing loads.
- Design and testing of sensors to monitor LH2 levels, H2 leakage, vacuum and pressure levels.
- Manufacture all individual parts and assembly them in 2 demonstrators.
- Test 2 full-scale demonstrators with LH2 to validate the requirements at TRL4.
What did we do?
In collaboration with the project partners, NLR made an initial design of a thermoplastic, composite conformal tank which fits in an ATR-72. To determine static material properties at 20 K, NLR executed a static test campaign in their cryostat. A permeability test was developed and microcracks were investigated. The 2 demonstrators, which will be manufactured by partners in the project, will be
tested with large amounts of liquid hydrogen in NLR’s newly built Energy to Propulsion Test Facility (EPTF). Test set-ups are being designed and manufactured by NLR to perform the required tests to validate the design and sloshing models. Test and safety procedures are being compiled and reviewed to ensure that the tests are executed safely.
Project partners:
Collins Aerospace Ireland (project lead), Royal NLR, Unified International, TU Delft, Novotech, ATR, Microtecnica, UTC Aerospace Systems Wroclaw, Goodrich Aerospace SAS, Crompton Technology Group Ltd, Simmonds Precision Products Inc.
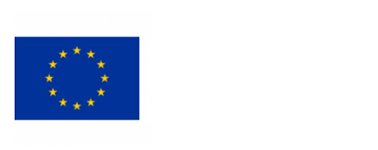
Co-funded by the European Union. GA no 101101961