Instrument Landing Systems (ILS) at airports are periodically calibrated using an aircraft equipped with a Flight Inspection System, such as the NLR Citation II research aircraft. If the ILS works well, and the transmission is free from disturbances, some periodic measurements can be carried out from or near the ground. This comprises Reduced Flight Inspection (ReFI). The main benefits of ReFI are 65% lower calibration cost, 90% less environmental impact (noise, emissions), and higher runway availability. The ground measurements can be carried out via Drone Flight Inspection (DFI). Therefore, NLR has developed DFI.
The challenge
To reduce the impact of periodic ILS flight inspections on airport operations and the nearby community. The goal is to apply Drone Flight Inspection (DFI) and to achieve approximately 90% less flight inspection runs, and 65% less ILS calibration cost.
The solution
Royal NLR is developing a NLR-DFI system to apply ReFI with DFI, based on an RPAS equipped with the capability for accurate positioning, ILS signal reception, and data processing and communication.
What did we do?
In order to minimise development cost, NLR acquired a robust industrial drone, an industrial ILS analyser, and an industrial RTK GPS navigation solution. NLR designed dedicated ILS antennas and industry manufactured these. We developed in-house DFI processing and control software, reusing as much as possible Open Source code. The DFI for ILS signal reception was optimised by using synthetic materials where possible (e.g. propellers, undercarriage). All DFI runs have been designed and verified in-house. All DFI runs can be flown in automated flight mode, ensuring repeatability of the results.
The testing of the DFI system and preparation for the validation has taken place in spring 2023, the operational level demonstrations were carried out in the fall of 2023.
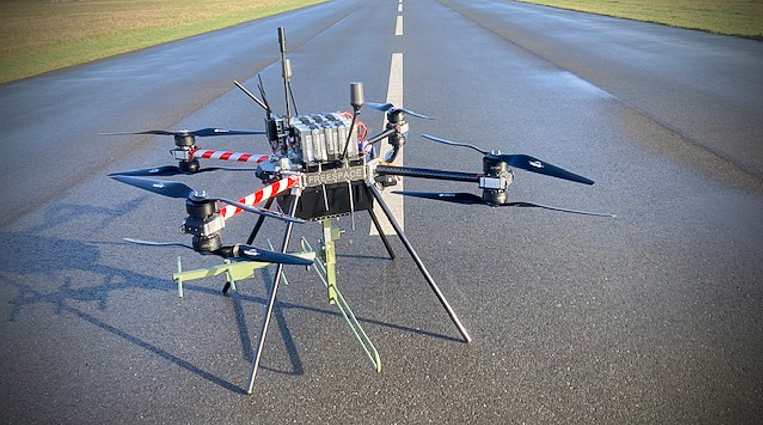
Project partners:
Research organisations: NLR