The SuCoHS project focusses on new structural concepts with novel multi-material composites to provide high resistivity against thermal, mechanical and fire loading. In order to achieve the project objectives for sustainable and cost-efficient high performance composite structures, the SuCoHS concept focusses on the three main topics: design, manufacturing and operation.ot grown.
The challenge
The challenge is to be able to maintain overview of individual process steps, part quality and status of equipment. Advanced monitoring and inspection of automated processes by a Digital Twin (DT) of the physical manufacturing environment could help an operator to filter all the available data supporting timely detection of production flaws, first-time right production, product quality, and delivery reliability. Additionally, all the collected data can be used for many more purposes:
- Design and optimise the production facilities and manufacturing processes
- Optimise maintenance
- Digital threads, digital product passports, and managing data on behalf of certification
The solution
Develop new materials and efficient manufacturing processes for fire and temperature resistant composites structures. Explore hybrid manufacturing processes, combining different materials and manufacturing technologies as well as sensor- and simulation- based adaptive process and quality control strategies. Perform manufacturing trials and customized material tests to guarantee performance of novel multi-material-systems.
What did we do?
New high temperature and fire resistant composites were developed with improved toughness by making use of effects from resin modification, thin ply technologies and woven fabrics. New manufacturing technologies were developed to provide tailored multi-material preforms with specific functionalities (thermal conductors/ barriers, damage resistance, integrated sensors) to enable efficient manufacturing at minimum waste.
New manufacturing technologies with integrated process and structural usage monitoring systems were validated and checked on reliability by manufacturing of representative critical details. All developed methods, designs and technology integrations were validated and demonstrated by NLR on thee use-cases: (1) High temperature nacelle component, (2) Composite aircraft interior shell and (3) Tail cone panel substructure.
Project partners:
Industry: Royal NLR, DLR, Aernnova Engineering division SAU, Apodius GmbH, Short Brothers plc (Bombardier Belfast), Fachhochschule Nordwestschweiz, L-up SAS, North Thin Ply Technology sarl, ONERA (Office National d’etudes et de Recherches Aerospatiales),Rockwell Collins (b/e aerospace UK lim.), Synthesites snc,
Transfurans Chemicals bvba, Technobis Fibre Technologies bv, Technische Universität Hamburg-Harburg
Period: September 2018 – February 2022
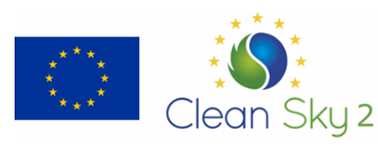
This project has received funding from the Clean Sky 2 Joint Undertaking (JU) research and innovation programme under
grant agreement No 769178.