Offshore wind energy plays a major role in the transition to green energy. The wind turbine blades require periodic inspection. The inspection and repairs are carried out by specialists who descend along the blade on a cable. This is very labour-intensive and an even greater challenge offshore. The AIRTuB consortium developed systems that are mounted on a drone and that can automatically inspect the wind turbine blade and carry out repairs if necessary. Regular inspection allows repairs to be planned in a windless period which prevents loss of production.
The challenge
Flying offshore, close to a wind turbine blade at 100 metres high with a lot of turbulence, requires high demands from the drone vehicle. When inspecting the leading edge of the blade, the drone must follow a flight path very accurately and within 2 metres of the blade. During the inspection, the drone must land on the wind turbine blade and be able to drop off and pick up a crawler with sensors.
The solution
Within AIRTUB1 a dedicated drone, inspection sensors and a crawler have been developed. The drone has an advanced flight controller and a positioning system that determines position and orientation of the drone relative to the blade. A drone has been built in which these systems will be integrated and that can carry out the inspection safely with the sensors and crawler, and follow the planned flight path very accurately in such a turbulent environment. In the first phase the drone will be flown from a ship, subsequently the drone will be resided on the wind farm.
What did we do?
NLR has built the drone, 60kg MTOM, that can transport the inspection systems and perform the inspection of the turbine blades. The drone is suitable for the hostile offshore environment and equipped with safety systems. NLR also developed a sensor for inspecting the construction. The drone has already flown with the crawler and leading
edge inspection sensor. In addition, a special undercarriage has been developed with which the drone can land on the curved (composite) blade and attach itself to the blade. The drone is ready to install the advanced flight controller and the positioning system.
Project partners:
Projectpartners: WCM, NLR, Demcon, TNO, TU-Delft, Hogeschool Zeeland, Stork, Eneco, LM Wind Power, Fusion, Stork, DCMC, Saxion, QLayers, Dutch Terahertz, InHolland
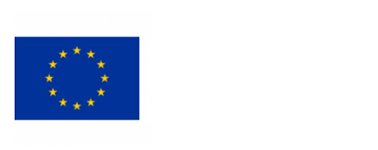
This project is funded by the Dutch Government (RVO/Netherlanda Enterprise Agency)