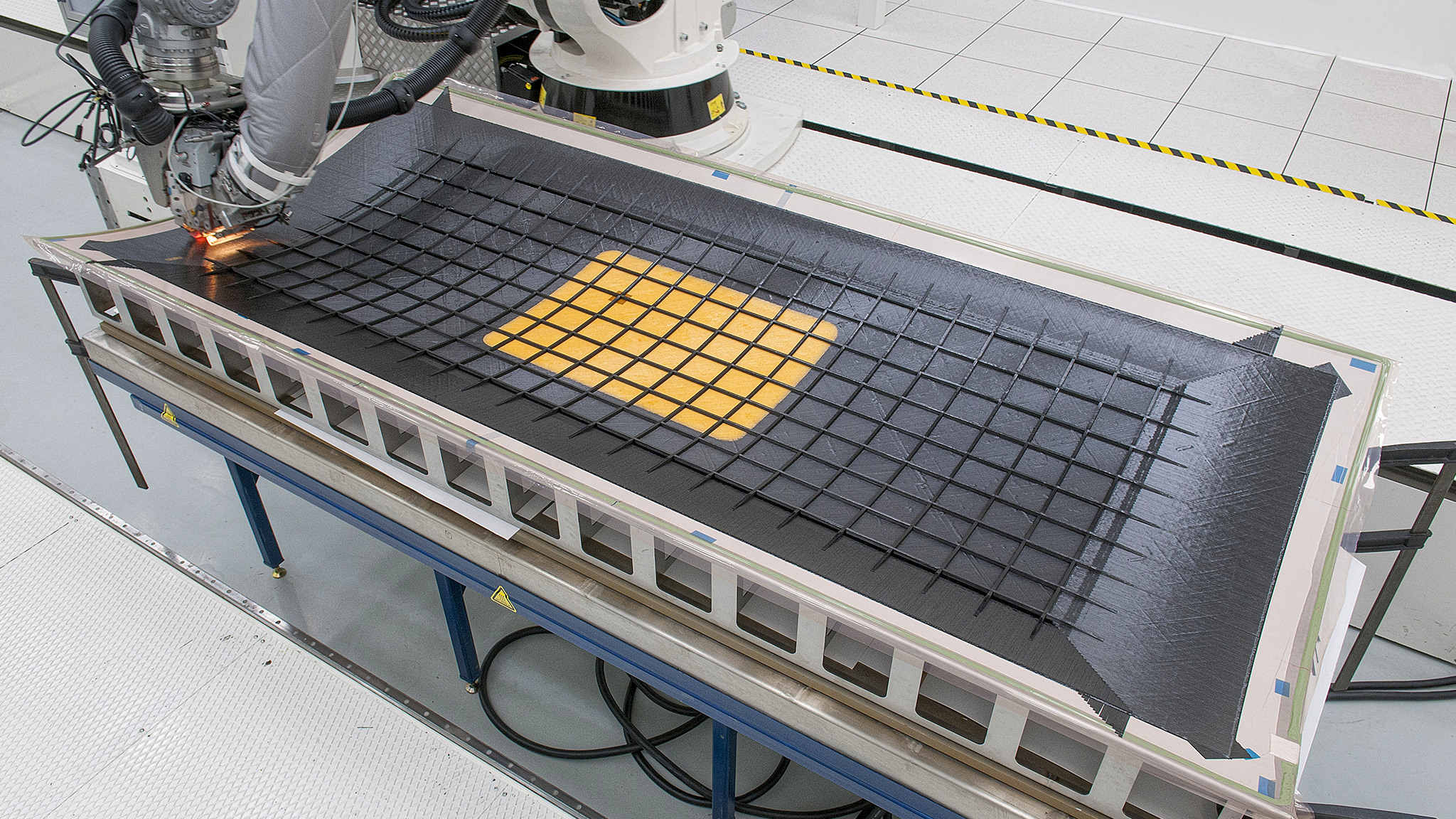
Area of expertise
Construction and Manufacturing
Society demands cleaner, quieter and safe aviation. Reducing the use of fossil fuels is one of the main challenges. Aerospace systems will therefore need to change radically. These systems are also becoming increasingly complex. With our knowledge, we develop the technological building blocks needed to design, build and operate new, efficient aircraft and spacecraft.
This includes material and manufacturing technology for various product types such as metals, composites and hybrid products, electronic products and avionics. We also design and manufacture wind tunnel models for new aircraft. In addition to developing production technology and designing products, testing and validating the products and the production process is crucial to enable certified production. We use our own state-of-the-art facilities to produce, test and qualify.
Outline of the research
Metals, composites and hybrid products
The research focuses on the development of ultra-efficient construction concepts using new materials and innovative manufacturing, assembly and disassembly techniques. Digital twinning and virtual manufacturing are part of the developments, as well as additive manufacturing technologies.
Electronics and avionics
In the field of electromagnetic compatibility, we study the effects of higher voltages and larger currents on other equipment and cabling. This is important for the high-power electronics and cabling required in electrically or hybrid-electrically powered, more climate-friendly aircraft. We study electromagnetic compatibility, including the effects on antennas in the structure. We also conduct research in the field of energy management, which is becoming increasingly important.
Avionics systems are also an important area of research, as they are a crucial part of modern civil and military aerospace platforms. They are also essential for wind tunnel testing and flight tests. The research into the correct functioning of these electronic systems is therefore of the utmost importance.
Wind tunnel models
We conduct research into material technology, sensor technology and manufacturing techniques for highly advanced wind tunnel models.
Testing and qualifying
Our research focuses on developing test methods for (new) materials and constructions based on them. We study electrochemical processes, fuel cells and electrolysers used in hydrogen applications. We test materials at both extremely low and high temperatures and we develop effective, non-destructive inspection techniques for the maintenance and manufacturing industries.
Some of our projects
TRAIL
In 2023, NLR completed its work on the TRAIL project, which aimed to design, manufacture, and deliver a high-performance, low-cost, and low-weight nacelle structure for next-generation tilt-rotor aircraft. As part of this project, a representative, complex-shaped scale model of a nacelle structure was vacuum-injected with BMI resin using a 3D-printed mould, demonstrating the feasibility of two innovative technologies. Furthermore, NLR’s mechanical testing has shown that an innovative, lightweight aerogel solution can significantly enhance the high-temperature resistance of BMI composites, particularly in cases of one-sided heat exposure, which is typical for applications such as engine cowlings, exhausts, and firewalls. The three technologies investigated in TRAIL contribute to the development of cost-effective, high-performance, and lightweight composite components for high-temperature applications.
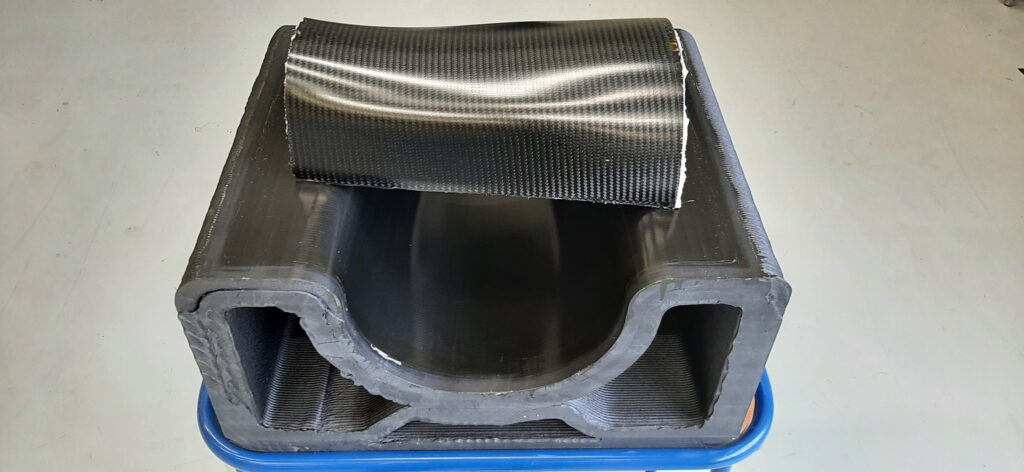
GARTEUR AG-36 aluminium metal additive manufacturing
NLR performed an optimisation of process parameters for processing high-strength aluminium alloys using laser powder bed fusion (LPBF) and directed energy deposition (DED) processes. As part of the LPBF process, a comprehensive test programme was established to determine mechanical properties, resulting in the production of 198 test specimens at NLR. The mechanical testing was carried out by Garteur’s knowledge partners. Additionally, various heat treatments were evaluated, with the selection of the most suitable heat treatment taking place in 2024.
The processing of high-strength aluminium alloys using DED is a new and challenging development. To investigate this technology, thin-walled and block-like specimens with various process parameters were produced. To select the optimal parameters, the porosity, dimensions, and roughness of these components were measured. Based on these results, mechanical test specimens were produced in 2024 using the selected process parameters, allowing the mechanical properties of these components to be determined.
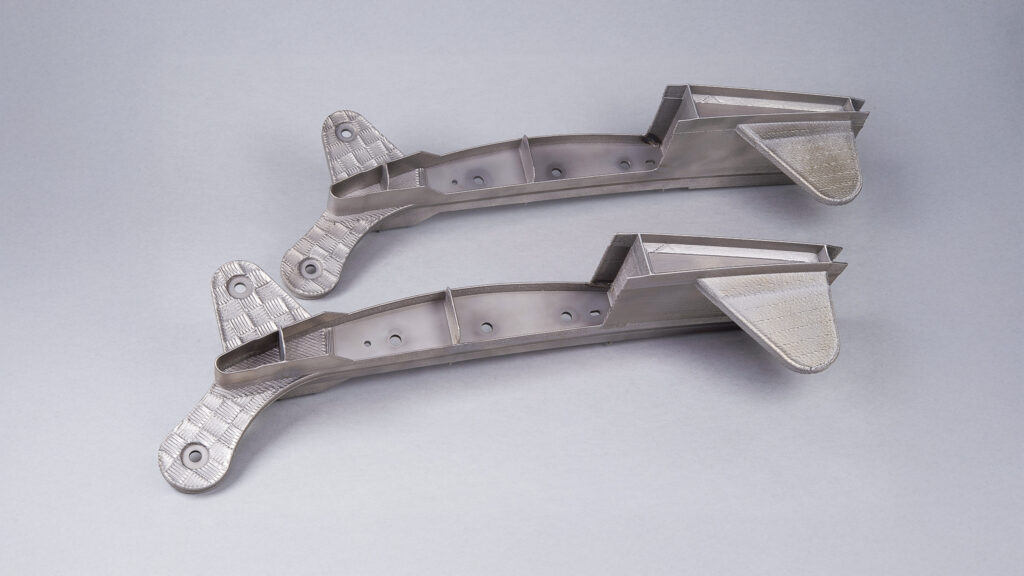
Energy management: aircraft thermal control
The development of knowledge for creating thermal control systems on board electric and hybrid aircraft involves investigating how two-phase pumped cooling systems can be integrated and optimised in aircraft concepts and specific applications such as fuel cell thermal control and high power electronics thermal control. Research was also conducted on the optimal integration of Vapour Cycle Systems (VCS) and possible combinations with two-phase pumped cooling systems. The stationary and dynamic models for two-phase pumped cooling systems were made modular to enable more effective and efficient use for trade-off analyses and implementation in platform models. A combined model of a Vapour Cycle System (VCS) and a two-phase pumped cooling system was developed to optimise the combination.
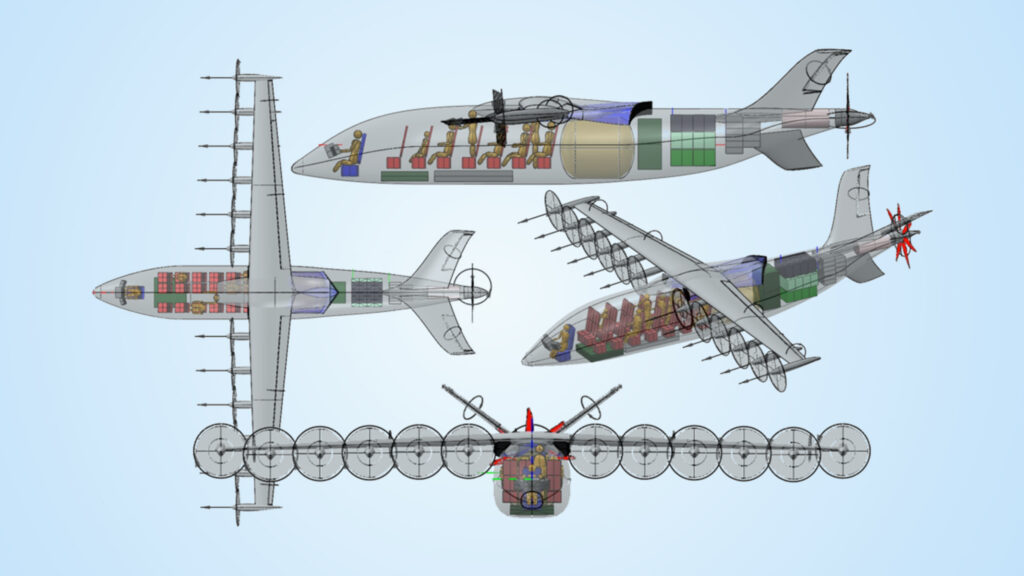