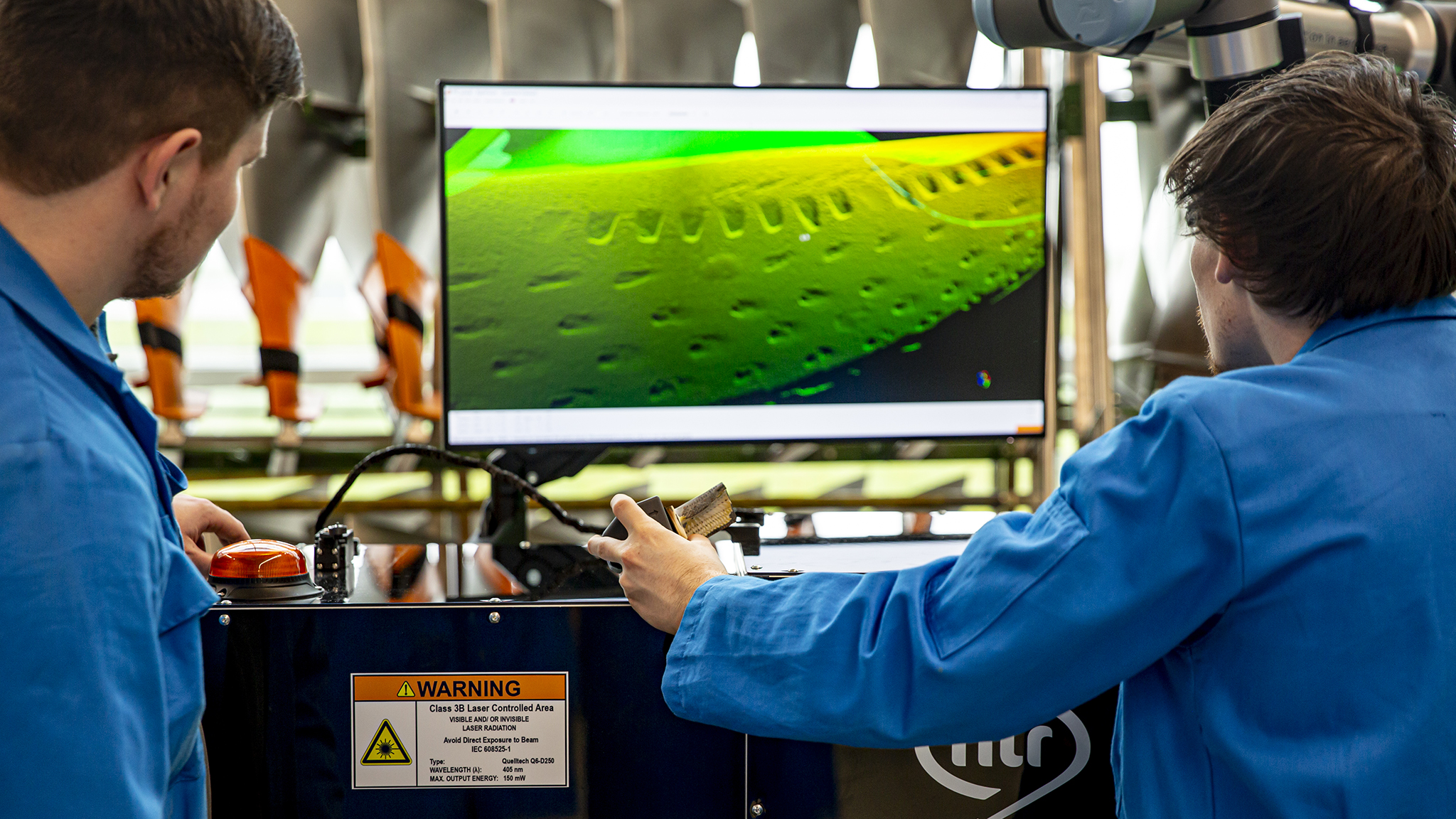
Area of expertise
Maintenance and Repair
Both civil and military aviation benefit from improved fleet availability and deployability, lower maintenance costs and sustainability. Our research in the field of maintenance and repair delivers innovative maintenance and repair solutions, giving the (Dutch) aerospace industry, operators and the air force a technological and economic advantage.
Outline of the research
Maintenance systems
With better maintenance tools and procedures, maintenance companies can significantly increase their productivity. In addition, the maintenance lead time is reduced, which also increases the availability of the fleet. With these goals in mind, we focus our research on structural health monitoring,autonomous robots and AI applications, virtual reality and augmented reality.
Our research also focuses on monitoring, planning and optimising fleet availability and affordability. In addition, we conduct research into maintenance concepts for aircraft powered by electricity or hydrogen.
Platform integrity and life cycle monitoring
With regard to predictive maintenance, we look specifically at aircraft life cycle monitoring and maintenance, as well as platform integrity. Platform integrity is the determination and modelling of the failure behaviour of aircraft structures, engines and systems such as powertrains and hydraulic pumps. To this end, we develop knowledge and technology to safeguard and improve the airworthiness and sustainability of aircraft structures, engine components and systems, and to conduct damage and accident investigations.
Structures testing & evaluation
In order to optimally support the aircraft industry and aircraft users, NLR evaluates new structures and materials. This provides information about the most critical locations in the structure where improvements may be required. It also generates data for inspection and maintenance schedules throughout the operational life of the structure. We also develop new analysis and inspection techniques for metals and composites. Finally, we investigate how maintenance companies and the manufacturing industry can use non-destructive inspection techniques. This allows the detection of defects that were previously difficult to detect and can drastically reduce inspection times.
Smart Maintenance
The set of maintenance concepts, activities and technologies is referred to as Maintenance 4.0 or Smart Maintenance (SMx). In our research, we gain knowledge about predictive maintenance and the underlying SMx technologies.
Some projects
Support for the Development Centre for Composite Maintenance (DCMC)
NLR provides support for the deployment of a “development box” where inspection and repair procedures and methods are developed and tested. NLR manufactures composite test panels and mounts them on the development box, which is then used to investigate how composite panels can be repaired using cobot systems. Several exploratory tests have been successfully conducted to determine whether a cobot can remove damage from thermoplastic composite panels.
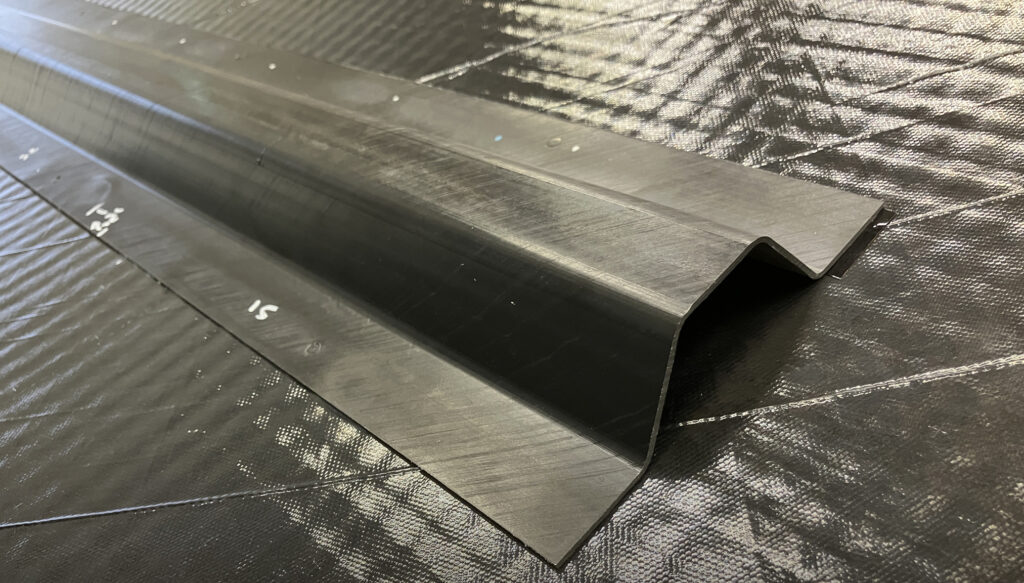
Maintenance engineering – Test Bed
Research has been conducted as part of internal research and European projects on the innovative use of cobots for inspection purposes in aircraft maintenance. This research has gained knowledge on (i) integrating cobots (collaborative robots) into a maintenance environment for performing inspection tasks, (ii) automating inspection tasks (automation technology, sensors, robots), and (iii) automatically processing image information based on AI technology. To achieve this, a laser line scanner for inspection purposes in aircraft maintenance has been applied to a cobot setup, including Pick & Place functionality.
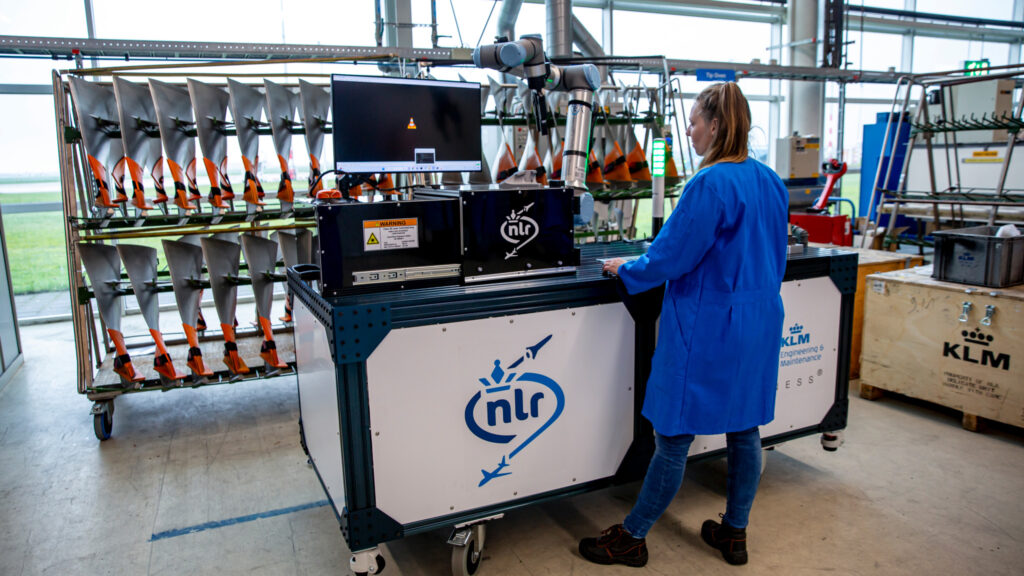
Smart maintenance technologies and concepts
Extensive research has been conducted in various areas, including the use of Augmented Reality and Artificial Intelligence in inspection and maintenance, the applicability of Fibre Optic Sensors, Laser Ultrasonics Inspection, and Non-Destructive Inspection (NDI) in general. NDI plays an important role in ensuring the airworthiness of aircraft structures throughout their entire lifespan, from production to end-of-life. To demonstrate the reliability of NDI methods, the Probability of Detection (PoD) must be established. This requires generating large amounts of experimental data under various conditions to achieve statistically valid results. This process is costly and makes it difficult to introduce new and improved inspection techniques. A potential solution to reduce the number of required experiments is the use of data from numerical simulations, known as Model-Assisted PoD (MAPoD).
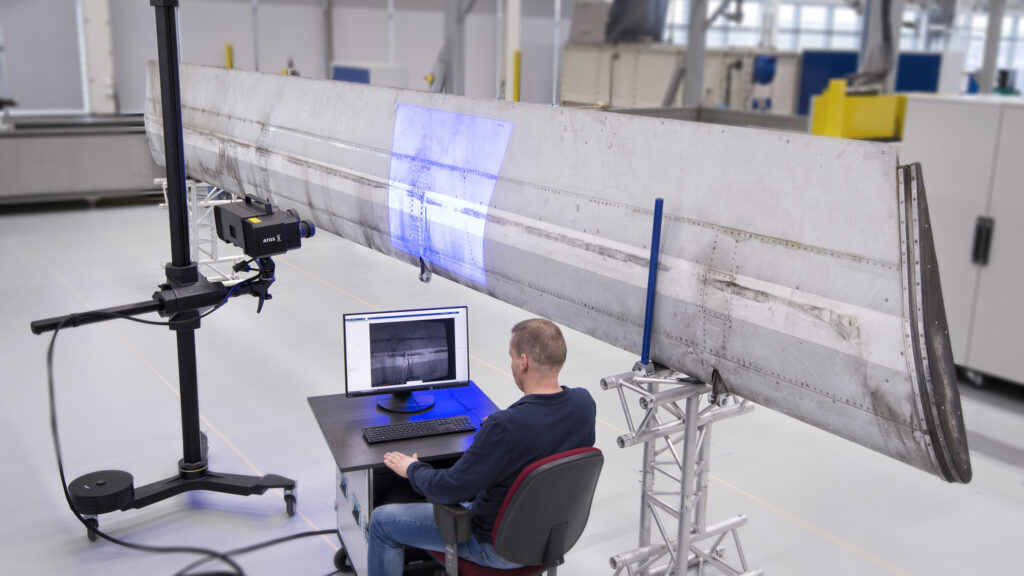