Mastering electromagnetic emissions effects
For any system to operate in aircraft or spacecraft, there must be a level of certainty that all systems are compatible and offer a certain degree of immunity to interference from nearby electronic equipment and external sources such as lightning strikes. The cornerstone of NLR’s EMC expertise is the level of knowledge it has obtained from decades of researching and testing virtually all the various systems used in aircraft. “Here at the NLR EMC facility, we offer two main types of tests for our customers. We measure various systems to determine their electromagnetic emissions, and on the flip side, we perform susceptibility tests to understand how certain equipment and instruments can be affected by this sort of interference,” describes Guus Vos, R&D engineer and manager of NLR’s EMC test facility. But according to Vos, what really sets the NLR EMC facility apart from other EMC facilities is its capabilities to test two key areas of interest specific for the aerospace domain. “If you look at the aerospace equipment, for instance, one of the typical phenomena in the domain comes from the effects of lightning strikes. At our facility, we’re able to test and measure the indirect effects of lightning on a system under test,” Vos highlights.
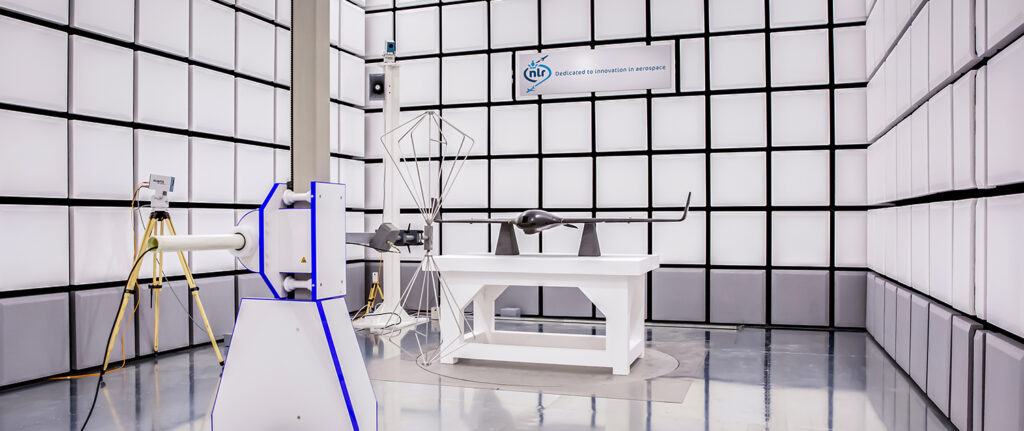
“Another distinctive capability of NLR’s EMC facility is its ability to test the effects of high intensity radiated fields (HIRF). HIRF conditions occur when an aircraft enters an area with high levels of electromagnetic disturbance, such as airfields with high-energy radar pulses bombarding approaching aircraft. HIRF testing is used to ensure that on-board systems are immune to these phenomena and that the safety critical equipment, for example the Instrument Landing System (ILS), can operate normally in these conditions.” Vos continues, “These conditions aren’t easy to recreate, which means not just any EMC test facility is equipped to perform these tests. This is a unique expertise of the NLR EMC facility.”
While these testing capabilities are certainly a strength of the EMC team at NLR, it’s not only the practical side of the domain at which it excels. Serving as a connecting link between the different domains of academia and industry, the aerospace expert team of NLR is extremely well-versed in advanced modelling and analysis and works together with several Dutch and international universities to design and build software tools used to verify the EMC performance of aircraft equipment and cabling and ultimately support designers, manufacturers and suppliers in the domain.
Crosstalk between cables in composite and plastic structures
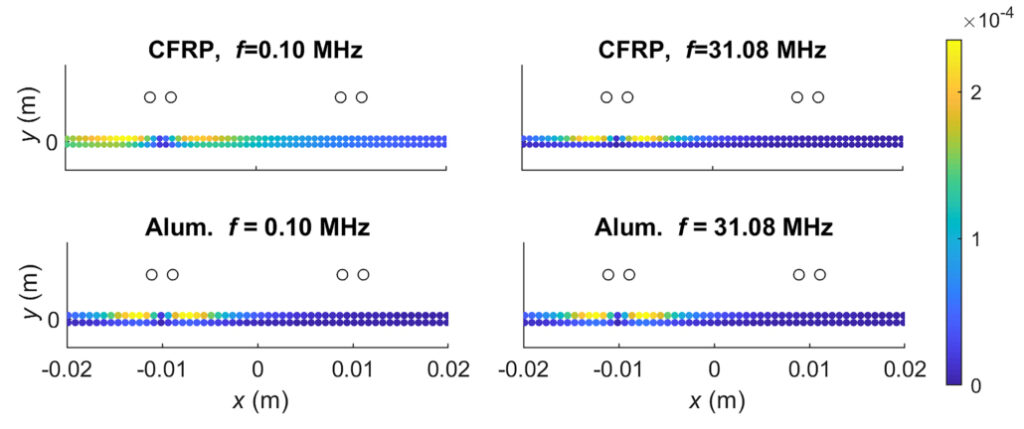
“From a theoretical perspective, NLR has a long history in advanced modelling and has contributed to a variety of different projects spanning the military, private and public domains,” explains Jesper Lansink Rotgerink, R&D Engineer at NLR. Simultaneously to working as an engineer at NLR, Lansink Rotgerink is a PhD candidate from the University of Twente, who has spent part of his time at NLR working on his PhD project focused on understanding and modelling EMC of aircraft and spacecraft, with a specific focus on crosstalk between cables.
“When you put new equipment onboard of an aircraft, you must ensure that it won’t disturb legacy equipment already deployed in an unforeseen manner,” says Lansink Rotgerink. As part of his PhD project, Lansink Rotgerink decided to delve into the EMC phenomena of crosstalk, or interference, between cables. Particularly as aircraft and spacecraft start to adopt more and more carbon-fibre reinforced plastics, which is much less conductive compared to traditional metal and aluminium structures, Lansink Rotgerink was interested in seeing what effects that had on signals and crosstalk.
“When we got started on the experimental side, we noticed some really interesting differences that we couldn’t explain, when comparing low-frequency and high-frequency signals while using the non-conductive ground plane. That’s when I started getting into modelling different ground planes to understand the theory behind the behaviour,” illustrates Lansink Rotgerink. “Using well-known models for cables and ground planes as a start, I adapted them to also capture the effects of less conducting, composite ground planes. With these tweaks in the models, we see that the simulated data is a match with the measurements we performed in the EMC facility in the experimental phase. Using this advanced modelling of the system, we now have reliable data sets and understand underlying physical behaviour. We can use this to predict how these widely used cables affect aircraft and spacecraft with composite parts.
Mission-based environmental testing for space
It’s exactly this level of both practical experience and theoretical expertise that has attracted numerous partners and companies to work with NLR. But this isn’t the only way the aerospace specialist aims to provide support to the domain. It also takes an active role in collaboration and leadership on several national and international projects aimed at moving the industry forward, specifically with an eye toward the ever-growing space market. “Recently, we participated in a project for the European Space Agency (ESA) where we collaborated with the University of Nottingham to completely design a software tool used to predict interfering behaviors, such as crosstalk, geared specifically for the space domain,” claims Lansink Rotgerink. “In the aviation sector, customers know what value we can add, particularly in validating technologies. But this platform of experience in practice and theory also meshes strongly with the space industry. Whether it’s developing our own tools, or applying those already developed, NLR offers a level of understanding that other institutions can’t quite match.” This of course, can be a little tricky in the space domain because the stringent standards of aviation and even automotive aren’t as clear cut. Qualification in space is more mission-based and depends on the objectives, meaning it’s much less standard in nature.
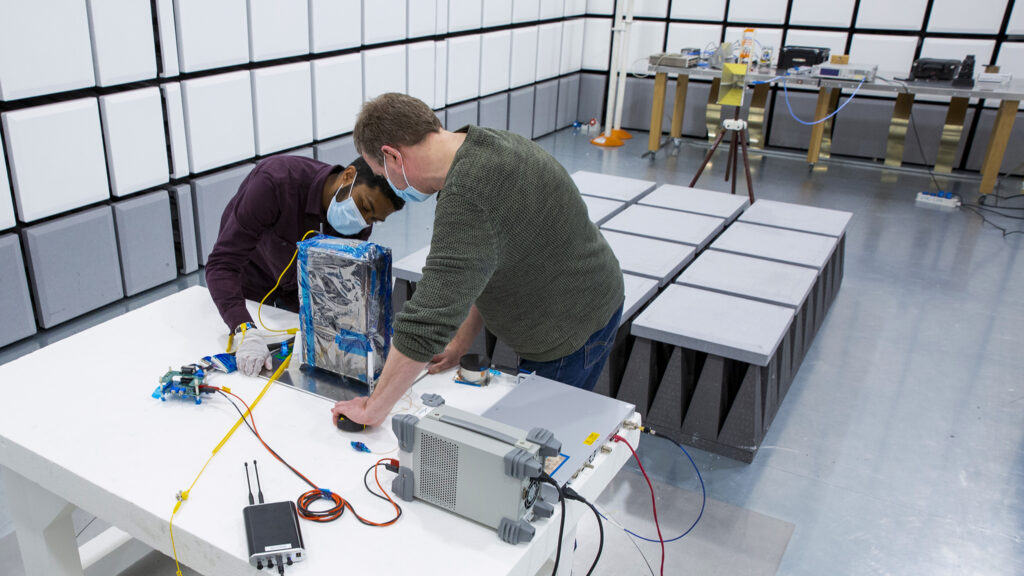
Reducing lead time and cost with early EMC compliance
Another major and most important role that NLR plays in the aerospace industry is that of an educator. As an independent and public institute, NLR is continuously researching and developing new tests, theories, tools and methods within the domain. But it’s their desire to spread information and their findings and guide the industry forwards that also sets it apart. In fact, Royal NLR makes itself available to aerospace manufacturers for courses in EMC.
“We have created fully customised courses on EMC for several of our customers. Each is crafted specifically to fit their design needs and ideas, but always constructed to share both the theory as well as the hands-on application of testing and show them how we achieve this in our facility,” explains Lansink Rotgerink. “This kind of work enables us to help customers tackle specific questions from early in the design phase. This focus on EMC compliance from so early on means they speed up prototyping and can reduce overall lead time, which leads to big savings in cost.”
“NLR has many of the brightest minds in the domain with expert knowledge and state-of-the-art facilities and testing equipment across the board,” expresses Vos. “Whether it’s for electromagnetic modelling, EMC testing or any other type of environmental testing for systems and equipment, from aviation to space, NLR has it covered.”