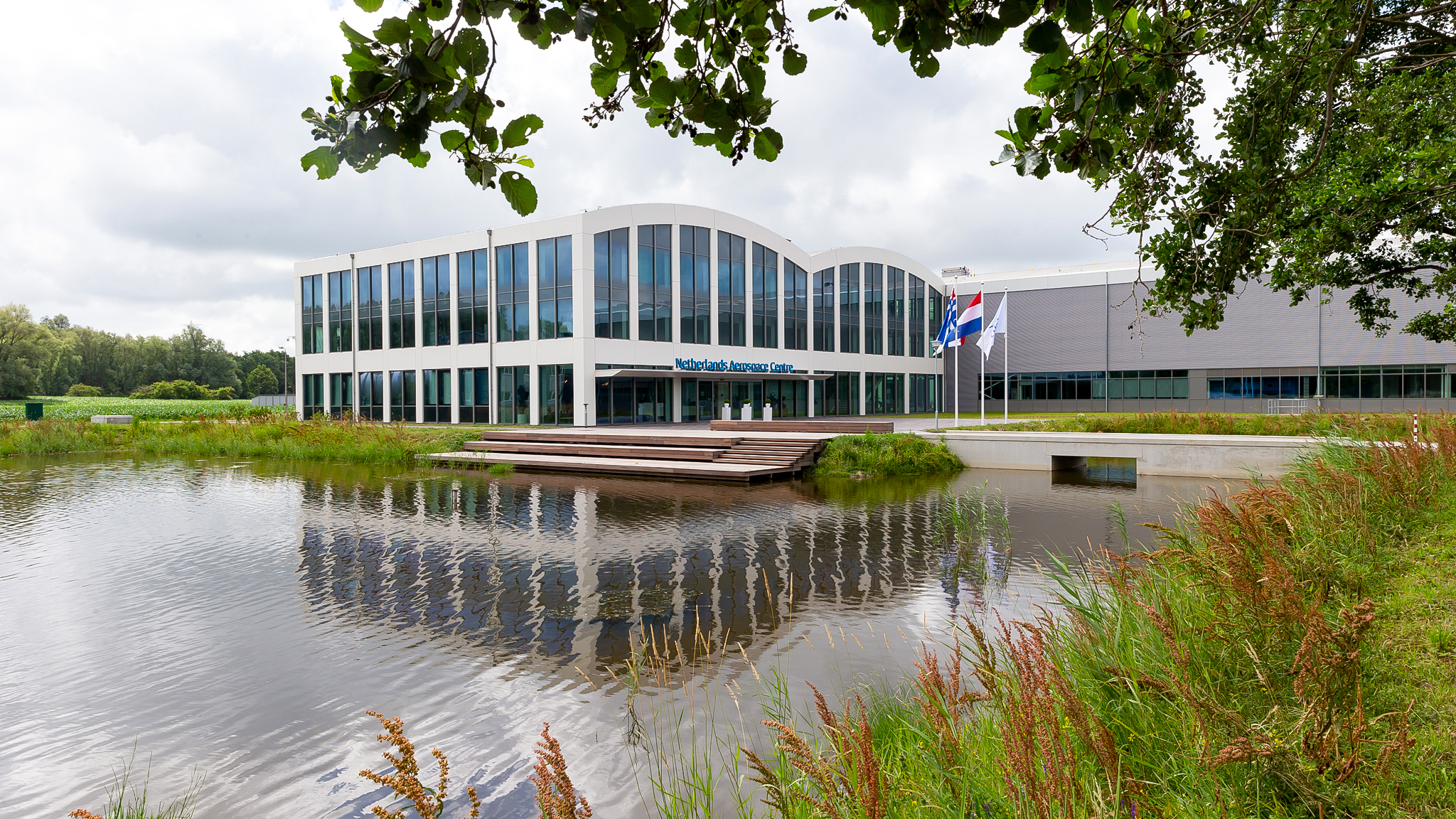
NLR corporate
17 April 2025
Royal NLR appoints new Board
As of June 1, 2025, NLR will have a new collegiate board. The top structure will be expanded to a three-headed board, consisting of a CEO, a CFO, and a CTO. With the appointment of Tineke van der Veen, Jan Lintsen, and Martin Nagelsmit, the organisation will lay a robust foundation to strengthen and further […]
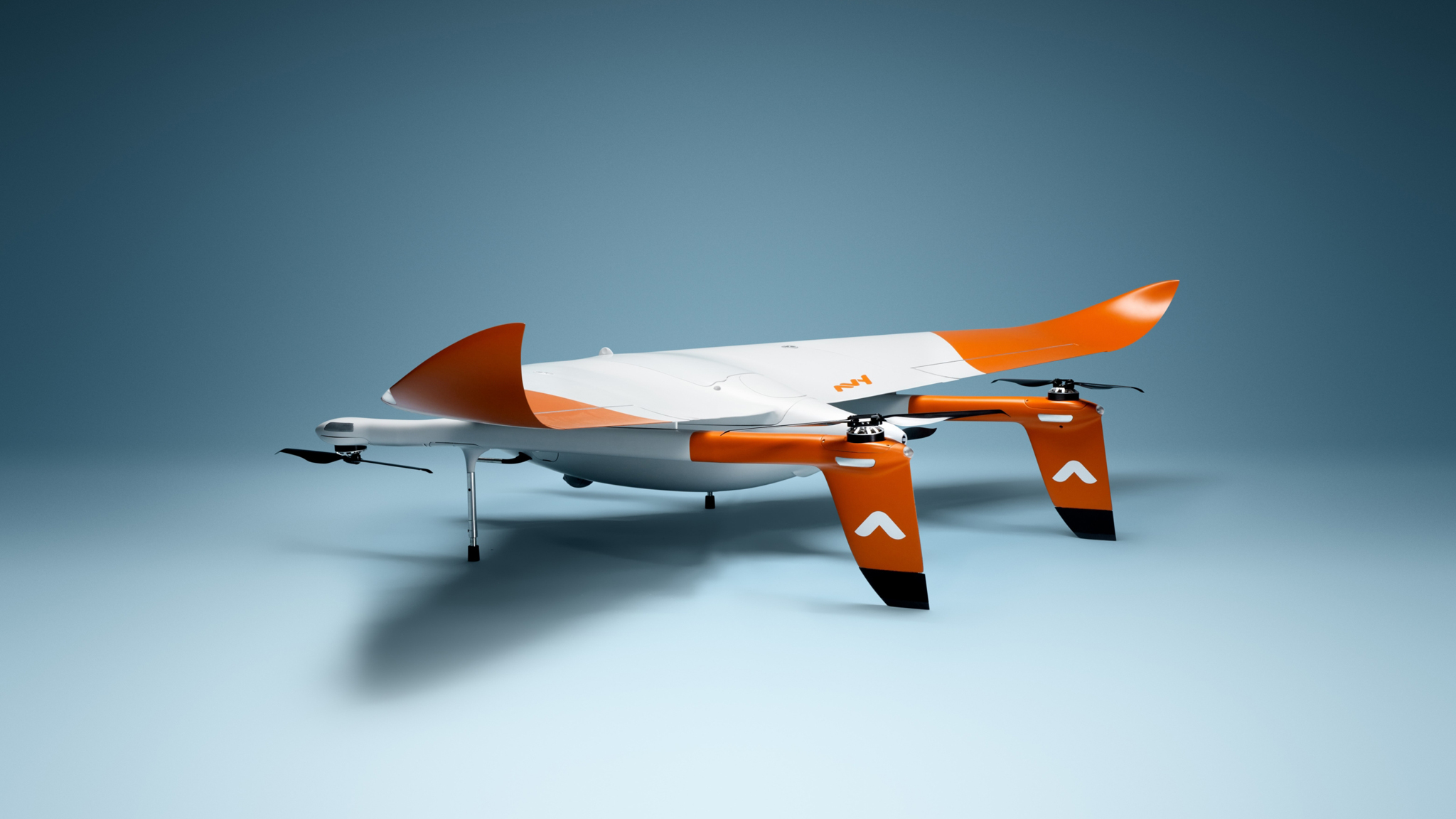
Platform System Design
22 January 2025
Avy and NLR partner to drive drone innovation
NLR has partnered with Avy, a Dutch company that develops autonomous fixed-wing drones tailored for humanitarian, health, and environmental missions, with a focus on creating a sustainable impact. NLR has acquired an Avy drone for testing and evaluation, aiming to drive innovation in aerospace applications. This collaboration supports the development of sustainable and cutting-edge drone […]
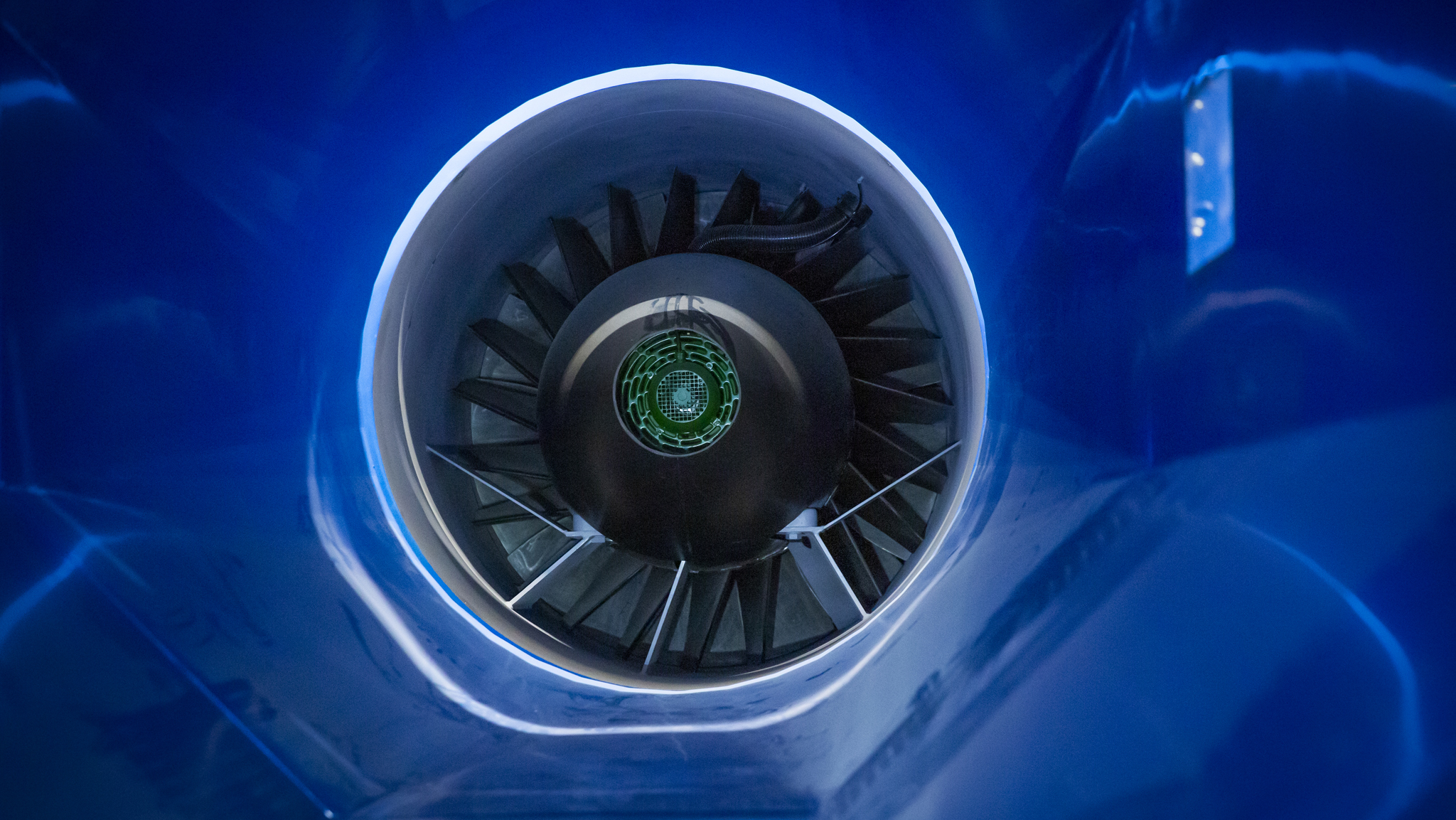
AGENDA
Let’s meet!
13-15 May
Airspace World
16-22 Jun
Paris Airshow
5 Oct
ESA/ESTEC Open day
6-7 Oct
SAMPE Europe
8-9 Oct
Electric & Hybrid
14-16 Oct
MRO Europe
18-20 Nov
Space Tech Europe
Areas of expertise
Programmes
Markets
NLR Repository
Newsroom
Stay up to date with the latest developments. In the Newsroom you can find the latest news, articles, and blogs from NLR. We also showcase a range of videos and publications here. For more video content, please visit our YouTube channel, NLRmedia.
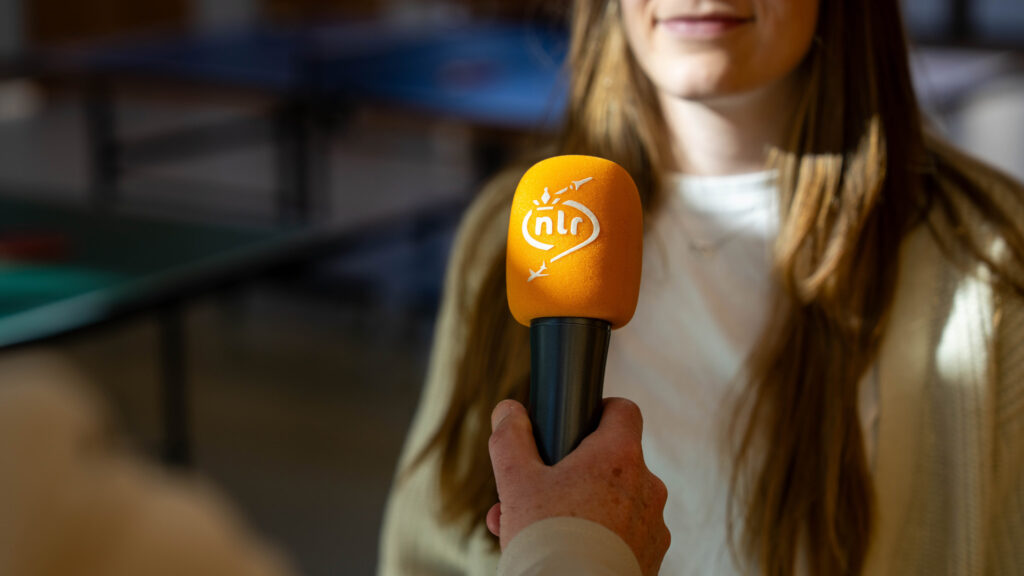