The Clean Sky 2 Multifunctional Fuselage Demonstrator (MFFD) with its 8.5 meter long composite-made fuselage section with an approx. 4 meter diameter gives a glimpse of what a next-generation aircraft could be. This typical section of a single aisle aircraft fuselage is completely produced from thermoplastic. Now, Royal NLR’s STUNNING project is turning heads as the MFFD’s largest component, the 8.5 meter long lower fuselage skin, has been manufactured and delivered to the project partners.
The challenge
As part of the EU’s Clean Sky 2 initiative, the aerospace industry is looking for flight path to sustainability. To deliver a double-digit fuel burn reduction for the Large Passenger Aircraft (LPA) segment next generation fuselage structure concepts are needed in which cabin, cargo and physical system elements are integrated. Its three main and for STUNNING overarching objectives for future Single Aisle Aircraft fuselages compared to the state of the art are:
- Reduce weight
- Reduce recurring cost
- Enable a High Rate Production (HRP) of 60-100 shipsets per months.
The solution
As part of the MFFD development, the STUNNING project developed, manufactured and delivered the 180° full scale lower half of the multi-functional integrated thermoplastic fuselage, including cabin and cargo floor structure and relevant main interior and system elements. The STUNNING team applied advanced design principles, innovative system architecture and advanced materials and processes.
What did we do?
NLR developed and applied a competitive manufacturing process using fast AFP layup of two 90° fuselage segments out of thermoplastic TC1225 PAEK/T700 uni-directional carbon fibre material on a layup tool at room temperature. The part was consolidated by the NLR team in an innovative consolidation mould (EMOTION CfP) using the research autoclave at the German Aerospace Centre (DLR) in Stade, Germany. The consolidated 180° fuselage skin was inspected at NLR using Thermography and delivered to the
STUNNING partners for the integration of structures, interior and systems installation. A significant weight reduction resulting from this integrated approach, based on advanced thermoplastic assembly principles like welding, will contribute to the environmental goals. Manufacturing costs and assembly times will be reduced and high production rates can be realized. To achieve the overall goals, ‘beyond state of the art’ technologies are developed and verified in dedicated tests up to TRL5.
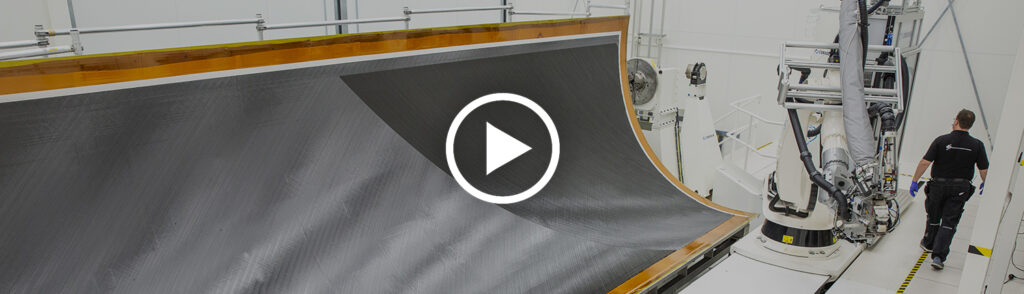
Project partners:
Industry : Fokker Aerostructures, DIEHL
Research organisations: Royal NLR
Universities: TU Delft, SAM|XL
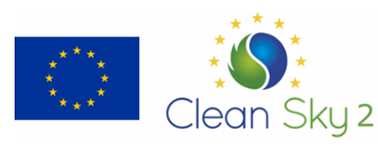
This project has received funding from the Clean Sky 2 Joint Undertaking (JU) under the European Union’s Horizon 2020 research and innovation programme.