To reduce the impact of aviation on the climate, the aviation industry needs to develop solutions that drastically reduce emissions of greenhouse gases. Hybrid electric flight is one of the cornerstones of our progress towards sustainable aviation. However, the significantly increased electric power levels associated with having electric propulsion on board yield both thermal and electromagnetic challenges.
The challenge
Increased currents and voltages caused by the higher electrical power levels on board hybrid electric aircraft introduce two main challenges:
- The thermal challenge: increased heat dissipation in power electronics and power feeders needs to be managed.
- The electromagnetic compatibility (EMC) challenge: increased currents may bring the risk of interference with other on-board equipment, e.g. through conducted and radiated emission. Mitigation measures need to be taken throughout the power train.
The solution
EASIER has developed EMC solutions for power EWIS, power electronics and filtering to mitigate the electromagnetic emission issues. Two-phase cooling systems have been developed to handle the increased heat dissipation. Thermal modelling and validation of power feeder designs has led to less voluminous and lighter power feeders for hybrid electric aircraft. Finally, system trade-offs have been made to optimise the performance and weight of the integrated solutions.
What did we do?
NLR has developed simulation models to assess the performance of the EASIER power feeder and power electronics solutions, which demonstrate that radio frequency (RF) emissions are reduced. The power feeder solutions have also been validated by a dedicated ground-based demonstrator with the power train of Evektor’s EPOS+ (a fully electric two-seater) at NLR’s EMC
>
facility. Moreover, NLR’s thermal team has designed and tested two-phase cooling solutions for power electronics, resulting in a 68% volume reduction compared to single-phase cooling. Finally, simulation models for the thermal optimisation of power feeders have been developed and validated, helping to optimise the weight of the EASIER power feeder solutions.
Project partners:
Project partners: GKN Fokker Elmo, Collins Aerospace Ireland, Evektor, EMAG, Raytheon, ARTTIC, University of Twente
For more information about the EASIER project, visit the project website here.
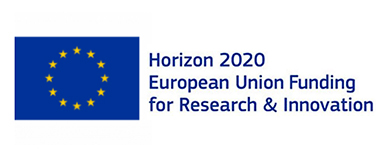
This project has received funding from the European Union’s Horizon 2020 research and innovation programme under grant agreement no.875504