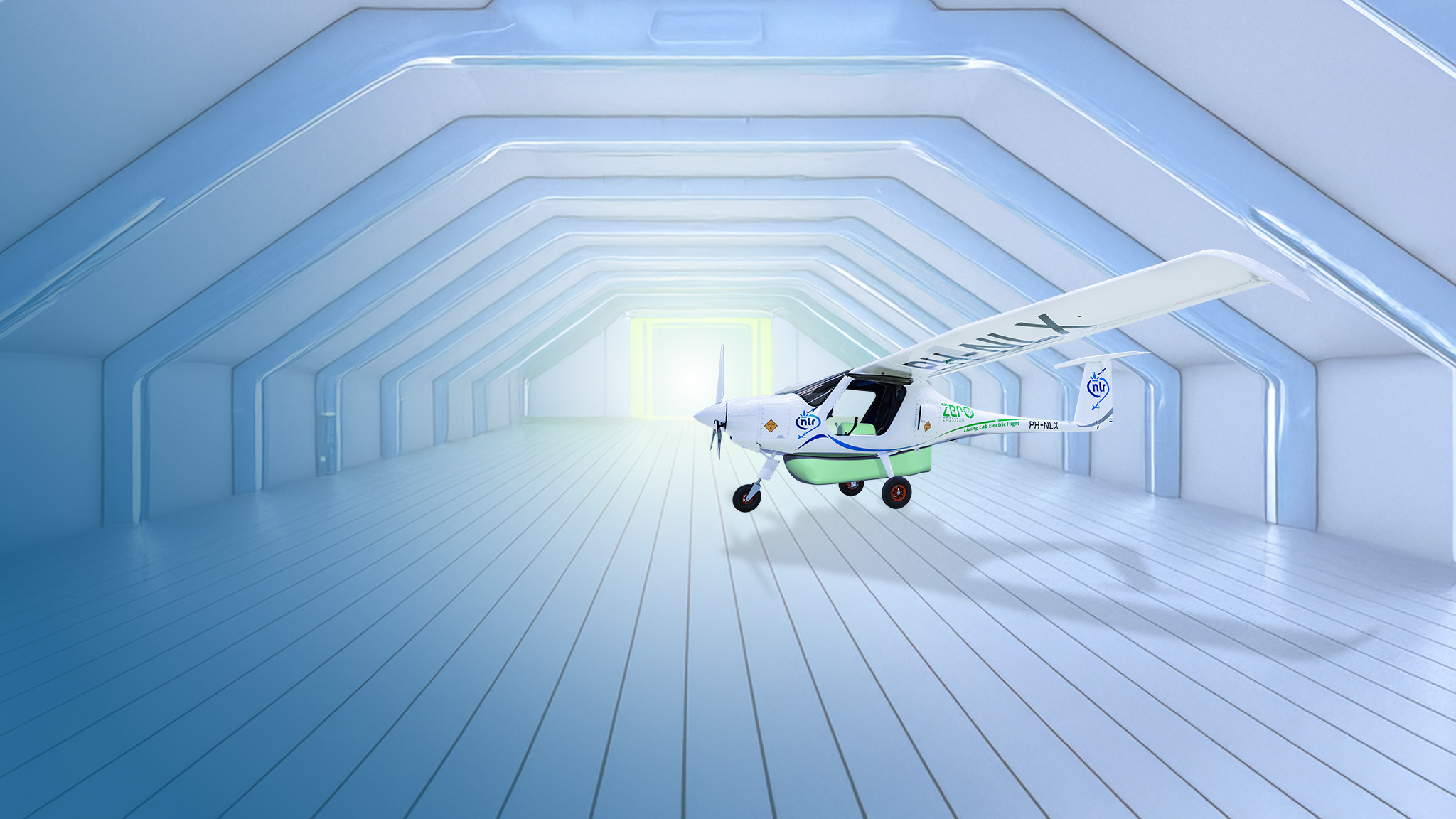
Newsroom
Filter
Stay up to date with the latest developments
Welcome to our Newsroom. Here you can find the latest news, articles, and blogs from NLR. We also showcase a range of videos and publications here. For more video content, please visit our YouTube channel, NLRmedia. The NLR Repository provides access to our public library of NLR reports.
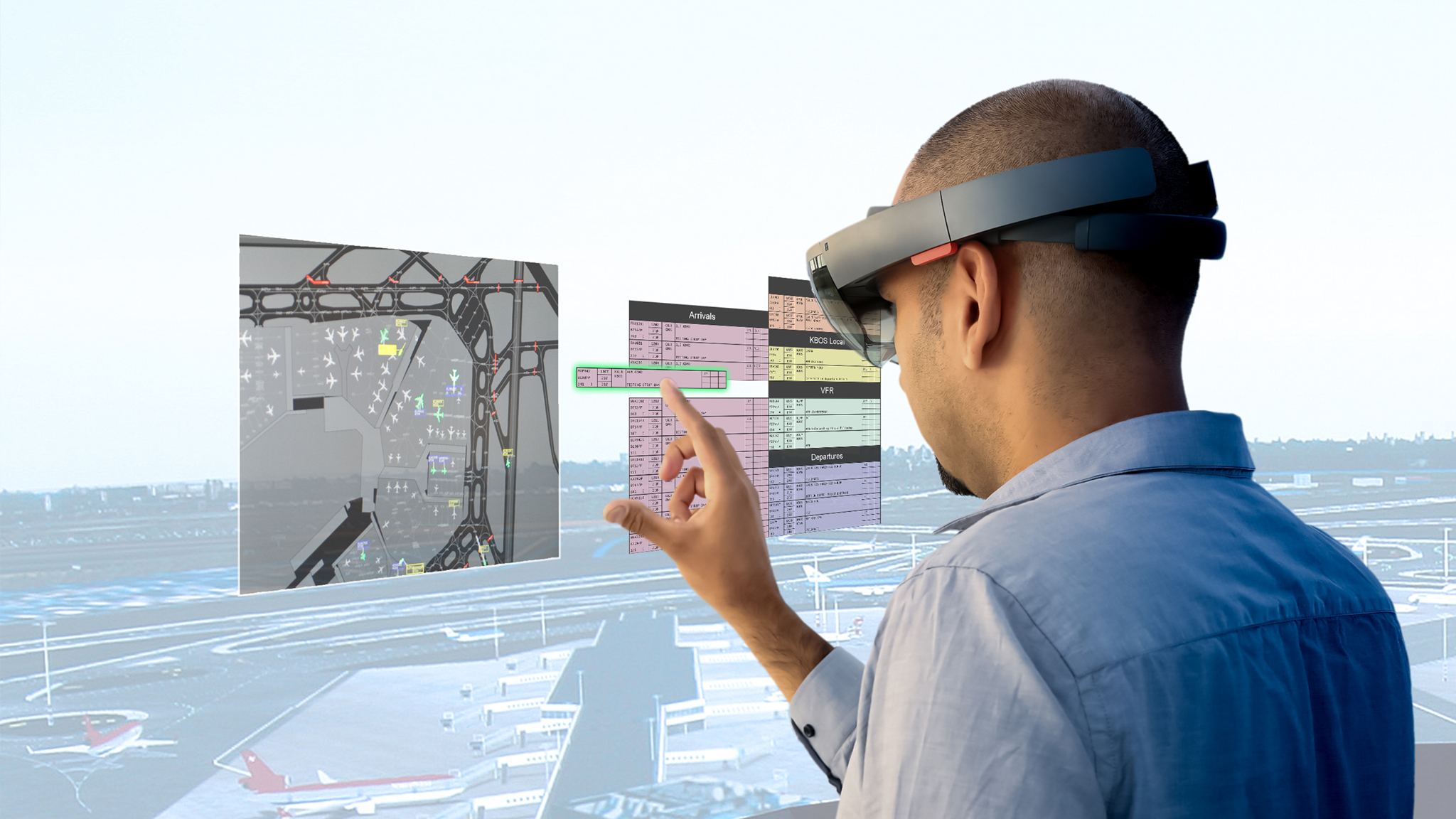
Air Traffic Management
17 April 2025
Booklet: Reseach and development solutions for Air Traffic Management
Let’s realise competitive and sustainable aviation The challenge for civil aviation operators is to achieve competitive and sustainable aviation. The growing demand to increase efficiency, sustainability, safety and security, enhance resilience and reduce costs requires innovative solutions. That is why Royal NLR focuses its innovative R&D and solutions within the Air Traffic Management domain on […]
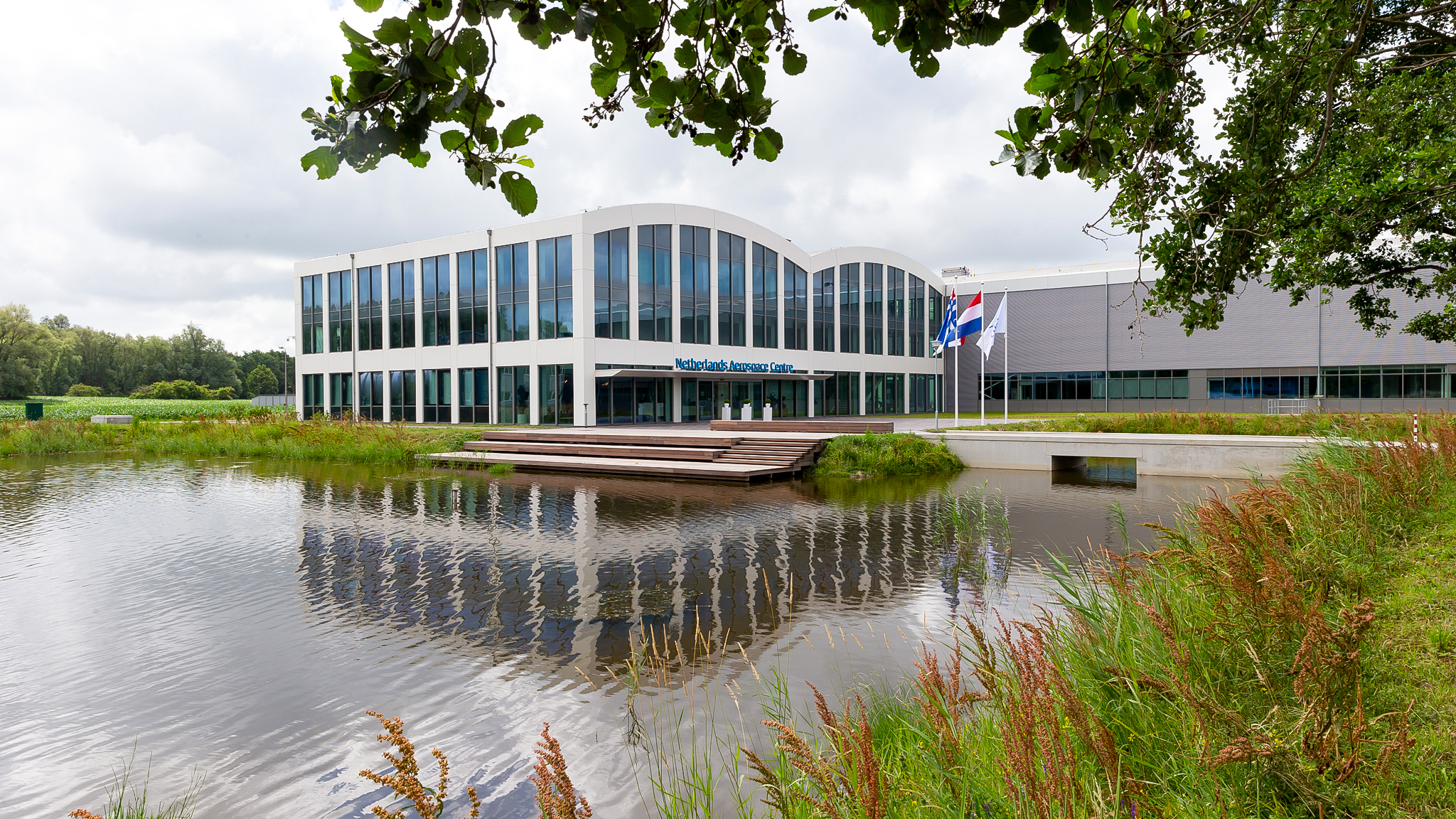
NLR corporate
17 April 2025
Royal NLR appoints new Board
As of June 1, 2025, NLR will have a new collegiate board. The top structure will be expanded to a three-headed board, consisting of a CEO, a CFO, and a CTO. With the appointment of Tineke van der Veen, Jan Lintsen, and Martin Nagelsmit, the organisation will lay a robust foundation to strengthen and further […]
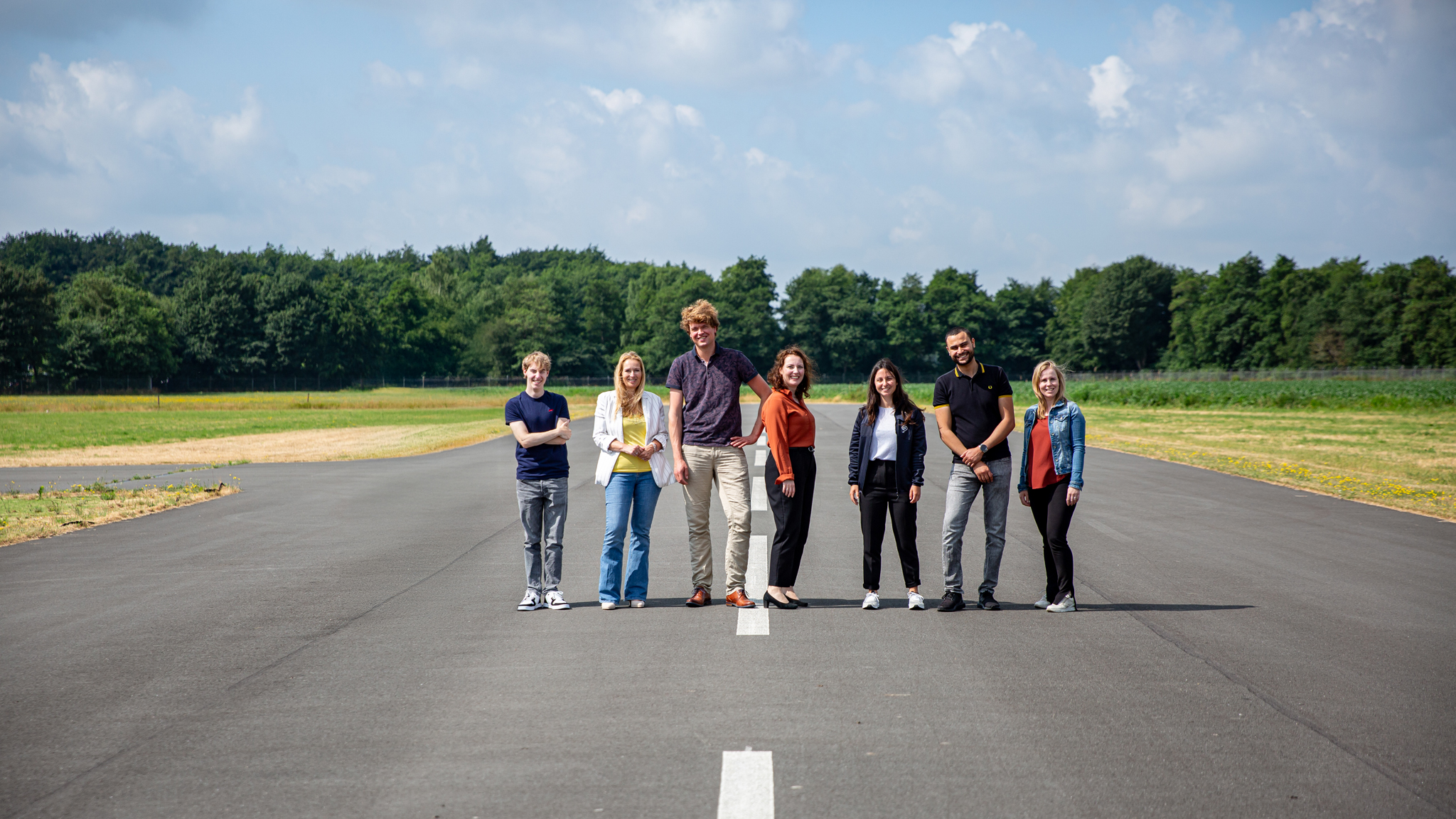
NLR corporate
09 April 2025
Welcome to our new website
Our new website is live! We’re proud of the result and invite you to take a look around. Welcome to our new website Discover our research and developments presented in a modern and contemporary way. Our experts work on innovative projects every day to make air and space travel safer, more sustainable, and efficient. We’re […]
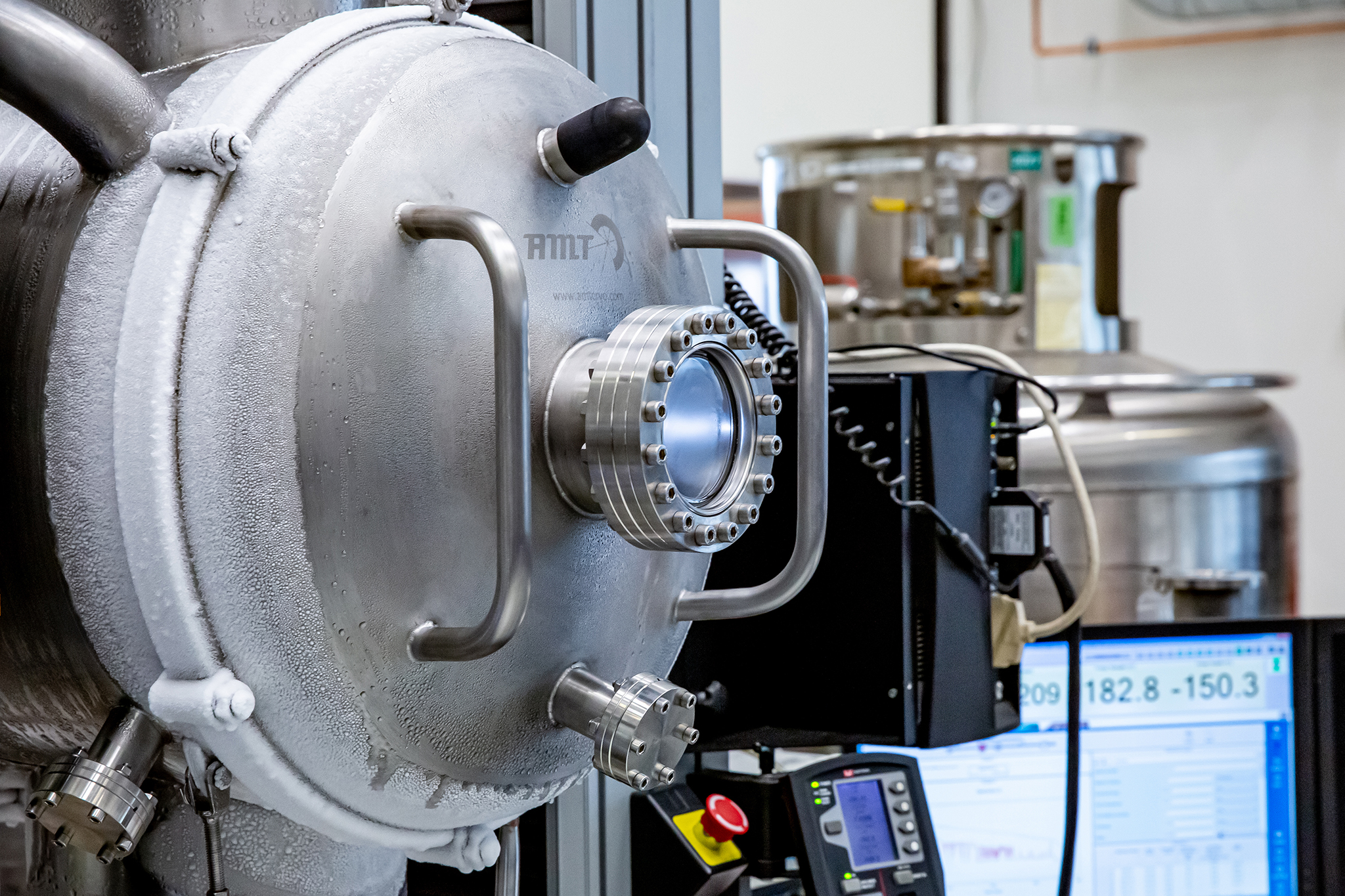
Construction and Manufacturing
24 March 2025
Brochure: Testing and Evaluation – Structures
NLR acts as a one-stop-shop for “Non-Standard” testing of aircraft parts, structures and materials. The traditional structural testing has evolved, it includes energy transition related testing: deep cryogenic, hydrogen, fuel cells, and hydrogen electric power trains (in full or its components). We have the capability to offer you inspection, testing, characterisation and failure analysis. For […]
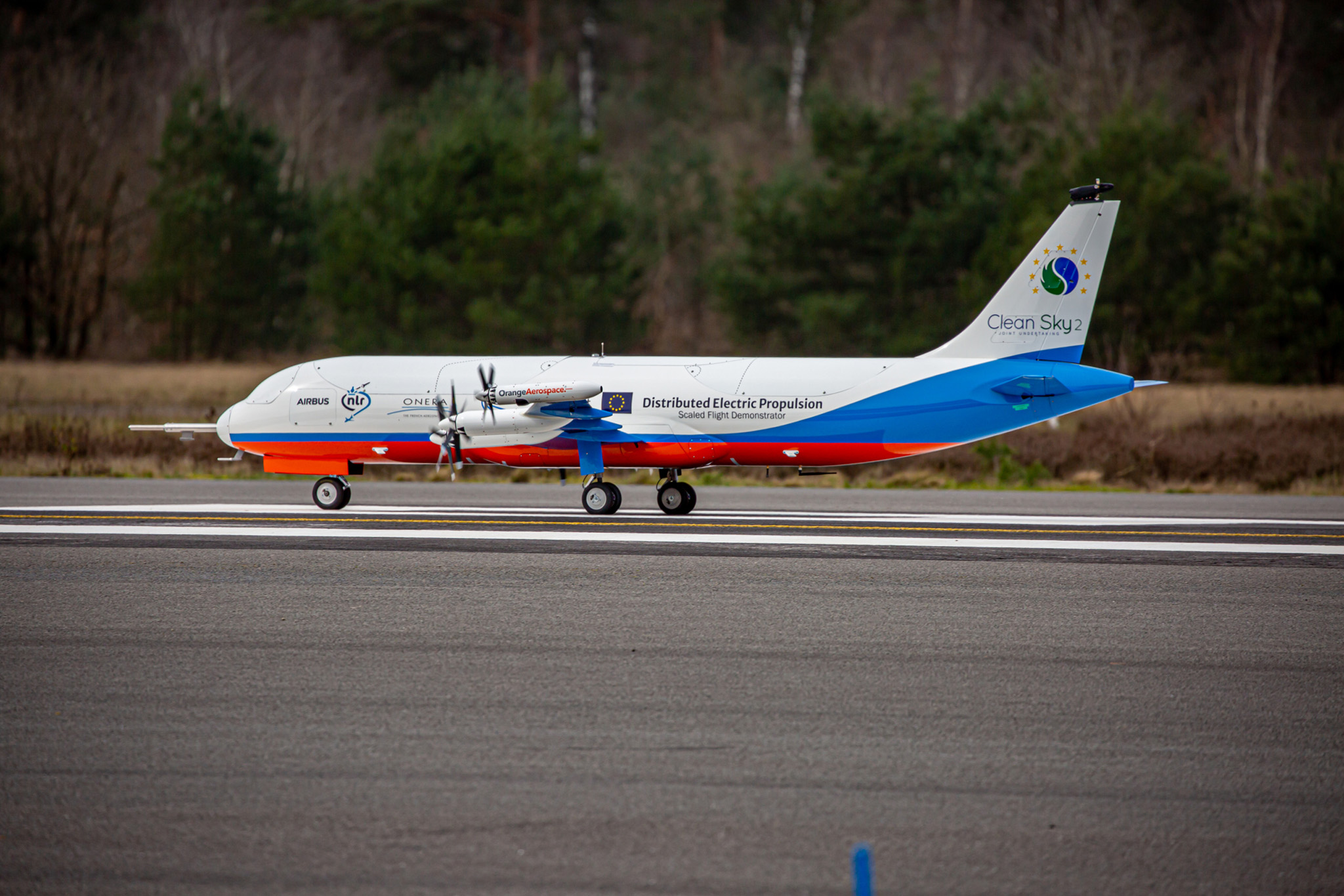
Sustainability and Environment
20 March 2025
Booklet: Applied research for aerospace industry, space and defence
Royal NLR operates as a non-profit, objective and independent research centre, working with its partners towards a better world tomorrow. As part of that, NLR offers innovative solutions and technical expertise, with the aim of making aerospace more sustainable, safer, more efficient and effective. We are the connection between scientific research, policy-based support and industrial […]
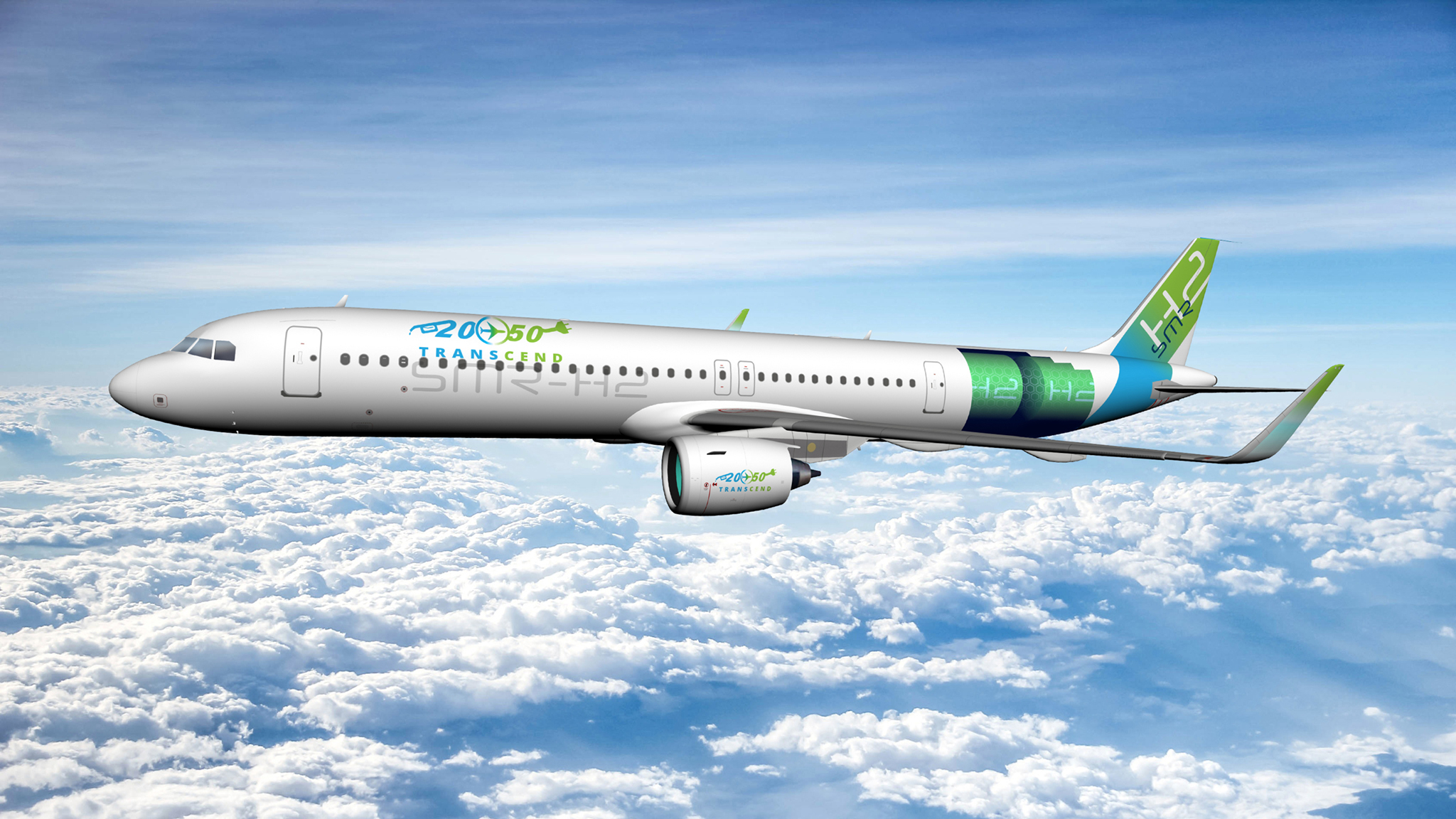
Sustainability and Environment
20 March 2025
Booklet: Research and Development more electric and hydrogen powered aerospace
Hydrogen as a fuel is considered to be an important route towards future sustainable aviation. For aviationapplications, hydrogen presents several key advantages: it allows for the elimination of carbon emissions inflight and along the entire life cycle. Its usage in fuel cells allows eliminating NOx and particles. When burntin a turbine engine, very low particle […]
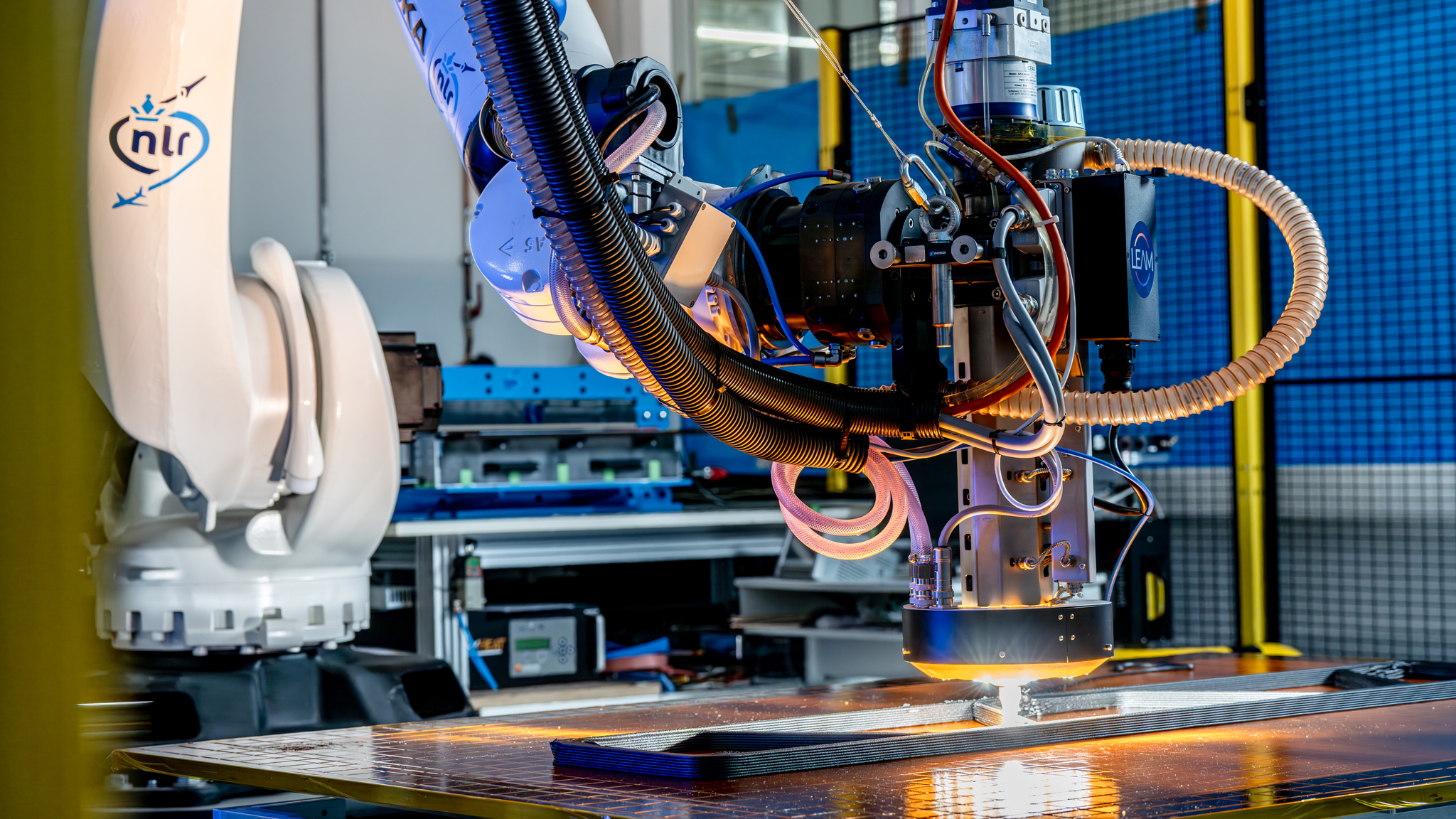
Construction and Manufacturing
20 March 2025
R&D case: Enabling temperature control for large scale additive manufacturing
The challenge One of the main challenges of Large Scale 3D printing of high temperature thermoplastics is the control of the interface temperature – which determines the degree of bonding between consecutive layers. When the deposited material has cooled down in excess, poor adhesion is achieved between layers, leading to insufficient strength, delamination, cracking and […]
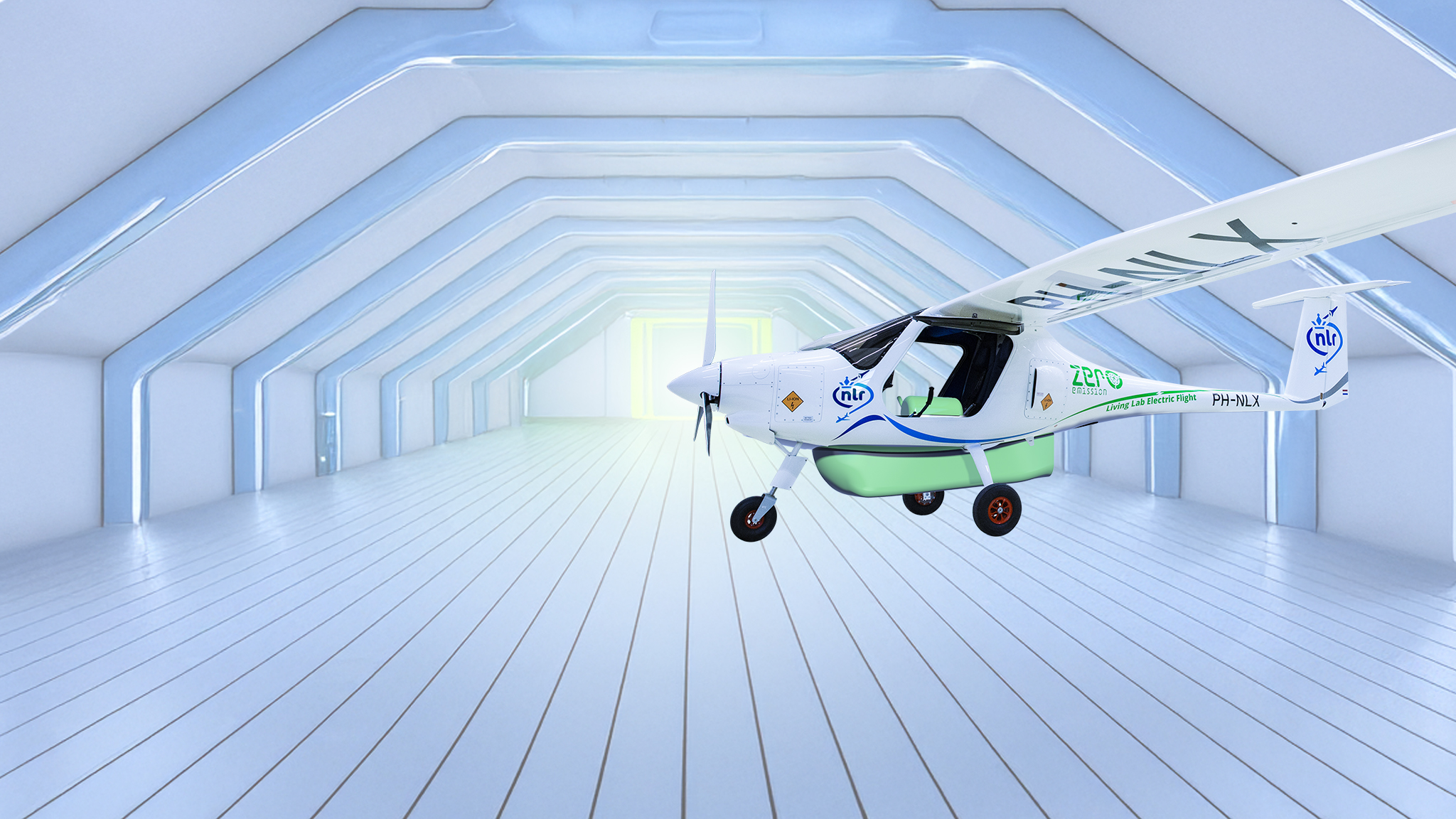
Sustainability and Environment
14 March 2025
NLR and Cryoworld collaborate on flying with liquid hydrogen
NLR is taking a further step towards more sustainable flight by partnering with Cryoworld to develop a liquid hydrogen tank. This follows the agreement with zepp.solutions for a fuel cell system. The new collaboration contributes to NLR’s ambition to conduct a demonstration flight on liquid hydrogen in 2026. NLR aims to achieve manned flight on […]
Sign up for the NLR newsletter to receive our latest news, recent developments, new insights, reports and whitepapers, as well as our calendar of upcoming trade fairs and events.