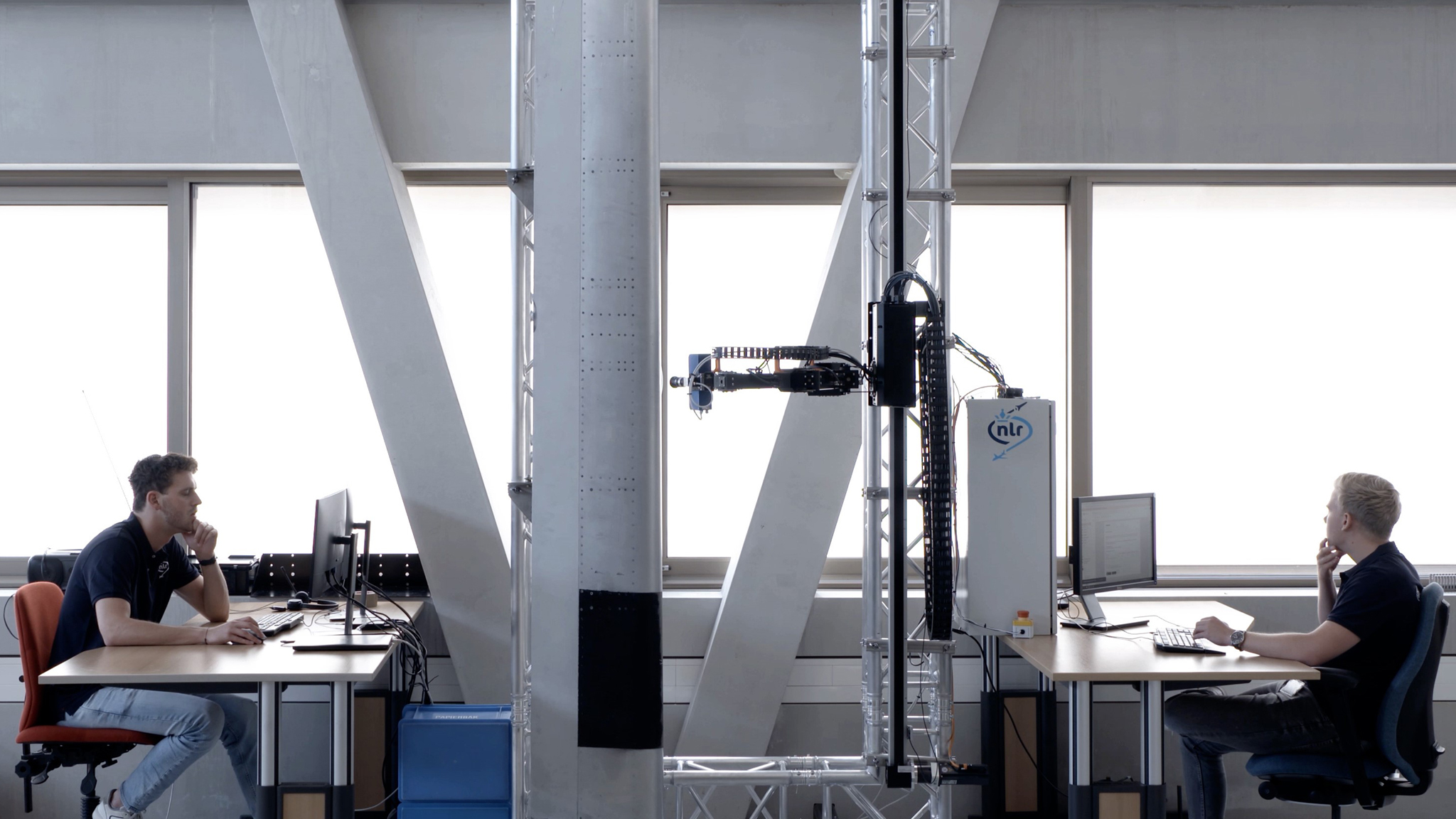
Autonomous Robot for Visual Inspections
Aircraft inspections require time and highly professional technicians. This makes aircraft maintenance time-consuming and expensive. NLR investigates the possibilities to make aircraft visual inspections faster and more affordable by automating and robotising these visual inspections.
The challenge
Aircraft inspections are critical for the continued operations of aircraft. However, the downtime and costs are a burden for operators. Current developments in automation, robotics, photonics, sensor technology and image processing are rapidly advancing. NLR investigates if these technologies can be applied to visually inspect aircraft. The biggest advantage is productivity. Inspections can be time-consuming and require skilled and experienced technicians. Robots can minimize the routine work so that the expert technicians can focus on the demanding inspections. This may be particularly relevant with an aging population of technicians. Another advantage is, that it makes the work more pleasant for technicians, robots can take over dull, dangerous and dirty work. They don’t mind the working conditions.
The solution
Royal NLR developed a system to investigate the possibilities visually inspect aircraft and components. The building blocks include:
- One or more sensors to scan the object. The choice for the sensors depends on the type of defect you want to find
- A robot to maneuver the sensors to the right locations around the object
- Algorithms to detect, classify and measure defects
- Automation technology to autonomously perform the prescribed inspections
The leading edge scanner is one of our test rigs. The initial intend was to inspect metallic leading edges for dents, scratches, gouges, missing rivets, and so on. However, one of our other robots scans composite structures. With the use of additional sensors we also inspect these composite structures for delamination, skin-to-core unbonds, and so on.
One of the challenges is the automation of an inspection robot. Not only does it require a robot arm (or a cartesian or delta robot), but it also requires different sensors to detect, classify and measure different defect types. And if we inspect larger objects, the images may require alignment and stitching too. In the background, machine vision technology and image processing algorithms are hard at work to process the images and draw meaningful conclusions. And it is not sufficient if you can perform one of the tasks, for an automated inspection, all these steps are necessary. Our leading edge scanner is our test bed to integrate all these different steps of the process to enable robots to autonomously inspect complex objects and parts such as aircraft.
What did we do
Royal NLR started approximately 4 years ago with the development of maintenance technology. We focused on the automation of visual inspections. We reckoned that we needed sensors, robots and an imaging pipeline to inspect aircraft and components for damages. When we started, we quickly realized that there are many different defect types that technicians may encounter when performing inspections. So, over the years, we tested many sensor technologies to find out how these technologies can help us identify and locate defects. We are often asked how long it will take to bring the visual inspection technology to the market. Well, if we assume that we want to inspect a specific component for a specific defect with a specific sensor, than it seems manageable in the short term. However, if you seek a universal robot that can inspect every part of an aircraft for any type of damage, we are talking about a longer period of time.