Sustainable aviation is a hot topic nowadays and it is being addressed with the main focus on reducing structural weight, thereby lessening fuel consumption and emissions. This can be achieved by replacing metallic parts with equivalents made from composite materials that provide high ratios of strength and stiffness to weight. Such modifications allow the total weight to be significantly reduced without compromising on performance.
Composite materials are already widely used in the industry, but more efficient ways of manufacturing are still needed. Consequently, in the context of the Mobility Fund, NLR is exploring the large-scale additive manufacturing of fibre-reinforced thermoplastic materials. This is a relatively new technology that brings all the advantages of 3D printing (such as freedom of design, short lead times and cost-effectiveness) to a large scale, up to 2×2 metres in the case of NLR’s current setup. Another important benefit is the minimal material waste incurred during manufacturing, which makes the process sustainable right from the beginning of the production line.
The programme
The governmental Mobility Fund programme is aimed at reinvigorating the efforts of Dutch industry to progress towards more sustainable aviation. Several projects are being carried out within the Mobility Fund programme. One of them focuses on developing thermoplastic fibre-reinforced concepts for the Urban Air Mobility (UAM) and Sub-Regional Electrical Vehicle (SREV) markets, which require the high quality levels of the aviation sector to be met while achieving the production speeds of the automotive industry.
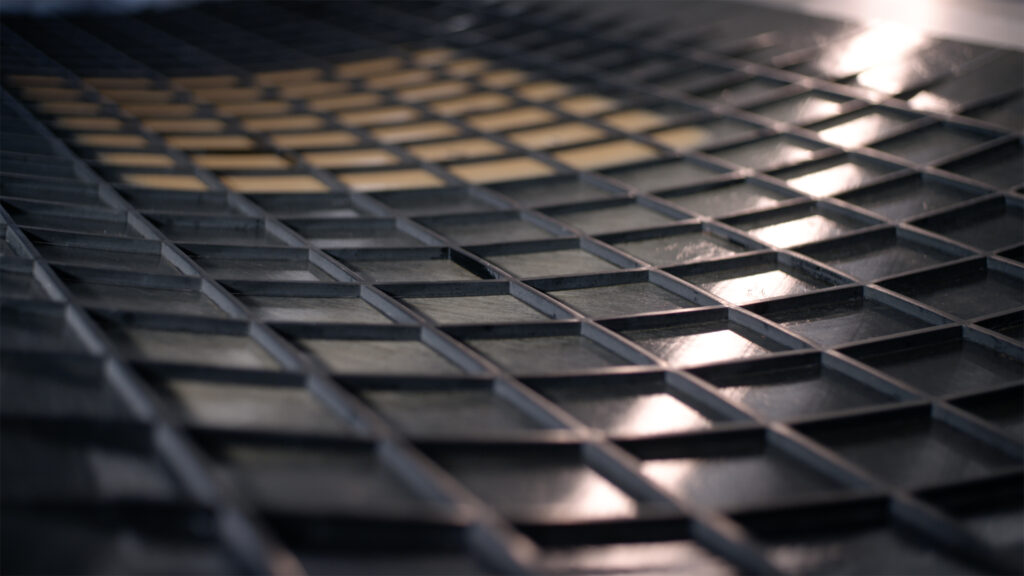
The thermoplastic project has been split into several groups of related tasks (known as work packages). NLR is involved in several and is conducting independent research and development into inter alia robot-assisted induction welding for thermoplastics, digitalisation of the welding process and the use of thermoplastics in stiffening structures. With a specific focus on the last subject, the Large-Scale Additive Manufacturing (LSAM) process is being evaluated as a possible solution for rapid manufacturing of stiffening grids or honeycomb structures for UAM and helicopter doors and hatches. Printing these structures on top of pre-consolidated multi-curved panels would be the ultimate goal.
The technology
Large-Scale Additive Manufacturing (also known as Big Area Additive Manufacturing or Fused Granulate Fabrication) is a manufacturing process based on depositing material in a certain area one layer at a time. The setup consists of an extruder (which melts and ejects the material) attached to a robot (which displaces the extruder as a function of the geometry to be printed) and the print bed (where the material is deposited).
The materials
R&D engineer Ana Ramirez de las Heras, who works for the Structures Technology department of the Aerospace Vehicles Division of NLR, is in charge of this relatively new manufacturing process. According to her, not every material is suitable for inclusion in a ‘flying part’ as it needs to meet aerospace quality and safety requirements and must be certified as such.
“The current focus is on carbon fibre-reinforced high-performance thermoplastics such as PEEK, low-melt PAEK or PPS, which can be used in very demanding applications,” states Ramirez de las Heras. “However, it’s precisely the special behaviour of these materials that makes them more challenging to process with this technology.”

“One of the main challenges of LSAM is finding the optimum layer time, the time required to print one complete layer. If the selected layer time is too short, the previous layer won’t have had time to cool down enough and it will make the following layer collapse. On the other hand, if the layer time is too long, the material will solidify and the bonding with the next layer will be weak, leading to poor mechanical properties in the final product. The layer time selected will be material-dependent.”
Special attention is being paid to temperature control of the previous layer and implementing technologies such as infrared or laser heating. This will potentially increase the possibilities of the technology.
The setup
Since the beginning of 2023, NLR’s Structures Technology department has been working on implementing its own LSAM setup, consisting of the latest extruder from CEAD, a Dutch technology supplier of 3D printing equipment. The model S25 is a lightweight extruder (under 30 kilograms) with a maximum output of 24 kilograms an hour, engineered for high-end applications. The S25 is designed to be mounted on a robot arm such as the KUKA KR240 used at NLR. This is a high-payload robot with an extensive range of movement (6-axis), allowing large scale printing.
The extruder uses four different heating zones to melt the thermoplastic material gradually without degrading it, and can reach temperatures up to 400°C. The system is suitable for processing high performance thermoplastic materials (like the ones previously mentioned) with minimal wear of the machine, even when short glass and carbon fibres are included. The nozzle offers flexibility in the achievable wall thickness, which adds value when the process is to be used for different applications.
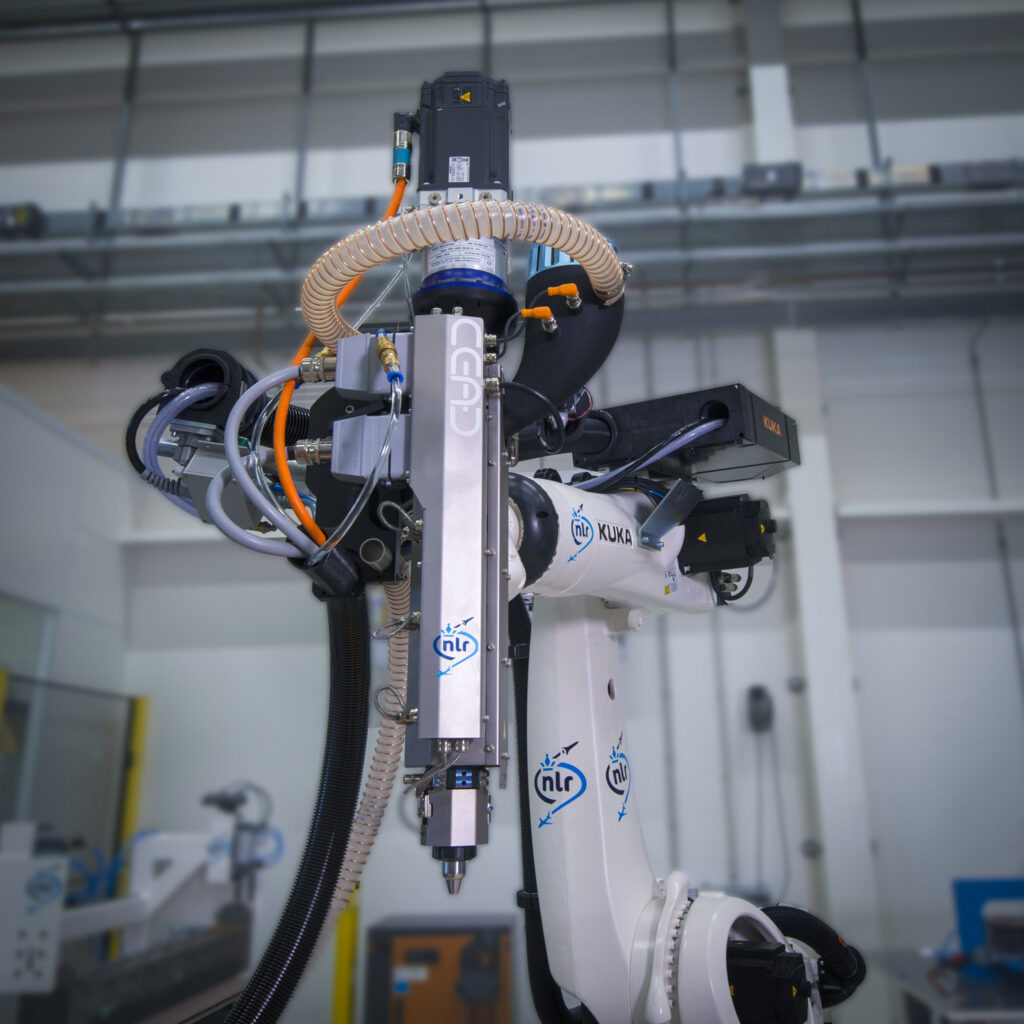
The setup also includes the VISMEC Dryplus drying system, upgraded with an automatic hopper loader for print jobs of more than 8 hours. Correct drying of the material before printing is essential if good part quality is to be achieved, due to the high moisture content that some materials tend to absorb.
In the coming months, the setup will also include a heated bed, which will improve the quality and the material adhesion to the print surface by maintaining the heat in the first layers of the product.
Future applications
“Even though the focus is currently on printing stiffening structures such as honeycombs or grids, this technology has proved to be suitable for other applications such as tooling,” says Ramirez de las Heras.
“LSAM moulds are certainly a faster and cheaper solution than current moulds made from metals or using composites. Nevertheless, depending on the final application of the mould, it is still a challenge to control the porosity levels and to predict its dimensional stability accurately.”
The NLR department will continue to study this topic and develop further solutions for improving the LSAM process and bringing its promising capabilities to full fruition.
Would you like to know more? Please check out the section ‘Prototyping & Manufacturing’ at our website here.