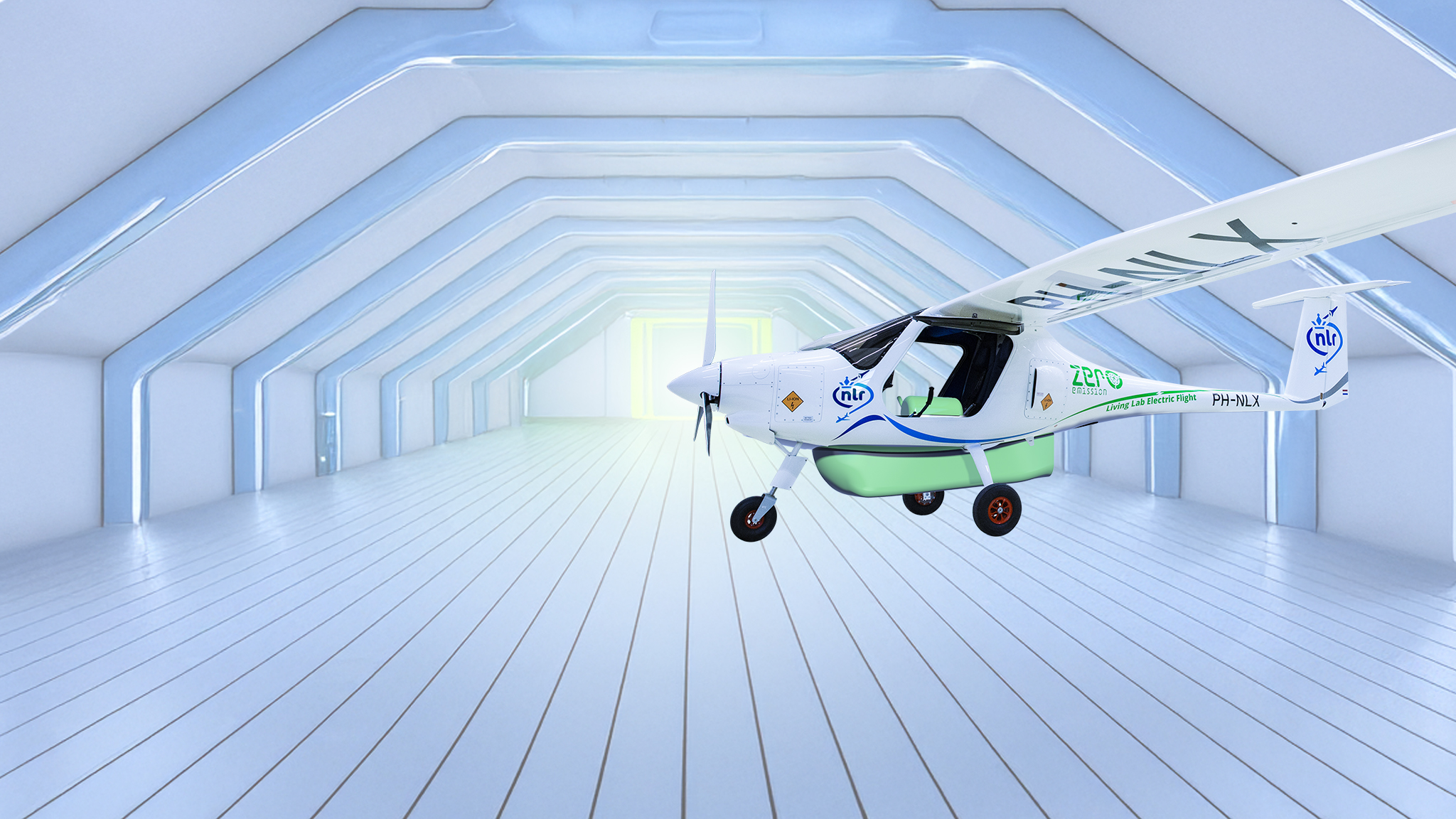
Sustainability and Environment
14 March 2025
NLR and Cryoworld collaborate on flying with liquid hydrogen
NLR is taking a further step towards more sustainable flight by partnering with Cryoworld to develop a liquid hydrogen tank. This follows the agreement with zepp.solutions for a fuel cell system. The new collaboration contributes to NLR’s ambition to conduct a demonstration flight on liquid hydrogen in 2026. NLR aims to achieve manned flight on […]
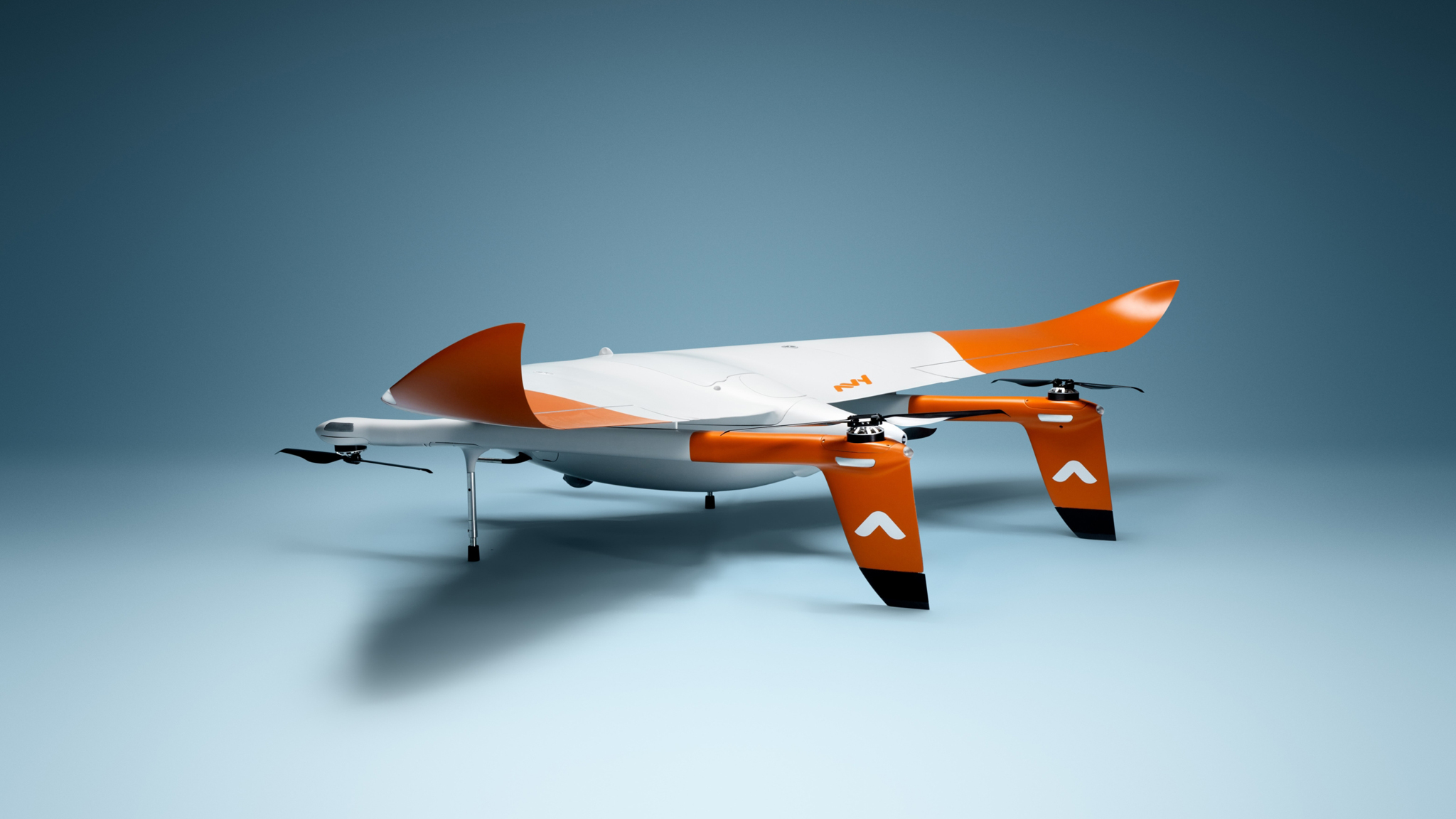
Platform System Design
22 January 2025
Avy and NLR partner to drive drone innovation
NLR has partnered with Avy, a Dutch company that develops autonomous fixed-wing drones tailored for humanitarian, health, and environmental missions, with a focus on creating a sustainable impact. NLR has acquired an Avy drone for testing and evaluation, aiming to drive innovation in aerospace applications. This collaboration supports the development of sustainable and cutting-edge drone […]
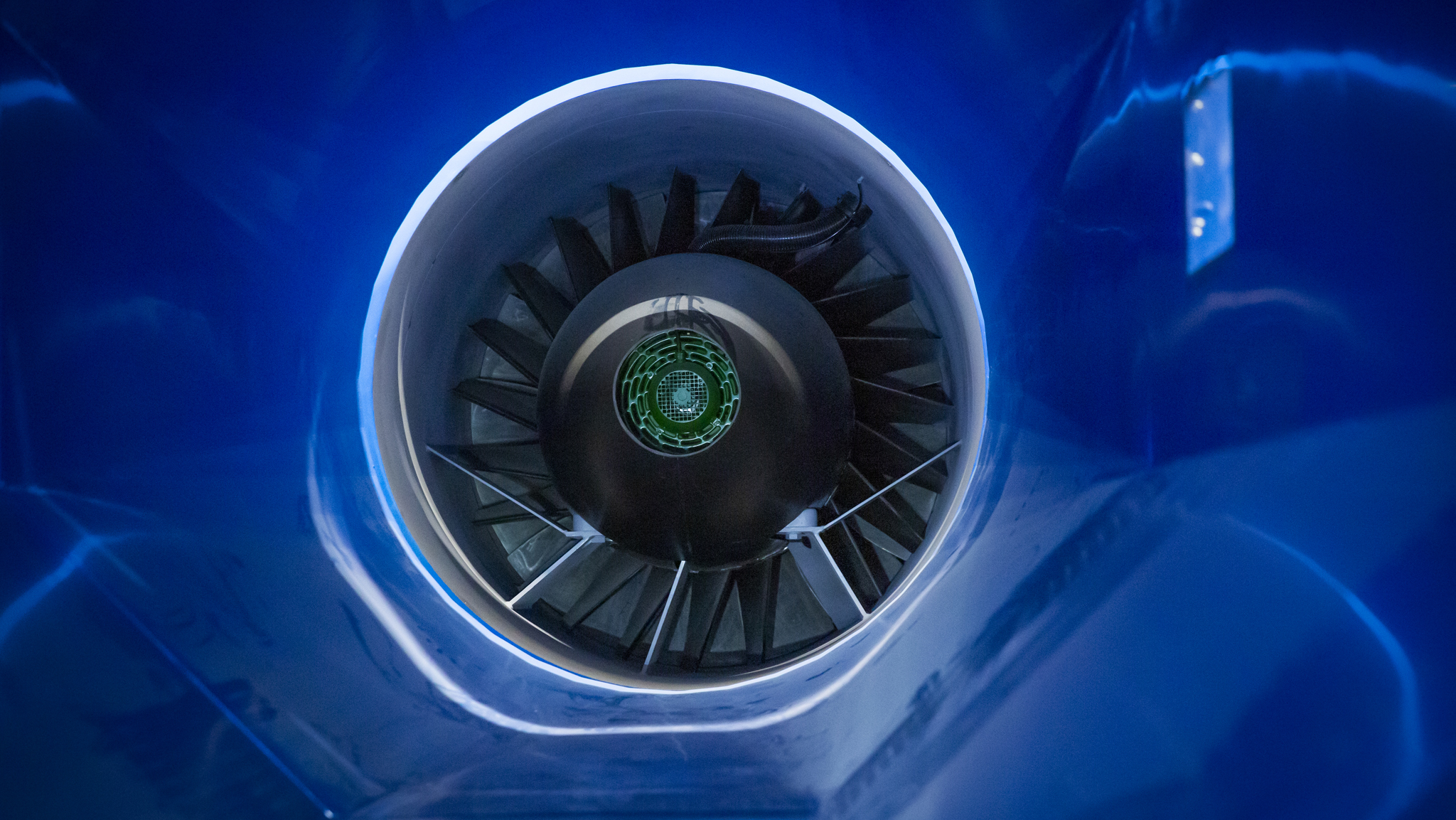
AGENDA
Let’s meet!
9-12 Apr
AERO Friedrichshafen
13-15 May
Airspace World
16-22 Jun
Paris Airshow
5 Oct
ESA/ESTEC Open day
6-7 Oct
SAMPE Europe
8-9 Oct
Electric & Hybrid
14-16 Oct
MRO Europe
18-20 Nov
Space Tech Europe
Areas of expertise
Programmes
Markets
NLR Repository
Newsroom
Stay up to date with the latest developments. In the Newsroom you can find the latest news, articles, and blogs from NLR. We also showcase a range of videos and publications here. For more video content, please visit our YouTube channel, NLRmedia.
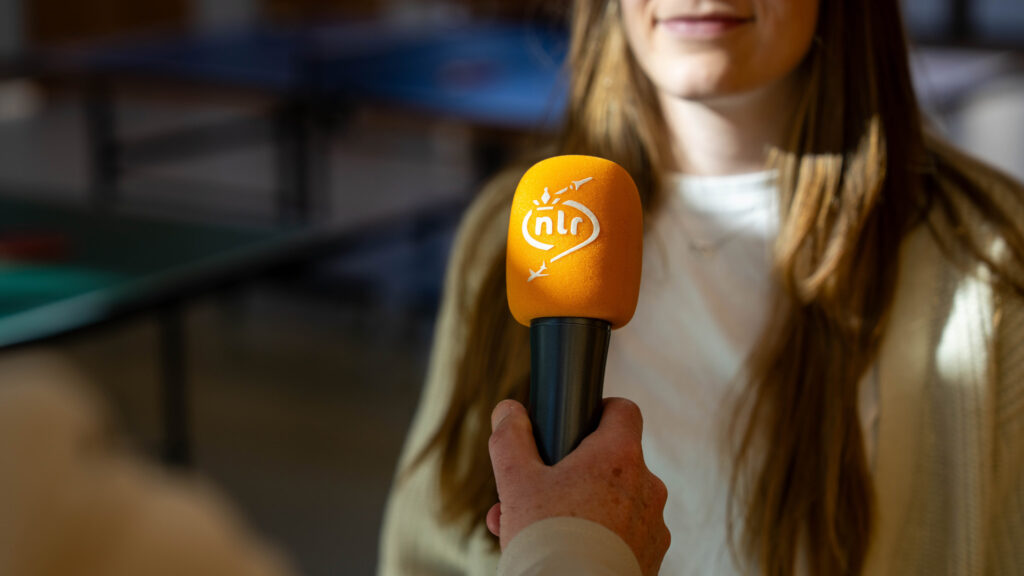