GKN Fokker, NLR, Delft University of Technology and SAM|XL, have successfully manufactured one of the world’s largest thermoplastic components as part of the Multi-Functional Fuselage Demonstrator (MFFD) project led by Airbus. This demonstrates how the use of thermoplastic composites can help realize a next-gen fleet of aircraft capable of offering the same strength and durability as aluminum, while drastically reducing the fuselage recurring cost, as well as the overall weight of aircraft and the subsequent emissions. The eight meters by four meters composite structure – delivered under the Clean Sky 2 STUNNING project – will act as the lower half of the fuselage demonstrator.
The ground-breaking aerostructure consists of more than 400 thermoplastic fibre-reinforced parts, as well as thousands of spot welds and hundreds of meters of continuous welds. The fuselage lower half will be joined at Fraunhofer IFAM in Stade with the upper half made by German Aerospace Center (DLR) Institute of Structures and Design in Augsburg.
The MFFD project aims to demonstrate High Rate Production (HRP) of a minimum of 60 aircraft per month (up to 100 aircraft), reduce the total fuselage weight by 1 ton (10%), and reduce the total fuselage recurring cost by €1 million (20%). STUNNING contributed to these objectives by showcasing novel thermoplastic manufacturing and joining technologies, as well as modular manufacturing techniques and automation.
GKN Fokker was responsible for the assembly of STUNNING, which consisted of a skin module and a floor grid module. The skin module featured a skin made as a single part by NLR using Automatic Fiber Placement, 38 stringers from Xelis made using continuous compression moulding, some of which joggled by NLR, 208 injection-moulded clips produced by the ECO-CLIP consortium, and frame sub-assemblies. The floor grid module included floor beam sub-assemblies with passenger floor beams made by automatic fibre placement. Both frame and floor beam sub-assemblies were made by GKN Fokker. The floor grid was fully equipped with various systems before installation in the skin module.
Arnt Offfringa, Director Global Technology Center NL of GKN Aerospace said: “This breakthrough project, which began in 2017, has significantly advanced our understanding and accelerated the development of thermoplastic technologies for large and complex aircraft parts. It has showcased the potential for industrial-scale application of robotic welding in the assembly of thermoplastic aerostructures. The partnership approach to STUNNING has also been a great success, showing how much progress can be made when working together. Collaboration projects such as this will be vital as we continue to push the boundaries of technology in order to meet our sustainability targets.”
“The lower skin of the MFFD, the largest known single thermoplastic piece ever made in the world, allowed us to investigate thermal and positioning effects during the manufacturing of complex thermoplastic parts”, added Johan Kos, NLR project manager.
“Next to this, the collaboration with GKN Fokker Aerostructures, Elmo, and Airbus benefits from further develop NLR’s knowledge of other relevant construction and system technologies such as of induction welding of thermoplastic parts, both experimentally and with simulation.”
The demonstrator was assembled in SAM|XL at the TU Delft Campus, where a 10x11x4m ultrasonic welding robot was built from numerous machine parts and software components supplied by European partners. Team SAM|XL was responsible for the integration of the robotic welding cell and the development of smart control and programming methods. Valuable lessons were learned related to ‘design for automated assembly’. In a joint effort, rapid energy-efficient ultrasonic welding technology was scaled-up from the lab at the Faculty of Aerospace Engineering to an industrial-scale solution for dust-less assembly of the demonstrator involving 1600 structurally sound spot welds. Further maturation of this game changing assembly technology will be accelerated in SAM|XL’s new robotic welding lab.
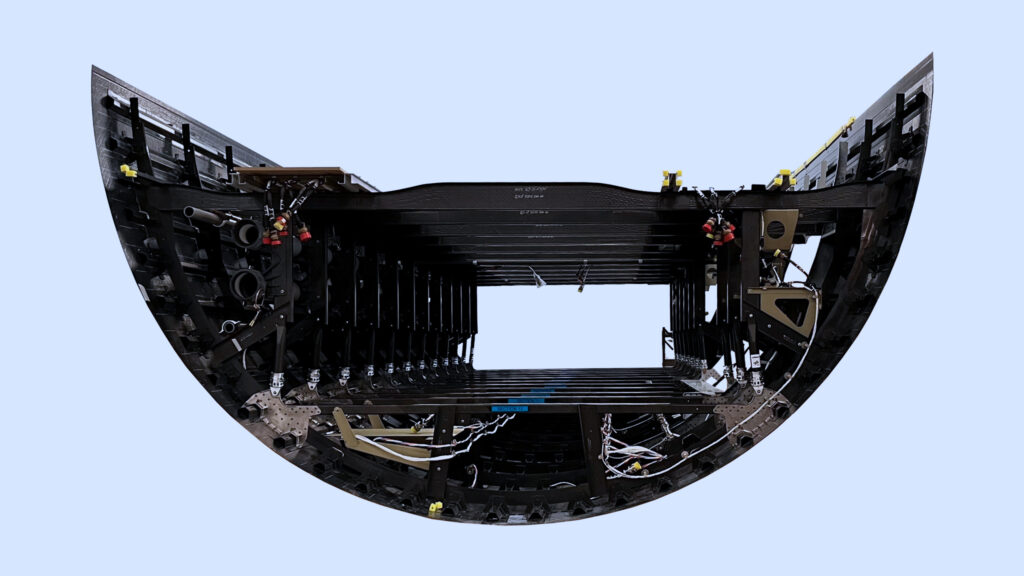
Interested?
Please also visit our website of the NLR programme ‘Development of air and space vehicles’. There you will be able to gather more information about other relevant construction and system technologies such as induction welding, aimed at the next generation of low-emission commercial airliners for short and medium ranges. See: www.nlr.org/focus-area/programmes/programme-development-of-air-and-space-vehicles/.
The results, opinions, conclusions, etc. presented in this work are those of the author(s) only and do not necessarily represent the position of the JU; the JU is not responsible for any use made of the information contained herein.
This project has received funding from the Clean Sky 2 Joint Undertaking (JU) under grant agreement No 945583. The JU receives support from the European Union’s Horizon 2020 research and innovation programme and the Clean Sky 2 JU members other than the Union.
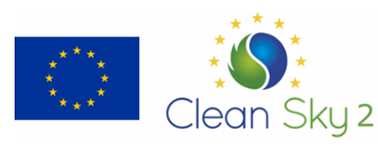