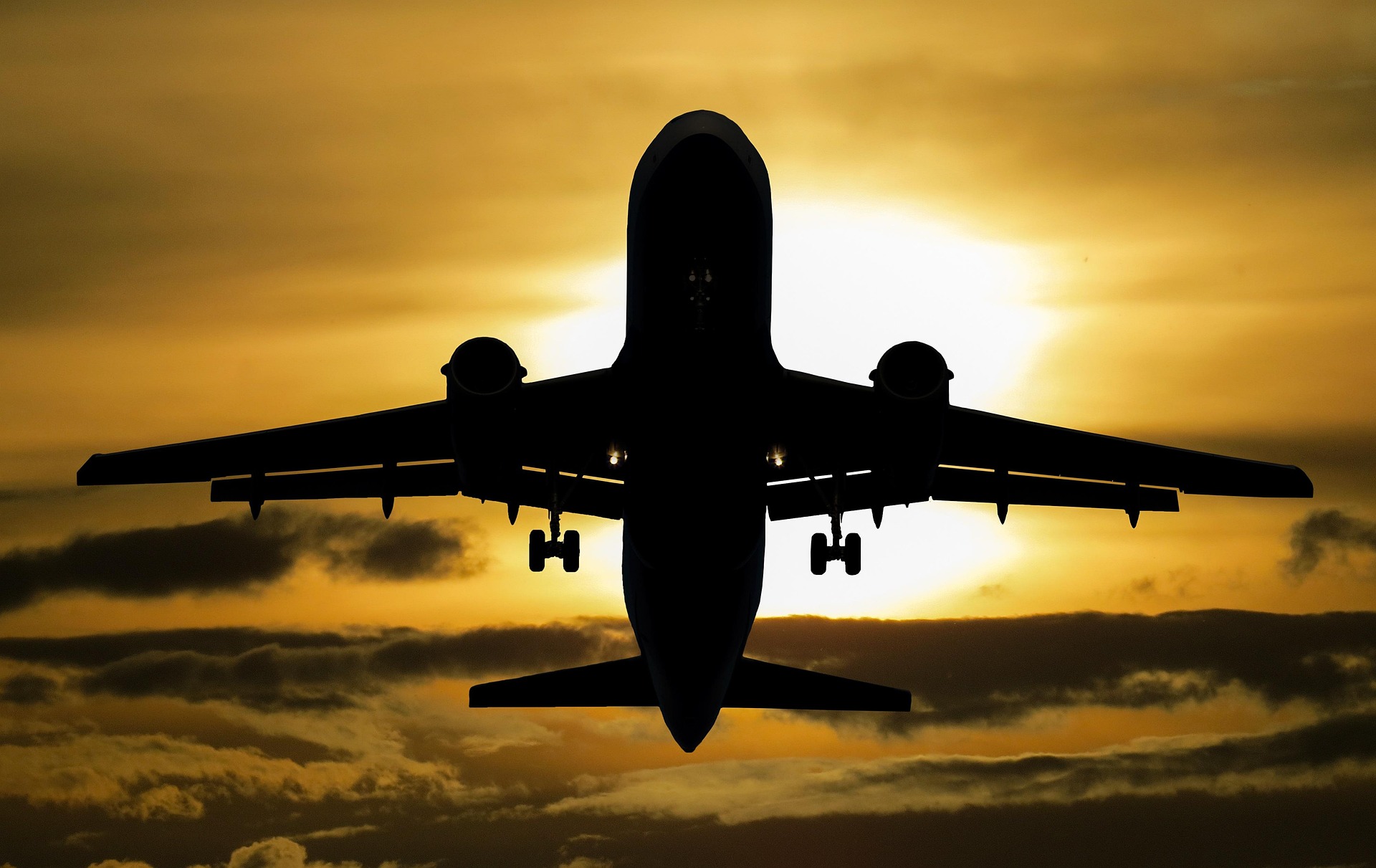
Safety and Human performance
09 July 2025
Effectiveness of flight time limitations for aircrew members
The Royal Netherlands Aerospace Centre (NLR) and its partners have completed a comprehensive research study on the effectiveness of current EU flight duty time limitations and rest requirements for aircrew members. The study, known as FTL2.0, aimed to assess whether current regulations provide sufficient protection against fatigue among aircrew members. The results of this research […]
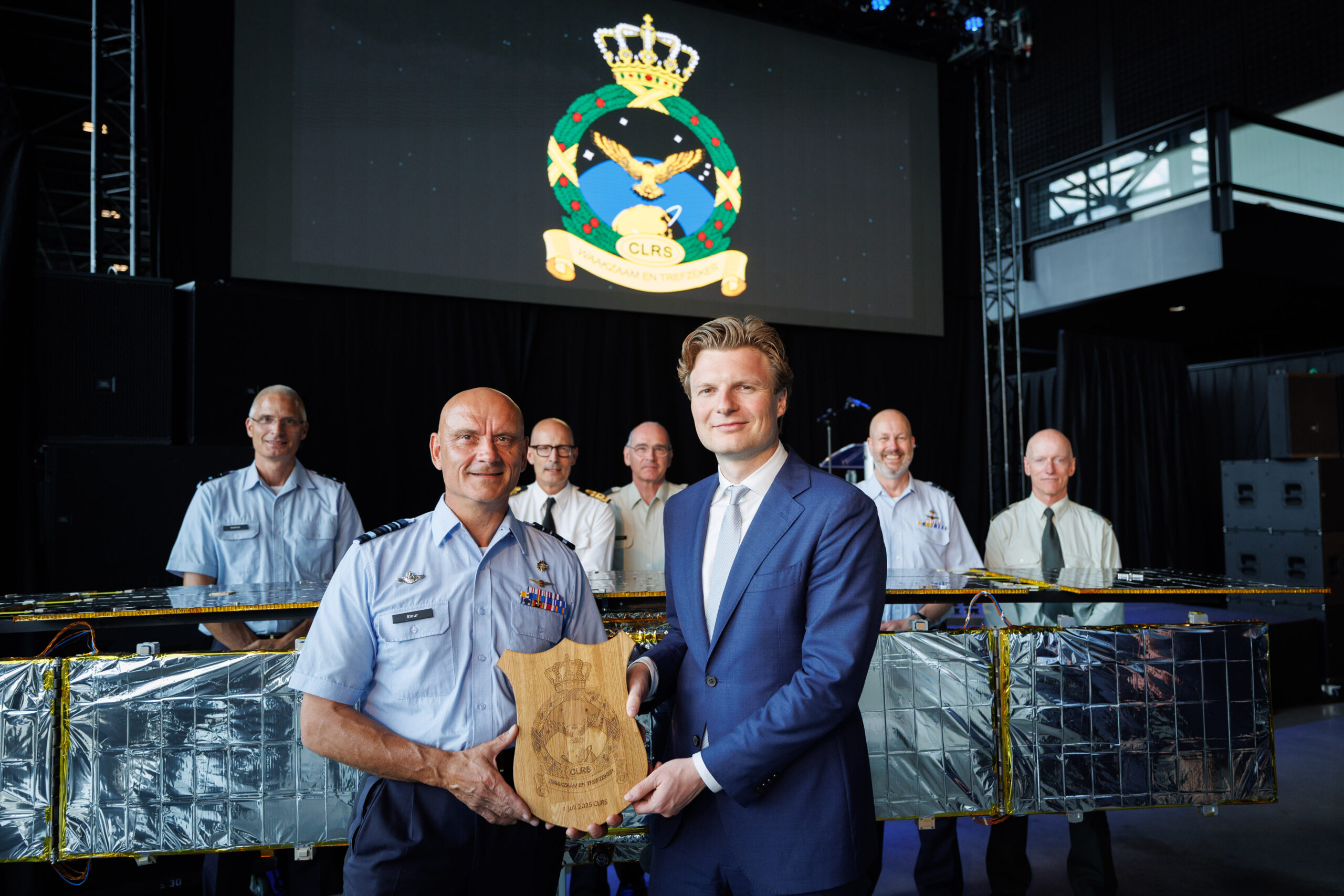
Defence and Security
02 July 2025
A new chapter for the Royal Netherlands Air Force: 112 years of history and a leap into the future
Yesterday, the Royal Netherlands Air Force (RNLAF) celebrated its 112th anniversary. In addition, the name of the Air Command (CLSK) is changing to Air and Space Command (CLRS). The name change means that space exploration is becoming more prominent within the Dutch defence. For NLR, this strong commitment by the Air Force to space power […]
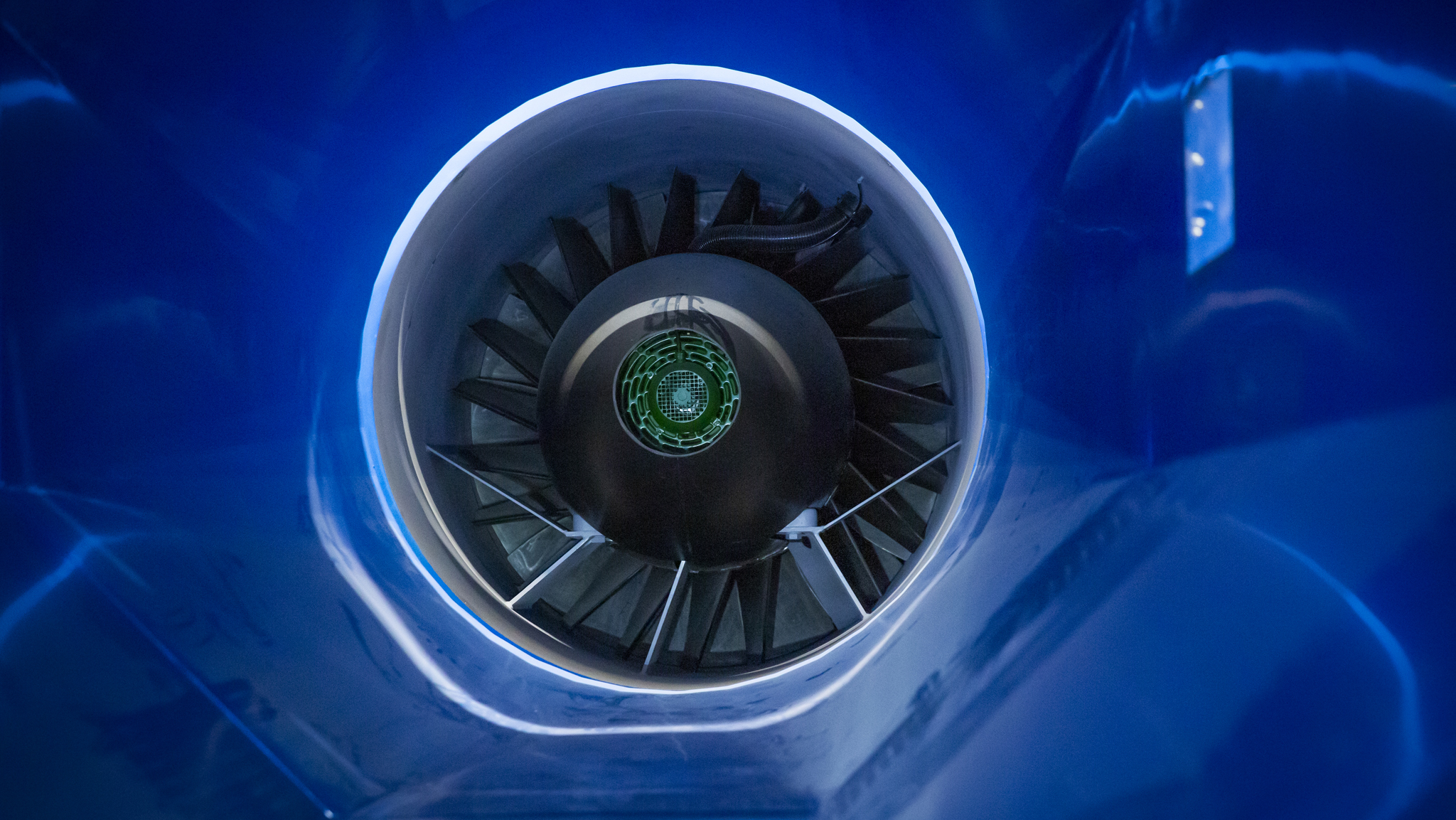
CHECK OUR NEWS IN BRIEF HERE
News updates
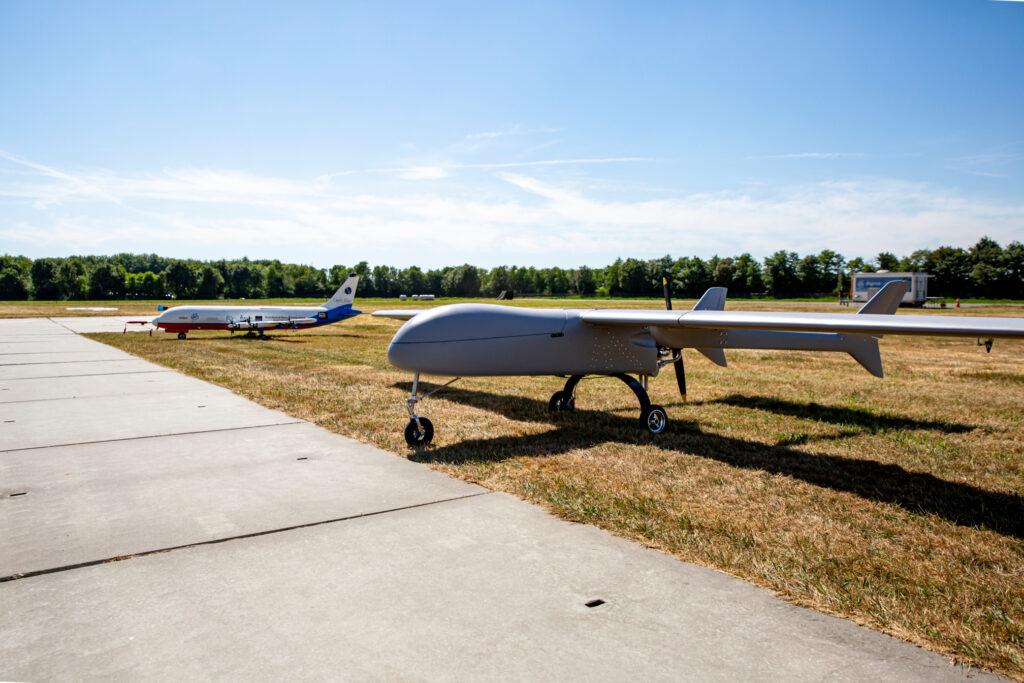
Defence & security
Accelerating drone research for Dutch Defence: the strength of an ecosystem
AGENDA
Let’s meet!
5 Oct
ESA/ESTEC Open day
6-7 Oct
SAMPE Europe
8-9 Oct
Electric & Hybrid Symposium
14-16 Oct
MRO Europe
18-20 Nov
Space Tech Europe
10-12 Mar
JEC World
Areas of expertise
Programmes
Markets
NLR Repository
Newsroom
Stay up to date with the latest developments. In the Newsroom you can find the latest news, articles, and blogs from NLR. We also showcase a range of videos and publications here. For more video content, please visit our YouTube channel, NLRmedia.
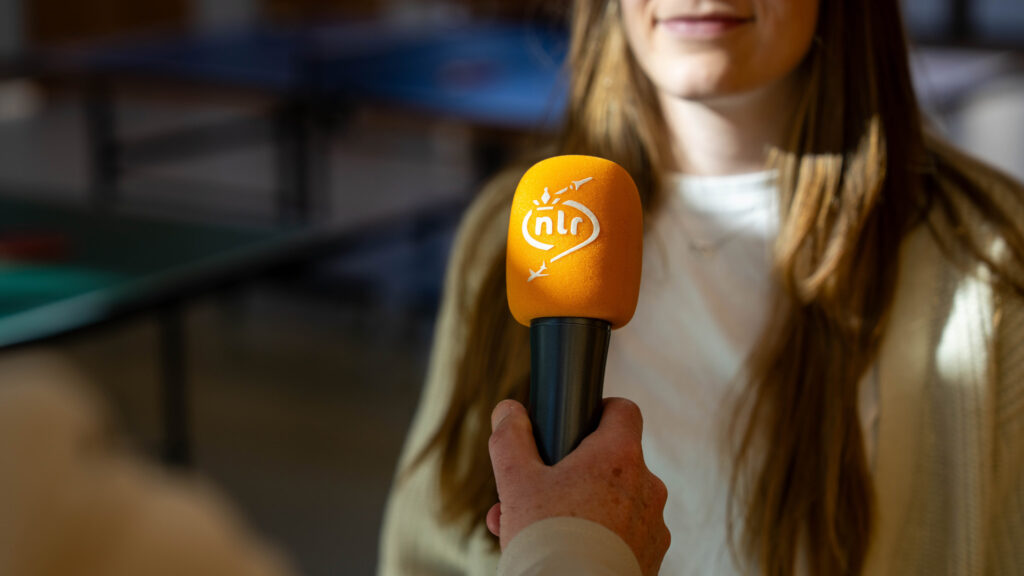