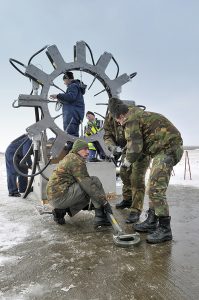
The test installation consisted of a ring with a dozen nozzles through which water was pumped at high pressure into the engine’s thrust stream.
Spraying water into the engine exhaust plume of an F-16 significantly reduces ground level noise. National Aerospace Laboratory (NLR) researchers made this discovery during two unique experiments carried out last month at Leeuwarden Air Base in the Netherlands.
During the tests, 12 nozzles (or injectors) sprayed 16 °C water at an angle into the rear exhaust plume of an F-16 as it tested its engine. The nozzles were specially constructed to transpose high pressure (up to 56 bar) at high speeds. The research was conducted in a special area where F-16 engines undergo tests following maintenance operations.
To record the noise levels, 36 microphones were directed at the rear of an F-16. During the noise recordings, which were first made without water injection and then with water injection, a number of variables were accounted for, including the F-16’s power output, the degree of water pressure, and the distance between the microphones and the aircraft. Weather conditions, such as temperature, wind speed and air pressure, were also recorded. NLR provided the water injection apparatus, the microphones, the meteo masts, a high speed camera, and the associated measurement computers.
In addition to the microphone set-up, a high speed camera, positioned to the side of the aircraft, filmed the variations in the exhaust plume, which allowed researchers to observe, in real-time, the principle by which noise is reduced. ‘Water alters the airflow, which reduces the shock waves and turbulence,’an NLR spokesperson explained. ‘What we don’t yet know, however, is exactly how the water alters the airflow. We hope the camera recordings will help us see that.Â
NLR is currently analyzing the test results. By studying the camera images, NLR researchers will identify how the water changes the airflow, and hence reduces noise levels. Thus far the preliminary results are promising. Thanks to this experiment, NLR expects, over the course of the next three to five years, to develop practical applications that not only reduce the measurable noise levels, but also change how the noise is experienced on the ground. ‘It will be less awful,’remarks the NLR spokesperson.
A third test, now in the pipeline, will aim to further optimize this water injection technique. During the tests that were already conducted, 1000 litres of water per minute was sprayed into the exhaust plumes. In the follow-up tests, NLR researchers will use less water, which they will achieve by regulating the water flow as it pulsates through the nozzles and/or by altering the shape of the nozzles.