NLR has extensive experience in virtual manufacturing and testing, utilizing modern finite element software such as ABAQUS to analyse composite and hybrid structures under various loading conditions, including quasi-static and dynamic loading, impact, and post-buckling analysis. We also have expertise in metal additive manufacturing, including distortion and thermal predictions, as well as vibration analysis and topology optimisation of aircraft parts.
We have developed specialised tools for aircraft panel analysis and optimisation, composite damage prediction, and failure analysis. Our capabilities extend to predicting temperatures and stresses in thermally loaded components, such as those found in gas turbines, and performing life predictions for these components considering factors like strength, creep, and fatigue. We also have expertise in fatigue analysis, using methods such as finite element stress analysis and automated crack propagation. By collaborating with our experts in manufacturing, testing, and non-destructive inspection, as well as materials scientists and industry partners, we can verify and validate our solutions, leading to reduced lead times and more cost-efficient execution of aircraft design, modification, and maintenance projects.
NLR can support you with:
- Complex mechanical and multi-physics analyses for aerospace applications, including advanced analyses with progressive damage prediction and post-buckling.
- Design and optimisation of thermoset and thermoplastic composites for aircraft structures.
- Design and topology optimisation of (additive manufacturing) metal structures.
- Preparation for manufacturing using curing/distortion analyses and additive manufacturing residual stress calculation.
- Virtual testing and virtual manufacturing.
- Thermo-mechanical stress analysis and life prediction.
- Fatigue analysis of components.
Documents
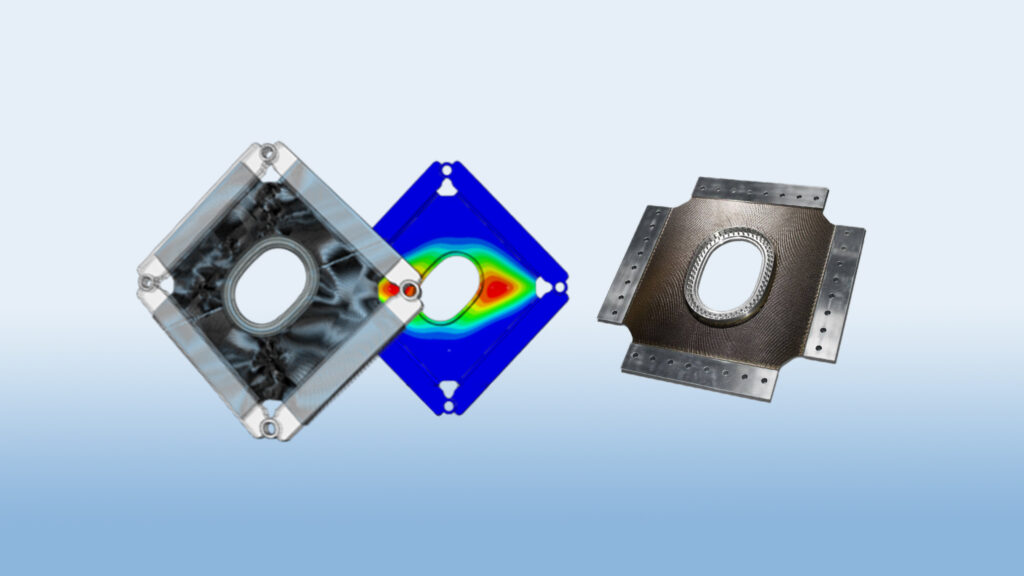
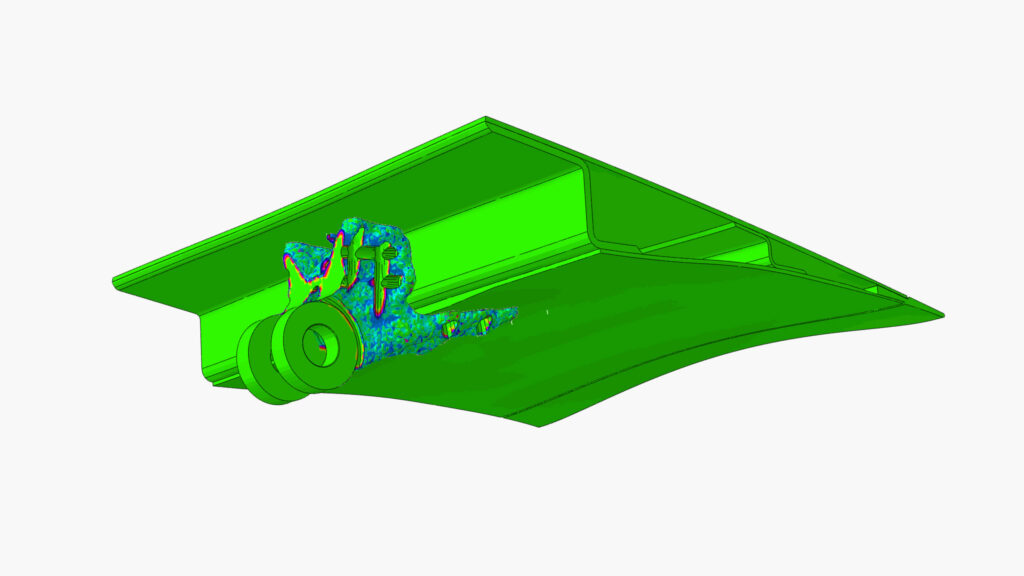