Because of the coronavirus crisis, the aviation sector has entered an uncertain phase and a lot of aircraft have been taken out of service earlier than expected. Despite that, encouraging the green transition in the post-pandemic aviation industry remains a strategic objective of governments who are looking for a way out leading to recovery.
The SUSTAINair project is being funded by the EU. The research team’s goal in this is to make the entire ecosystem of the aviation sector’s supply chain greener, in line with the Circular Economy Action Plan. This can be done by defining new standards for the manufacture of aerospace applications so that the synergy between various sectors can improve. Based on the circular economy approach, SUSTAINair is offering the aviation sector a more cost-effective, lower-emission economy and is tackling the increase in the use of raw materials as well as waste and emissions. For the Future Sky research initiative of the Association of European Research Establishments in Aeronautics (EREA), this is therefore an important reason for backing the SUSTAINair project.
European cooperation
The SUSTAINair project started in January 2021. With a budget of €5 million, eleven European research organisations and industrial partners will be collaborating on the project for 3.5 years. Jürgen Roither, a research engineer at AIT-LKR – the biggest research and technology organisation in Austria – is coordinating the project.
Roither emphasises the complementary functions of each of the project partners within a specific phase of the circular economy of a plane’s lifecycle. “SUSTAINair is focusing on all the phases of the value chain of aircraft components, from circular design to production, maintenance and repairs, and from assembly to recycling. It will stand out thanks to the combined skills and expertise of its project partners.” He adds that innovations in the materials used in the highly regulated aviation sector will need to be certified before being used in flight. That is why SUSTAINair asked for advice from the European Union Aviation Safety Agency (EASA), led by the EASA Senior Research Coordinator, Willy Sigl.
“The assistance from EASA will shorten the time to market for new and innovative products and operational models, as well as making a high level of safety, security and environmental protection feasible,” says Sigl. “EASA is therefore backing selected research projects – such as SUSTAINair – in an advisory capacity relating to aspects such as certification, regulations and safety evaluations.”
Buy-to-fly-ratio
The circular economy is an approach to using raw materials sustainably by keeping them in use for as long as possible. This raises their overall value over the course of their lifecycles. Demand in aerospace for high-quality materials unfortunately often goes hand in hand with large amounts of waste during the manufacturing process. This applies to both metal alloys and composites.
The new upcycling and recycling methods that are being developed within SUSTAINair – for both metals and composite aviation materials – will help achieve a considerable reduction in waste during manufacture and the end-of-life processes. Upcycling aims to retain the original use of materials. In this case, upcycling solutions are being developed for thermosetting materials containing fibres of carbon or glass, as well as for high-quality thermoplastic composites.
“These methods of bonding should be able to eliminate the need for rivets” – Ruben Nahuis
Roither, the SUSTAINair coordinator, adds that the project is aimed at developing the components in a way that is as close as possible to the dimensions and shape of the end product. Bringing the buy-to-fly ratio down towards unity is an absolute must for the aviation industry. That means that material losses will be cut because there is a better relationship between the mass of material used to create the component and the mass of the component itself, as ultimately used in the aeroplane. This should be made possible by using a nano-eutectic aluminium alloy recently invented by AIT-LKR, combined with advanced high-pressure injection moulding technology.
“That kind of processing is what the automotive industry refers to as ‘quick and efficient’.” According to Roither, applying the technology and materials used in SUSTAINair in the same way will make manufacturing of aerospace components ‘quick, efficient and clean’.
Reducing weight and CO2 emissions
New metal alloys and composite materials, such as those involving carbon fibre-reinforced polymers, are being used to reduce the mass and increase aerodynamic efficiency. That improves fuel consumption during the flight and cuts emissions. Small changes to materials or to the aircraft’s construction can have major effects on fuel consumption. With that in mind, SUSTAINair will not only continue developing ways to use materials as flexible options for assembly but will also look at techniques for integrating sensors into materials that are intended to be used in aircraft components. Monitoring real-time data can allow operators to adjust the flight path of an aircraft, for example. Such changes lead to lower fuel consumption, while also improving the safety and reliability of aircraft structures and reducing maintenance costs
Combinations like these of metals and composite materials have their own sets of technological challenges for bonding and repair tasks, as well as for the circular approach in the end-of-life process.
“What makes SUSTAINair unique is that we’re making the design process suitable for adding innovative techniques to the value chain that will give materials a longer operational lifespan and add value,” says Chiara Bisagni, Professor of Aerospace Structures and AIAA Fellow at Delft University of Technology in the Netherlands, “and that means taking account of disassembly at the end of the lifespan and upcycling.”
Automatically removing rivets
Aircraft are made up of numerous components put together from a variety of materials. They are currently largely connected together using rivets, but those are difficult to remove. That makes separation (and therefore efficient recycling) of aircraft components a challenge, often so costly that it stops being economically viable. In that context, NLR’s research includes looking at alternatives for bonding materials together.
“For that, we’re concentrating on induction welding of thermoplastic materials and ways of monitoring that process online,” says the NLR’s project leader Ruben Nahuis.
Rivets make aeroplanes heavier too, which negatively affects on fuel consumption. The particular expertise of NLR and the project partners in welding and other bonding techniques could ultimately eliminate the need for rivets. This innovation cannot however be applied without amendments to the current norms that have been drawn up by aviation authorities such as EASA.
The SUSTAINair project is introducing what is known as Industry 4.0 technology for processing aircraft at the end of their operational lifespans.
“We’re developing a setup for the NLR robot cell in which rivets in a bond can be detected automatically and removed,” says Nahuis. This will make it possible to separate alloys better, which will yield more high-quality recycled aircraft materials.
Flightpath 2050
The project partners are in the vanguard of circular aviation and are aiming to meet the targets set in the European Green Deal and Flightpath 2050. The technological innovations that will come hand in hand with the transition to a circular economy can be seen as an opportunity to tackle the economic effects of the coronavirus pandemic on industries throughout the aircraft component supply chain.
The partners in the project are AIT-LKR (Austria), Royal NLR (Netherlands), DLR (Germany), Joanneum Research (Austria), Johannes Kepler University Linz (Austria), Delft Technical University (Netherlands), Aerocircular (Belgium), Inocon Technologie (Austria), Invent (Germany), Dutch Thermoplastic Components (Netherlands) and RTDS Association (Austria). See the project website for additional information: www.sustainair.eu
This project has received funding from the European Union’s Horizon 2020 research and innovation programme
under grant agreement No 101006952.
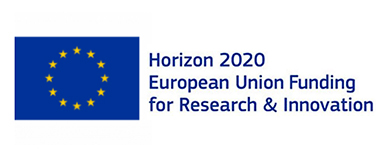