GKN Fokker, NLR, Technische Universiteit Delft en SAM|XL hebben met succes een van de grootste thermoplastische componenten ter wereld gefabriceerd als onderdeel van het project Multi-Functional Fuselage Demonstrator (MFFD) onder leiding van Airbus. Dit toont aan hoe het gebruik van thermoplastische composieten kan helpen een volgende generatie vliegtuigen te bouwen met dezelfde sterkte en duurzaamheid als aluminium. Tegelijkertijd verlaagt het materiaal de terugkerende kosten van de romp drastisch, evenals het totale gewicht van het vliegtuig en de daaruit voortvloeiende emissies. De composietconstructie van acht bij vier meter, opgeleverd in het kader van het Clean Sky 2-project STUNNING, zal als onderste helft van de rompdemonstrator fungeren.
De baanbrekende vliegtuigconstructie bestaat uit meer dan 400 thermoplastische vezelversterkte onderdelen, evenals duizenden puntlassen en honderden meters doorlopende lassen. De onderste helft van de romp zal bij Fraunhofer IFAM in Stade worden samengevoegd met de bovenste helft die is vervaardigd door het Institut für Bauweisen und Strukturtechnologie van het Deutsches Zentrum für Luft- und Raumfahrt (DLR) in Augsburg.
Het project MFFD is gericht op het demonstreren van High Rate Production (HRP) van minimaal 60 vliegtuigen per maand (maximaal 100 vliegtuigen), het verminderen van het totale rompgewicht met 1 ton (10%) en het verlagen van de totale terugkerende rompkosten met € 1 miljoen (20%). STUNNING droeg bij aan deze doelstellingen door nieuwe thermoplastische fabricage- en verbindingstechnologieën te demonstreren, evenals modulaire fabricagetechnieken en automatisering.
GKN Fokker was verantwoordelijk voor de assemblage van STUNNING die bestond uit een huidmodule en een vloerroostermodule. De huidmodule bestond uit een huid die als enkelvoudig onderdeel door NLR is gemaakt met behulp van Automatic Fiber Placement, 38 rechte verstijvers van Xelis, gemaakt met een continu persproces en deels door NLR in vorm gebogen, 208 spuitgegoten clips, geproduceerd door het consortium ECO-CLIP, en assemblagedelen van de frames. De vloerroostermodule omvat assemblagedelen voor vloerbalken waarbij de balken voor de passagiersvloer zijn gemaakt met behulp van automatic fibre placement. Zowel de assemblagedelen van de frames als die van de vloerbalken zijn gemaakt door GKN Fokker. Het vloerrooster is vóór de installatie in de huidmodule volledig voorzien van diverse systemen.
Arnt Offringa, Director Global Technology Center NL van GKN Aerospace: “Dit baanbrekende project, dat in 2017 begon, heeft ons begrip aanzienlijk verbeterd en de ontwikkeling van thermoplastische technologieën voor grote en complexe vliegtuigonderdelen versneld. Het heeft het potentieel aangetoond voor toepassing van robotlassen op industriële schaal bij de assemblage van thermoplastische vliegtuigconstructies. De partnerschapsbenadering van STUNNING is ook een groot succes en laat zien hoeveel vooruitgang er kan worden geboekt door samen te werken. Samenwerkingsprojecten zoals deze zijn van vitaal belang, omdat we de grenzen van technologie blijven verleggen om onze duurzaamheidsdoelstellingen te behalen.”
“De onderste huid van de MFFD, het grootste bekende enkelvoudige thermoplastische stuk dat ooit ter wereld is gemaakt, stelde ons in staat thermische en positioneringseffecten te onderzoeken tijdens de fabricage van complexe thermoplastische onderdelen”, vult NLR-projectmanager Johan Kos aan.
“Daarnaast is de samenwerking met GKN Fokker Aerostructures, GKN Fokker Elmo en Airbus gebaat bij de verdere ontwikkeling van NLR’s kennis van andere relevante bouw- en systeemtechnologieën, zoals het inductielassen van thermoplastische onderdelen, zowel experimenteel als met simulatie.”
De demonstrator werd geassembleerd in SAM|XL op de TU Delft Campus, waar een ultrasone lasrobot van 10 x 11 x 4 meter werd gebouwd uit talloze machineonderdelen en softwarecomponenten die door Europese partners werden geleverd. Team SAM|XL was verantwoordelijk voor de integratie van de robotlascel en de ontwikkeling van slimme besturings- en programmeermethoden. Er werden waardevolle lessen geleerd met betrekking tot “het ontwerpen voor geautomatiseerde assemblage”. In een gezamenlijke inspanning werd de snelle en energiezuinige ultrasone lastechnologie opgeschaald van het laboratorium van de faculteit Luchtvaart- en Ruimtevaarttechniek naar een oplossing op industriële schaal voor stofvrije assemblage van de demonstrator. Hierbij werden 1600 structureel solide puntlassen aangebracht. De verdere rijping van deze baanbrekende assemblagetechnologie zal worden versneld in het nieuwe robotlaslaboratorium van SAM|XL.
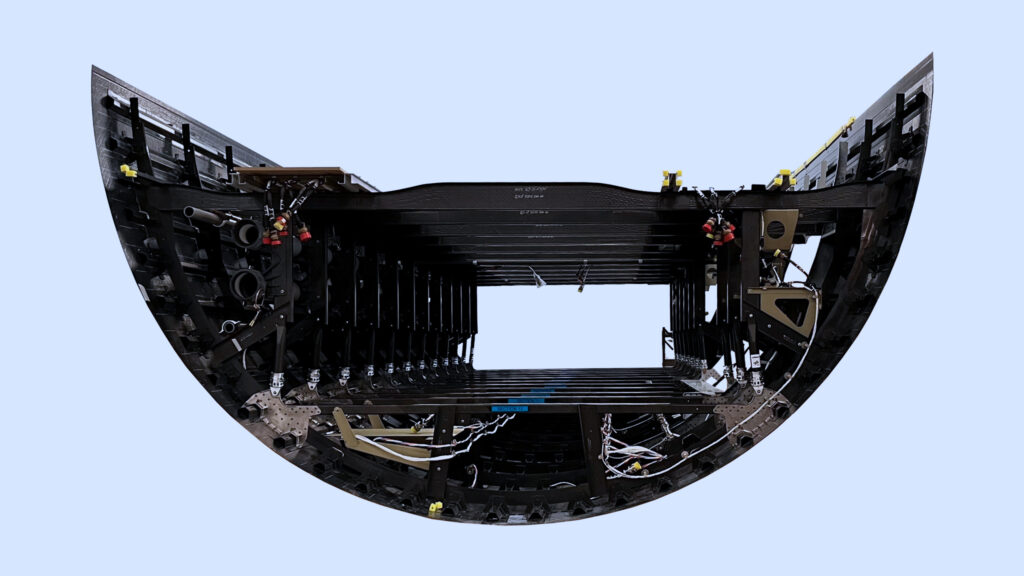
Interesse?
Bezoek ook de pagina’s over het NLR-programma ‘Ontwikkeling van lucht- en ruimtevoertuigen’ op onze website. Hier vindt u meer informatie over andere relevante bouw- en systeemtechnologieën, zoals inductielassen, die zijn gericht op de volgende generatie commerciële passagiersvliegtuigen met lage emissies voor korte- en middellange afstanden. Zie: www.nlr.org/focus-area/programmes/programme-development-of-air-and-space-vehicles/.
De in dit werk gepresenteerde resultaten, meningen, conclusies, enzovoort zijn uitsluitend die van de auteur(s) en vertegenwoordigen niet noodzakelijkerwijs het standpunt van de JU; de JU is niet aansprakelijk voor enig gebruik dat van de hierin opgenomen informatie wordt gemaakt.
Dit project heeft financiering ontvangen van de Clean Sky 2 Joint Undertaking (JU) onder subsidieovereenkomst nr. 945583. De JU ontvangt steun van het onderzoeks- en innovatieprogramma Horizon 2020 van de Europese Unie, en van de lidstaten van Clean Sky 2 JU buiten de Unie.
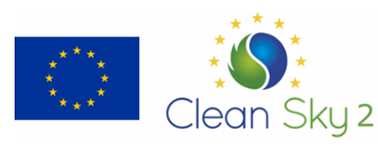