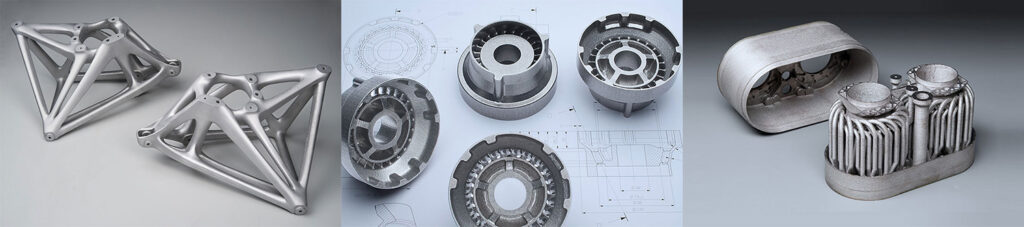
“In het eerste programma hebben we uitsluitend gebruik gemaakt van laserpoederbedfusie (LPBF). In het nieuwe programma gaan we ook met een ander additief productieproces aan de slag”, zegt Marc de Smit, R&D engineer bij Koninklijke NLR. “We beginnen nu ook met directed energy deposition (DED)waarbij metaalpoeder uit een spuitmond direct met een laser op zijn plaats wordt gesmolten. Het is een proces dat geschikt is voor het maken van grote onderdelen, het toevoegen van onderdelen aan bestaande producten of het uitvoeren van reparaties.”
Voordat we dieper in deze technologie duiken, trappen we af met wat geschiedenis. “De hype rondom metaalprinten bereikte in 2014 zijn hoogtepunt: de verwachtingen waren hooggespannen en iedereen was bijzonder geïnteresseerd”, zegt De Smit. „Metal additive manufacturing (MAM) biedt een groot aantal mogelijkheden, waaronder de mogelijkheid om producten te maken die lichter zijn, uit minder componenten bestaan en beter presteren. Deze technologie biedt mogelijkheden om vliegtuigen lichter en dus zuiniger en duurzamer te maken. Er kunnen verschillende toepassingen worden bedacht in andere markten waar de vrijheid in ontwerp van metal additive manufacturing aanzienlijke voordelen kan opleveren. NLR heeft al verschillende toepassingen in de praktijk gebracht. Hydraulische systemen kunnen worden geoptimaliseerd zodat de weerstand tegen vloeistofstromen minder wordt; Er kunnen lichtere en efficiëntere warmtewisselaars worden geproduceerd en structurele onderdelen kunnen zodanig worden geoptimaliseerd dat het gewicht substantieel wordt verminderd.”
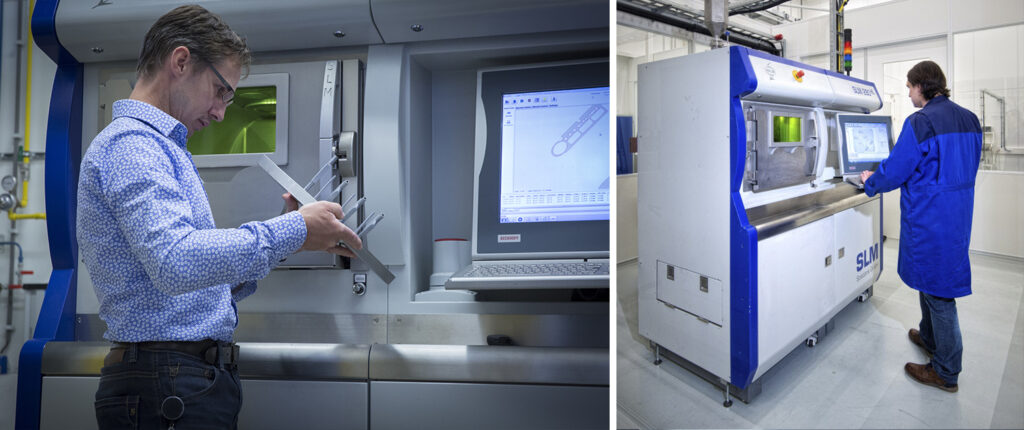
Een probleem met de nieuwe technologie is dat er veel kennis nodig is om echt goede en veilige producten te kunnen leveren. Hierbij gaat het niet alleen om het productontwerp, maar ook om kennis over de basismaterialen, het proces, de materiaaleigenschappen en last but not least de eisen waaraan het product moet voldoen om gecertificeerd te worden.
De inhoud van dit samenwerkingsproject is gebaseerd op de behoeften van de geïnteresseerde bedrijven. Belangrijke onderwerpen zijn bijvoorbeeld procesoptimalisatie zodat goede materialen gemaakt kunnen worden, het bepalen van de fysieke sterkte van geprint werk, nabewerking van geprinte producten en ontwerpen voor additieve productie zodat maximaal voordeel behaald kan worden. Binnen het programma zijn de door verschillende bedrijven aangeleverde technologiedemonstrators geoptimaliseerd en ontwikkeld.
Grote vraag naar kennis
De Smit legt uit dat er in de beginperiode veel vraag was naar kennis over alle aspecten van metal additive manufacturing , zoals vragen over ontwerpregels, het proces, warmtebehandelingen en nabewerking. Bij de start van het eerste programma was dergelijke kennis in Nederland slechts in zeer beperkte mate beschikbaar. “Voor het proces om poederdeeltjes te smelten met lasers moeten een groot aantal verschillende instellingen gecombineerd worden”, zegt De Smit. “Denk bijvoorbeeld aan variabelen als het laservermogen, de snelheid, de afstand tussen de laserscanlijnen, de dikte van de poederlaag en nog veel meer. Voor elk materiaal moeten andere parameters gebruikt worden. Een van de doelen was om een efficiënte methode te bedenken om snel de juiste instellingen te selecteren, en dat is ons gelukt.”
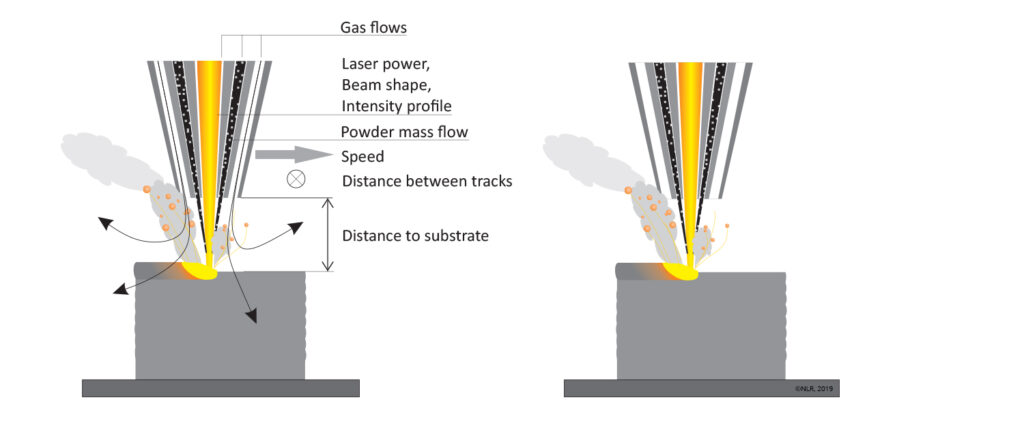
Ontwerpoptimalisatie
Een van de grootste voordelen van metal additive manufacturing is de enorme ontwerpvrijheid. Dankzij dit proces is het mogelijk om producten te ontwerpen die lichter zijn en beter presteren dan producten die met conventionele methoden worden gemaakt. Het voorbeeld dat De Smit geeft is een T-stuk voor een hydraulisch systeem dat de stromingsweerstand vermindert. “Door materiaal te verwijderen waar je het niet nodig hebt, wordt het ontwerp lichter en de verbeterde interne vorm betekent dat er in het T-stuk minder weerstand is tegen de vloeistofstroom. Een bijkomend voordeel is dat door de lagere stromingsweerstand een lichtere pomp kan worden toegepast.”
Certificering
Als de geprinte componenten uiteindelijk in veeleisende toepassingen moeten worden gebruikt, is certificering van de 3D-geprinte items essentieel. De benodigde procedures hiervoor zijn nog niet ontwikkeld en daarom is deze doelstelling een van de kernelementen van het nieuwe programma.
“Het lastigste is dat je moet bewijzen dat je precies weet wat je doet”, zegt De Smit. “Je moet kunnen aantonen dat materialen geen gebreken vertonen die ertoe kunnen leiden dat een product faalt. Dat kun je bijvoorbeeld doen met een CT-scan, maar dat is tijdrovend en duur omdat ieder onderdeel afzonderlijk gescand moet worden. Het is daarom gunstig dat er gedetailleerde procesmonitoring wordt ontwikkeld, waarmee kan worden vastgesteld wanneer materiaalfouten ontstaan.”
De Smit legt verder uit dat het monitoren van de processen niet alleen gaat over de directe kennis van de materialen en het proces, maar ook over het verwerken van grote hoeveelheden data. “Er worden monitoringsystemen gebruikt om in de gaten te houden wat er in het smeltbad gebeurt. Tijdens het productieproces wordt een schat aan informatie gegenereerd. Al die gegevens zouden ons moeten helpen bepalen of het proces goed is verlopen of niet. In de toekomst willen we ook graag kunstmatige intelligentie toevoegen aan de processen, zodat geconstateerde gebreken bijvoorbeeld kunnen worden gerepareerd.”
Technologiedemonstrators
Al deze werkpakketten kwamen samen in een zogenaamd ’technologiedemonstrator’-pakket. Deelnemende bedrijven kregen de mogelijkheid om hun eigen technologiedemonstrator in het programma op te nemen. De individuele eisen van de verschillende partners zijn van groot belang omdat elke branche andere eisen stelt en andere doelstellingen heeft.
De Smit: “Voor diverse partners hebben wij demonstrators ontworpen en geproduceerd. Voor Mokveld is een onderdeel gemaakt dat een betere scheiding van water uit olie mogelijk maakt. De Oerlikon-demonstrator is een draaderosietool die herontworpen is met topologie-optimalisatie. Voor Fokker Aerostructures optimaliseerden we hydraulische manifolds. Hiermee werd een aanzienlijke gewichtsbesparing en drukvalreductie bereikt. Voor Fokker Services ontwierpen we een structurele bracket. Het gewicht hiervan is aanzienlijk lager, terwijl de sterkte-eisen nog altijd ruimschoots voldoen.”
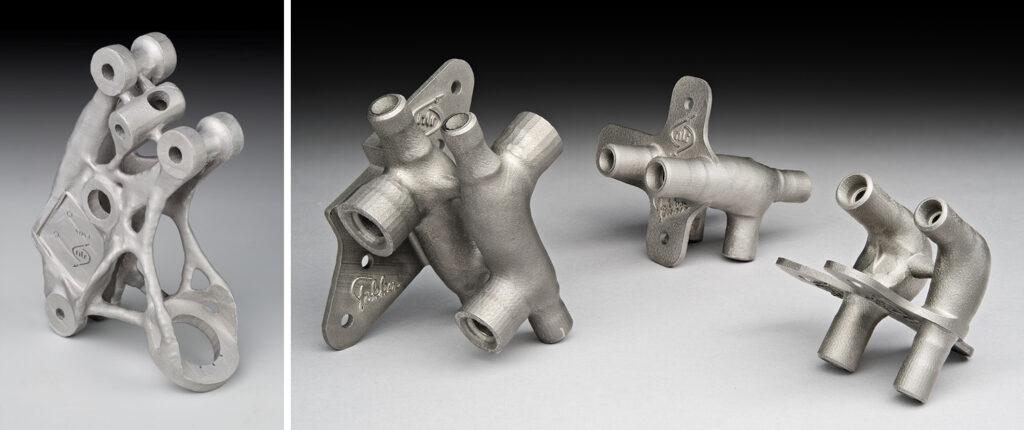
Nieuw programma
Het nieuwe vierjarige programma is in april 2019 van start gegaan. De inhoud is opnieuw op basis van de verlanglijstjes van deelnemers, samengesteld. Het belangrijkste doel van dit nieuwe programma is om de deelnemers te ondersteunen in hun ambitie om gecertificeerde metalen Additive Manufacturing (AM)-componenten te introduceren. In een groot aantal sectoren, met name de lucht- en ruimtevaart en hightech, is het belangrijk om aan te tonen dat het Additive Manufacturing-proces betrouwbaar en reproduceerbaar is. Certificering van AM-componenten is belangrijk om een veilige en duurzame implementatie in verschillende veeleisende toepassingen mogelijk te maken.