De digital twin verbetert de controle over het productieproces en helpt dit te optimaliseren. De digitale versie doorloopt dezelfde processtappen als zijn tegenhanger in de ‘echte’ wereld. Dit ‘beeld’ biedt steeds meer mogelijkheden.
Senior wetenschapper Erik Baalbergen, al enkele jaren betrokken bij de ontwikkeling van deze technologie, legt uit wat dit voor NLR betekent.
“We willen een duidelijker beeld van de toepassing van innovatieve ondersteunende technologieën bij de ontwikkeling en productie van lucht- en ruimtevaartproducten, zodat de productie efficiënter en groener kan. Als onderdeel daarvan onderzoeken we hoe mensen en systemen samenwerken. Dankzij moderne automatisering en de aanwezigheid van steeds meer sensoren hebben we toegang tot een grote hoeveelheid data. Deze innovatie geeft ons nieuwe inzichten tijdens de productie van composietonderdelen en helpt ons productieprocessen te optimaliseren. We hebben hiervoor, samen met Fokker Landing Gear, een paar jaar geleden een testomgeving opgezet bij NLR in de Noordoostpolder.”
“We willen bijvoorbeeld de operators helpen”, legt Baalbergen uit. “Er staat in deze pilot plantonder meer een RTM-machine (Resin Transfer Moulding) voor harsinjectie. Als je eenmaal een halffabricaat gemaakt hebt, dan moet je dat injecteren met hars. De RTM is in feite een conglomeraat van machines, waaronder de harsinjector maar ook een aantal heetwaterbaden om de hars op weg naar de mal warm te houden. Dat is een behoorlijk complexe opstelling en een operator moet er continu bij zijn om alles in de gaten te houden.”
NLR werkt, met de rol van de operator als uitgangspunt, aan deze nieuwste ontwikkelingen op het gebied van digitale ondersteuning van productieprocessen. Volgens Baalbergen was het de uitdaging om daarbij de OT- en IT-technieken intelligent te verbinden.
“Kortom een echte industriële automatiseringsklus voor de RTM-opstelling, en we hebben het concept van de ‘digital twin’ omarmd als een geautomatiseerde kopie van het RTM-proces.”
Hulp voor de operator
Using the digital simulacrum has a clear, predefined goal.
Het inzetten van een digital twin had een duidelijk vooropgezet doel.
“Uiteindelijk moet deze digital twin de operator helpen”, zegt Baalbergen, “zodat deze minder vaak hoeft te reageren op allerlei alarmbellen. De digital twin moet alle details in de gaten houden. De operator kan zich dan volledig richten op specifieke fasen van het harsinjectieproces, waarbij je precies dat fingerspitzengefühl nodig hebt voor het reageren op bepaalde situaties. Daarvoor moet je simulaties laten draaien en data-analyses doen. Uiteindelijk streven we een hoger doel na: we willen de hele pilot plant door één operator laten controleren. Daarbij moet je niet alleen nog veel meer zaken automatiseren, maar ook intelligenter reageren op incidenten. Je moet teveel valse alarmen voorkomen, dus je wilt alleen de essentiële alarmmeldingen doorgeven aan de operator.”
Daarbij moet NLR wel diverse uitdagingen zien te overwinnen, mede omdat er strenge regels gelden voor de vliegtuigindustrie.
“Alle processen zijn gecertificeerd”, zegt Baalbergen, “dus we mogen ook niet teveel zomaar aan een computer overlaten. Een mooi voorbeeld: de temperatuur van een mal moet 80 graden blijven en de alarmbel moet afgaan bij 82 graden. De standaardactie is dat de operator bij een alarmbel de temperatuurinstelling iets omlaag haalt. Dat zou je natuurlijk kunnen automatiseren, maar dat mag niet. Het proces moet door een operator worden beoordeeld. Er zijn veel randvoorwaarden, maar daarbinnen proberen we toch zoveel mogelijk te automatiseren en de operator te ondersteunen.”
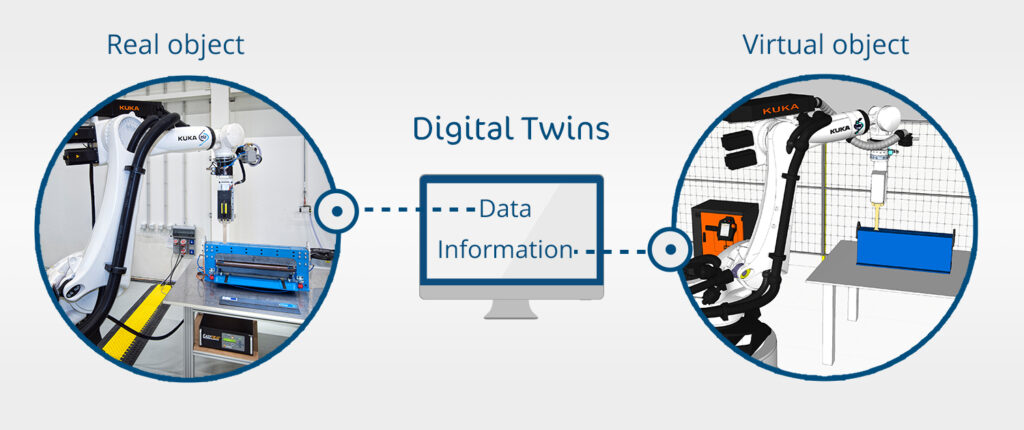
Verdere ontwikkelingen
Als voortvloeisel van de ontwikkeling van een digital twin is Koninklijke NLR samen met een vliegtuigbouwer, een hogeschool en een leverancier van apparatuur bezig om in het project Luxovius een digital twin voor een innovatief productieproces te ontwikkelen.
“Daarvoor zijn nog veel meer sensoren in machines nodig”, zegt Baalbergen, “omdat je voor een goede digital twin zoveel mogelijk data wil gebruiken. Uiteindelijk willen we met dit project een productieproces creëren dat zo efficiënt en ‘groen’ mogelijk is, waarbij zo min mogelijk energie wordt verbruikt en zo min mogelijk afval wordt geproduceerd.”
Ook zal het vak van de operator niet verloren gaan door deze technische ontwikkelingen, zegt hij.
“Je gaat de operator echt niet uitfaseren, maar inzetten op een gebied waar deze veel beter in is; de eigen creativiteit meer ruimte geven. We hebben operators geïnterviewd en als je uitlegt wat de voordelen van digital twin-technologie zijn, dan worden ze ook enthousiast. Je helpt hen om de saaie administratieve aspecten van het werk te verminderen. Je moet de potentie van de nieuwe technologie dus goed uitleggen. Tevens willen we bereiken dat bij de digitalisering van complexe productieprocessen en -systemen de mens zich niet hoeft aan te passen aan de computer. Laat die computer zich maar aanpassen aan de mens! Zo kun je veel efficiënter werken. Digital twin-technologie maakt het voor de eindgebruiker gewoon gemakkelijker, zodat de operator zijn of haar creativiteit beter kan inzetten.”
Dit artikel is een vertaling van een aangepaste versie (gemaakt met toestemming van de auteur, Dimitri Reijerman) van een originele tekst op de website van branchevereniging FHI voor het Machinebouwevent van 1-3 december 2020.
Want to know more?
Koninklijke NLR beschikt over een onderzoeksplatform (productiemachine, echt vliegtuig en/of simulatieomgeving) om de mogelijkheden van Digital Twin en Industrie 4.0 te onderzoeken. Lees meer over De Digital Twins-mogelijkheden van NLR