Duurzame luchtvaart is tegenwoordig een veelbesproken onderwerp waarbij de focus ligt op het verminderen van het constructiegewicht, wat leidt tot lager brandstofverbruik en minder emissies. Dit kan worden bereikt door metalen onderdelen te vervangen door equivalente componenten van composietmaterialen die een hoge sterkte-stijfheidverhouding hebben ten opzichte van het gewicht. Door dergelijke aanpassingen kan het totale gewicht aanzienlijk worden verlaagd zonder dat de prestaties verminderen.
Composietmaterialen worden in de sector al op grote schaal gebruikt, maar er is nog steeds behoefte aan efficiëntere fabricagemethoden. Daarom onderzoekt NLR in het kader van het Mobiliteitsfonds de grootschalige additieve productie van vezelversterkte thermoplastische materialen. Dit is een relatief nieuwe technologie die alle voordelen van 3D-printen biedt (zoals ontwerpvrijheid, korte doorlooptijden en kosteneffectiviteit) op een grotere schaal, tot 2×2 meter in de huidige opstelling van NLR. Een ander belangrijk voordeel is het minimale materiaalverlies tijdens de fabricage, wat het proces vanaf het begin van de productielijn duurzaam maakt.
Het programma
Het programma van het Mobiliteitsfonds van de overheid is bedoeld om de inspanningen van de Nederlandse industrie voor een duurzamere luchtvaart nieuw leven in te blazen. Binnen het programma van het Mobiliteitsfonds worden verschillende projecten uitgevoerd. Een daarvan richt zich op de ontwikkeling van thermoplastische vezelversterkte concepten voor de markten voor Urban Air Mobility (UAM) en Sub-Regional Electrical Vehicle (SREV), die de hoge kwaliteitsniveaus van de luchtvaartsector vereisen maar tegelijkertijd de productiesnelheden van de auto-industrie halen.
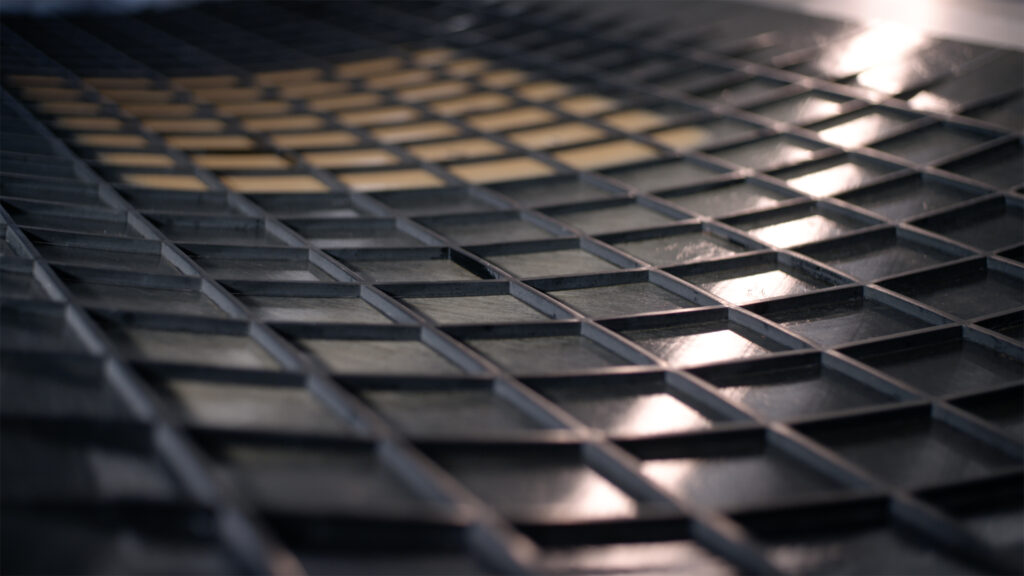
Het thermoplastische project is opgesplitst in verschillende groepen gerelateerde taken (werkpakketten genoemd). NLR is betrokken bij diverse taken en voert zelfstandig onderzoek en ontwikkeling uit op gebieden als robotgestuurd inductielassen voor thermoplasten, digitalisering van het lasproces en het gebruik van thermoplasten in verstijvingsconstructies. Met een specifieke focus op het laatste onderwerp wordt het Large-Scale Additive Manufacturing-proces (LSAM) geëvalueerd als mogelijke oplossing voor snelle fabricage van verstijvingsrasters of honingraatstructuren voor UAM- en helikopterdeuren en -luiken. Het uiteindelijke doel is om deze structuren te printen op voorgeconsolideerde panelen met meerdere krommingen.
De technologie
Large-Scale Additive Manufacturing (ook bekend als Big Area Additive Manufacturing of Fused Granulate Fabrication) is een fabricageproces waarbij materiaal laag voor laag wordt afgezet in een bepaald gebied. De opstelling bestaat uit een extruder (die het materiaal smelt en uitspuit), bevestigd aan een robot (die de extruder verplaatst op basis van de te printen geometrie), en een printbed (waarop het materiaal wordt aangebracht).
De materialen
R&D-engineer Ana Ramirez de las Heras, werkzaam op de afdeling Structures Technology van de divisie Aerospace Vehicles van NLR, heeft de leiding over dit relatief nieuwe fabricageproces. Volgens haar is niet elk materiaal geschikt om in een ‘vliegend onderdeel’ te worden verwerkt, omdat het moet voldoen aan de kwaliteits- en veiligheidseisen voor de lucht- en ruimtevaart en als zodanig moet worden gecertificeerd.
“De huidige focus ligt op koolstofvezelversterkte hoogwaardige thermoplasten zoals PEEK, laagsmeltende PAEK of PPS, die in zeer veeleisende toepassingen kunnen worden gebruikt”, zegt Ramirez de las Heras. “Het is echter juist het speciale gedrag van deze materialen dat het lastiger maakt om ze met deze technologie te verwerken.”

“Een van de grootste uitdagingen van LSAM is het bepalen van de optimale laagtijd, oftewel de tijd die nodig is om één volledige laag te printen. Als de geselecteerde laagtijd te kort is, heeft de vorige laag niet genoeg tijd gehad om af te koelen en stort de volgende laag in. Als de laagtijd echter te lang is, stolt het materiaal, wat de hechting met de volgende laag verzwakt en leidt tot slechte mechanische eigenschappen in het eindproduct. De gekozen laagtijd is afhankelijk van het materiaal.”
Er wordt speciale aandacht besteed aan temperatuurregeling van de vorige laag en het implementeren van technologieën zoals infrarood- of laserverwarming. Dit kan de mogelijkheden van de technologie vergroten.
De opstelling
Sinds begin 2023 werkt de afdeling Structures Technology van NLR aan de implementatie van een eigen LSAM-opstelling, bestaande uit de nieuwste extruder van CEAD, een Nederlandse technologieleverancier van 3D-printapparatuur. Het model S25 is een lichtgewicht extruder (minder dan 30 kilogram) met een maximale output van 24 kilogram per uur, die is ontwikkeld voor high-end-toepassingen. De S25 is ontworpen voor montage op een robotarm zoals de KUKA KR240 die bij NLR wordt gebruikt. Dit is een robot met een hoge payload en een groot bewegingsbereik (zes assen), wat printen op grote schaal mogelijk maakt.
De extruder gebruikt vier verschillende verwarmingszones om het thermoplastische materiaal geleidelijk te smelten zonder het te beschadigen, en kan temperaturen tot 400 °C bereiken. Het systeem is geschikt voor het verwerken van hoogwaardige thermoplastische materialen (zoals de eerder genoemde) met minimale slijtage van de machine, zelfs bij het verwerken van korte glas- en koolstofvezels. De spuitmond biedt flexibiliteit in de haalbare wanddikte, wat van toegevoegde waarde is wanneer het proces voor diverse toepassingen moet worden gebruikt.
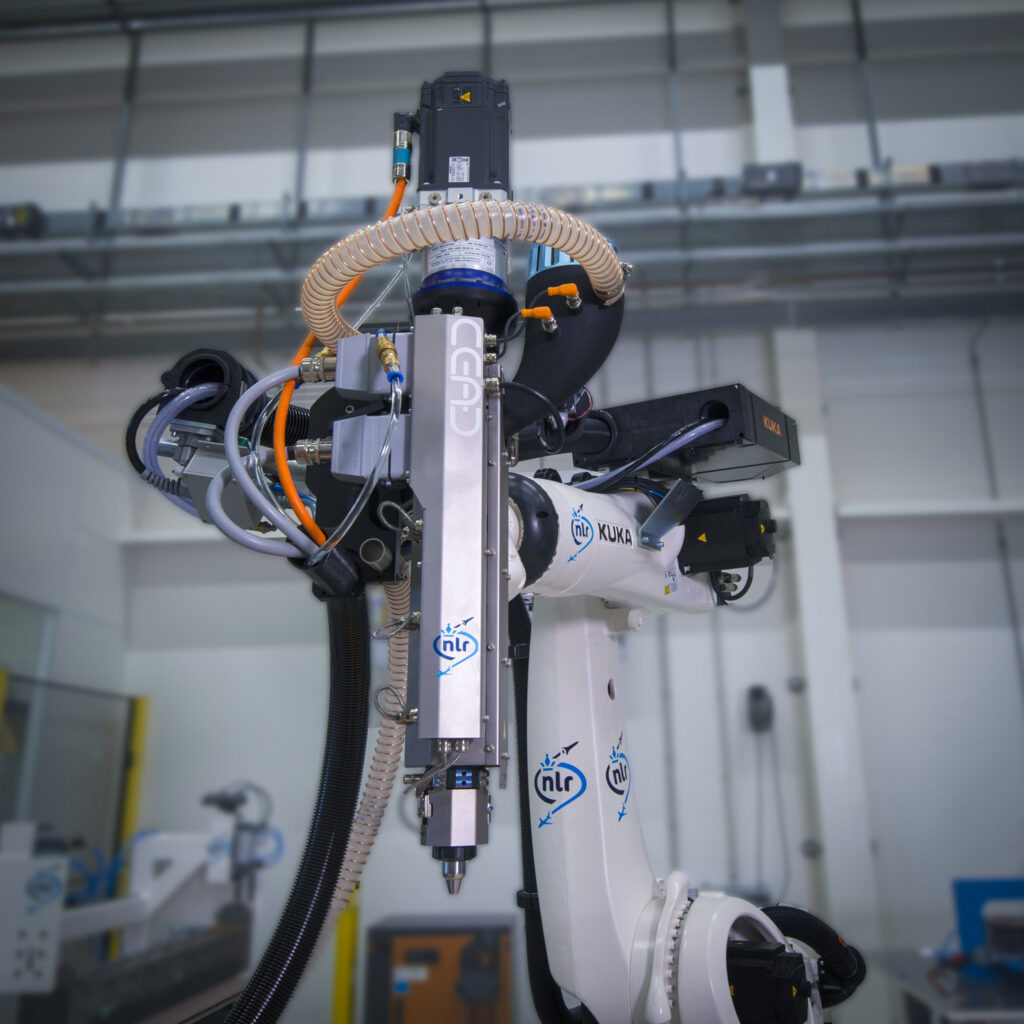
De opstelling omvat ook het droogsysteem VISMEC Dryplus, dat is uitgebreid met een automatische hopperlader voor printtaken van meer dan acht uur. Correcte droging van het materiaal voor het printen is essentieel om onderdelen van goede kwaliteit te krijgen, omdat sommige materialen veel vocht kunnen absorberen.
In de komende maanden bevat de opstelling ook een verwarmd bed dat de kwaliteit en de hechting van het materiaal aan het printoppervlak verbetert, doordat het de warmte in de eerste lagen van het product vasthoudt.
Toekomstige toepassingen
“Hoewel de focus momenteel ligt op het printen van verstijvingsstructuren zoals honingraten of rasters, heeft deze technologie bewezen geschikt te zijn voor andere toepassingen zoals tooling”, zegt Ramirez de las Heras.
“LSAM-mallen zijn zeker een snellere en goedkopere oplossing dan de huidige mallen die zijn gemaakt van metalen of composieten. Toch blijft het, afhankelijk van de uiteindelijke toepassing van de mal, nog steeds een uitdaging om de porositeitsniveaus te beheersen en de dimensionale stabiliteit nauwkeurig te voorspellen.”
De NLR-afdeling zal dit onderzoek voortzetten en verdere oplossingen ontwikkelen om het LSAM-proces te verbeteren en het volledige potentieel ervan te benutten.
Wilt u meer weten? Bekijk hier de sectie ‘Prototyping & Manufacturing’ op onze website hier.